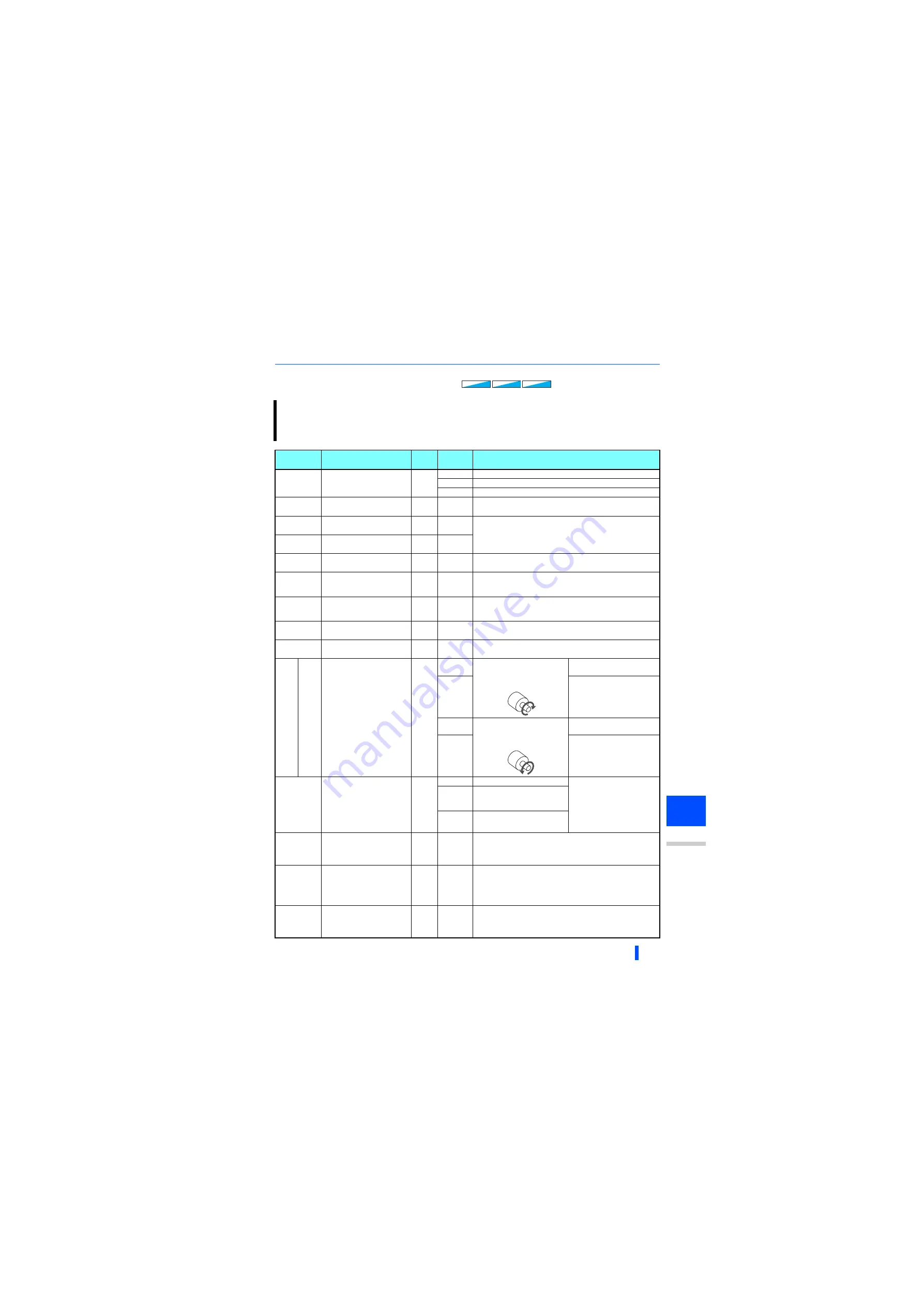
(A) Application parameters
473
5
GROUP
A
5.14.9
Orientation control
The inverter can adjust the stop position (Orientation control) using a position detector (encoder) attached to a place
such as the main shaft of the machine.
A vector control compatible option is required.
Because
Pr.350 Stop position command selection
is initially set to "9999", the orientation control function is invalid.
Pr.
Name
Initial
value
Setting
range
Description
350
A510
Stop position command
selection
9999
0
Internal stop position command
(Pr.356)
1
External stop position command (FR-A8AX 16-bit data)
9999
Orientation control invalid
351
A526
Orientation speed
2 Hz
0 to 30 Hz
Turning ON the X22 signal decelerates the motor speed to the set
value.
352
A527
Creep speed
0.5 Hz
0 to 10 Hz
After the speed reaches the orientation speed, the speed
decreases to the creep speed set in
Pr.352
as soon as the current
position pulse reaches the creep switchover position set in
Pr.353
.
353
A528
Creep switchover
position
511
0 to 16383
354
A529
Position loop switchover
position
96
0 to 8191
As soon as the current position pulses reach the set position loop
switchover position, control is changed to the position loop.
355
A530
DC injection brake start
position
5
0 to 255
After the motor moves into the position loop, the motor stops by
the DC injection brake when the current position pulses reach the
specified start position of the DC injection brake.
356
A531
Internal stop position
command
0
0 to 16383
When "0" is set in
Pr.350
, the internal position command is
activated and the setting value of
Pr.356
becomes the stop
position.
357
A532
Orientation in-position
zone
5
0 to 255
Set the in-position width at a stop of the orientation.
358
A533
Servo torque selection
1
0 to 13
Operation at orientation completion can be selected.
359
C141
852
C241
Encoder rotation
direction
1
0
Set when using a motor for
which forward rotation (encoder)
is clockwise (CW) viewed from
the shaft
Set for the operation at 120 Hz
or less.
100
Set for the operation at a
frequency higher than 120 Hz.
1
Set when using a motor for
which forward rotation (encoder)
is counterclockwise (CCW)
viewed from the shaft
Set for the operation at 120 Hz
or less.
101
Set for the operation at a
frequency higher than 120 Hz.
360
A511
16-bit data selection
0
0
Speed command
When
Pr.350
= "1" is set and
the FR-A8AX is mounted
together, set the stop position
using 16-bit data.
Stop position command is
input as binary regardless of
the
Pr.304
setting.
1
16-bit data is used as the
external position command as
is.
2 to 127
Set the stop position by dividing
up to 128 stop positions.
361
A512
Position shift
0
0 to 16383
Shift the home position using a compensation value without
changing the home position of the encoder. The stop position is a
position obtained by adding the setting of
Pr.361
to the position
command.
362
A520
Orientation position loop
gain
1
0.1 to 100
When the servo torque function is selected using
Pr.358
, the
output frequency for generating servo torque gradually increases
to the creep speed of
Pr.352
according to the slope set in
Pr.362
.
Although the operation becomes faster when the value is
increased, hunting may occur in the machine.
363
A521
Completion signal output
delay time
0.5 s
0 to 5 s
The orientation complete signal turns ON after going into the in-
position width and waiting for the set time. Also, the signal turns
OFF after going out of the in-position width and waiting for the set
time.
V/F
V/F
V/F
Magnetic flux
Magnetic flux
Magnetic flux Vector
Vector
Vector
CW
CCW
Содержание 800 Series
Страница 11: ...MEMO 10 ...
Страница 17: ...MEMO 16 ...
Страница 95: ...MEMO 94 ...
Страница 671: ...MEMO 670 ...
Страница 681: ...MEMO 680 ...