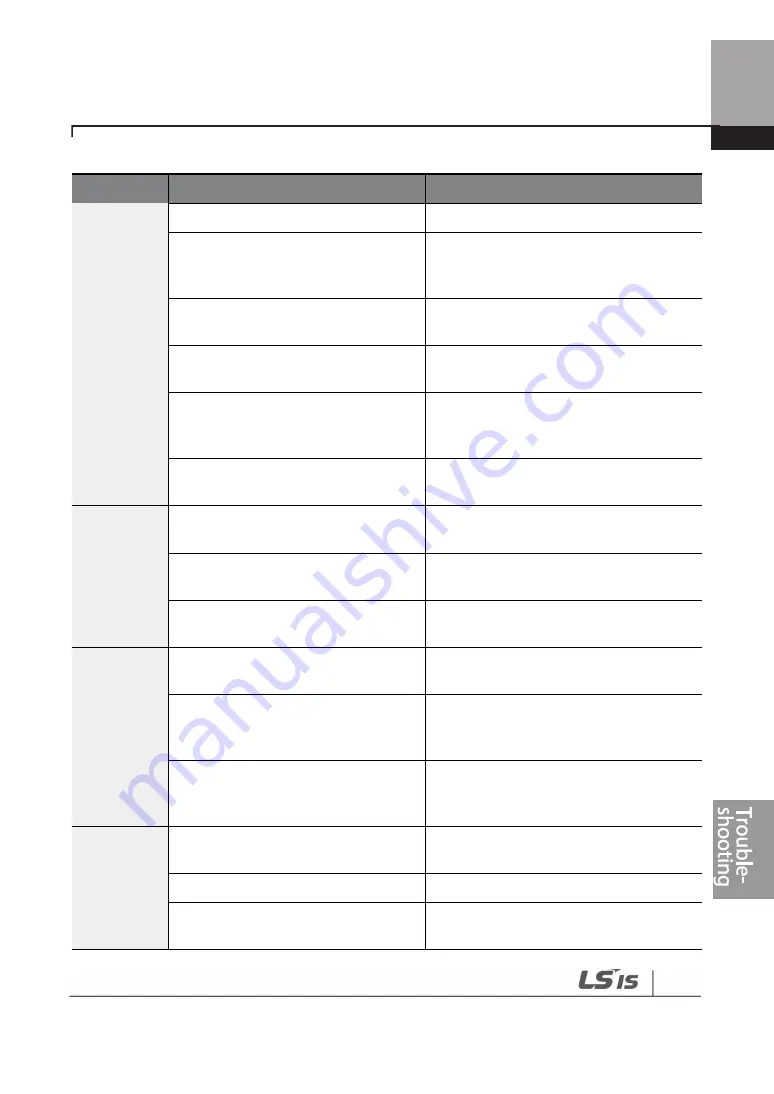
567
Troubleshooting
Type
Cause
Remedy
problem.
models with lower capacity.
The set value for underload level (PRT-
24) is less than the system’s minimum
load.
Reduce the set value for the underload
level.
Over
Current1
Acc/Dec time is too short, compared to
load inertia (GD
2
).
Increase Acc/Dec time.
The inverter load is greater than the
rated capacity.
Replace the inverter with a model that has
increased capacity.
The inverter supplied an output while
the motor was idling.
Operate the inverter after the motor has
stopped or use the speed search function
(CON-70).
The mechanical brake of the motor is
operating too fast.
Check the mechanical brake.
Over Voltage
Deceleration time is too short for the
load inertia (GD
2
).
Increase the acceleration time.
A generative load occurs at the inverter
output.
Use the braking unit.
The input voltage is too high.
Determine if the input voltage is above the
specified value.
Low Voltage
The input voltage is too low.
Determine if the input voltage is below the
specified value.
A load greater than the power capacity
is connected to the system ( a welder,
direct motor connection, etc.)
Increase the power capacity.
The magnetic contactor connected to
the power source has a faulty
connection.
Replace the magnetic contactor.
Low
Voltage2
The input voltage has decreased during
the operation.
Determine if the input voltage is above the
specified value.
An input phase-loss has occurred.
Check the input wiring.
The power supply magnetic contactor
is faulty.
Replace the magnetic contractor.
Summary of Contents for 6731001500
Page 1: ......
Page 17: ...Preparing the Installation 4 37 90kW 3 Phase ...
Page 18: ...Preparing the Installation 5 110 132kW 3 Phase ...
Page 19: ...Preparing the Installation 6 160 185kW 3 Phase ...
Page 20: ...Preparing the Installation 7 220 250kW 3 Phase ...
Page 21: ...Preparing the Installation 8 315 400kW 3 Phase ...
Page 22: ...Preparing the Installation 9 500kW 3 Phase ...
Page 34: ...21 Installing the Inverter 400 V 220 500kW ...
Page 50: ...37 Installing the Inverter Inputand OutputControlTerminalBlockWiringDiagram 5 5 90kW ...
Page 66: ...Perform BasicOperations 53 ...
Page 106: ...93 Learning BasicFeatures 0 10V InputVoltageSettingDetails V1 Quantizing ...
Page 107: ...94 Learning BasicFeatures ...
Page 187: ...174 Learning Advanced Features PIDCommandBlock ...
Page 188: ...175 Learning Advanced Features ...
Page 189: ...176 Learning Advanced Features PIDFeedbackBlock ...
Page 190: ...177 Learning Advanced Features PIDOutputBlock ...
Page 191: ...178 Learning Advanced Features PIDOutputModeBlock ...
Page 205: ...192 Learning Advanced Features EPID1Controlblock ...
Page 206: ...193 Learning Advanced Features EPID2Controlblock ...
Page 228: ...215 Learning Advanced Features ...
Page 244: ...231 Learning Advanced Features TheTime Chartfor the Exception Day ...
Page 260: ...247 Learning Advanced Features SpeedSearchOperation SettingDetails ...
Page 405: ...392 RS 485 Communication Features 7 3 9 2 Control Area Parameter Read Write ...
Page 555: ...Table ofFunctions 542 8 16 4 CoolingTower MC4 Group ...
Page 558: ...Tableof Functions 545 8 16 5 Circulation Pump MC5 Group ...
Page 562: ...Tableof Functions 549 8 16 6 Vacuum Pump MC6 Group ...
Page 588: ...575 Troubleshooting ...
Page 608: ...TechnicalSpecification 595 11 3 External Dimensions 0 75 30kW 3 phase 37 90kW 3 phase ...
Page 609: ...TechnicalSpecification 596 110 185kW 3 phase ...
Page 632: ...TechnicalSpecification 619 400 V 37 500 kW Current Derating Rate ...
Page 643: ...630 ...
Page 644: ...631 ...
Page 645: ...632 ...