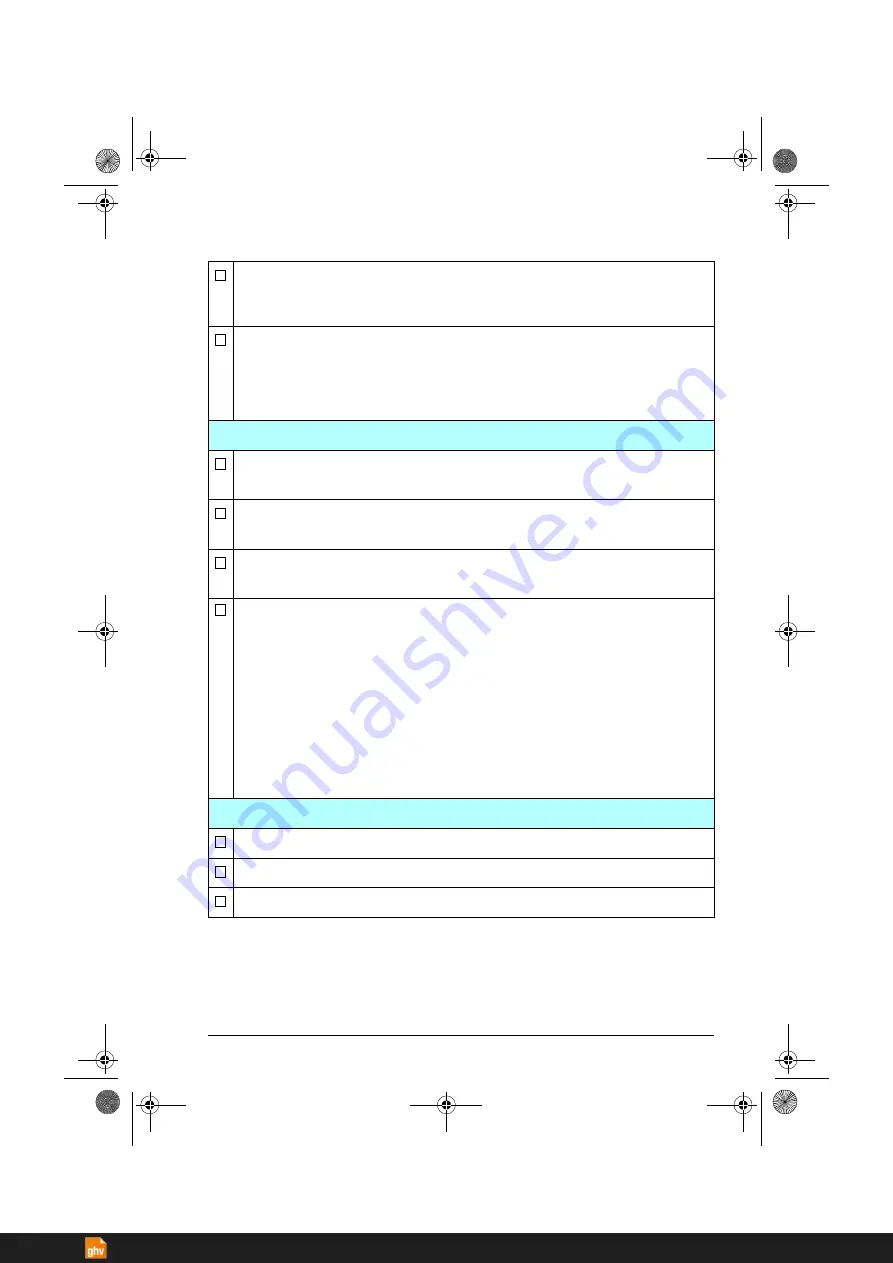
Appendix A - ACS380 in crane applications 523
Set the speed limits.
30.11
Minimum speed
30.12
Maximum speed
46.01
Speed scaling
Set the torque and current limits.
30.17
Maximum current
= Nominal motor current [A]
30.19
Minimum torque 1
= Nominal motor torque (for example, -100%)
30.20
Maximum torque 1
= Nominal motor torque (for example, 100%)
Note:
After the trial run, you must set the above limits according to the application
requirements.
Brake control settings
Make sure that the brake control logic is activated.
44.06
Brake control enable
=
Selected
10.24
RO1 source
=
Brake command
Define brake opening and closing delays.
44.08
Brake open delay
= eg. 1 s
44.13
Brake close delay
= eg. 1 s
Select the source for the brake acknowledgment signal.
44.07
Brake acknowledge selection
= as per the application requirements (eg. DI3 or No
acknowledge)
If you set up a hoist drive, set the parameters as below:
44.09
Brake open torque source
=
Brake open torque
44.10
Brake open torque
= 30% (this value works as minimum value when
Brake torque
memory
is selected)
44.202
Torque proving
=
Selected
44.203
Torque proving reference
= 25.0
44.204
Brake system check time
= 0.30
If you set up a trolley or long travel drive, set the parameters as below:
44.09
Brake open torque source
=
Zero
44.10
Brake open torque
= 0%
44.202
Torque proving
=
Not selected
Note:
These values are also recommended when you use scalar control mode (
99.04
) for
the hoist drive.
Trial run
Do a trial run with an empty hook.
Make sure that the brake and safety circuits are working.
Do a trial run with real load.
ACS380 FW.book Page 523 Friday, May 4, 2018 4:18 PM
ghv Vertriebs-GmbH
| Am Schammacher Feld 47 | 85567 Grafing | T 49 80 92 81 89 0 | [email protected] |
www.ghv.de