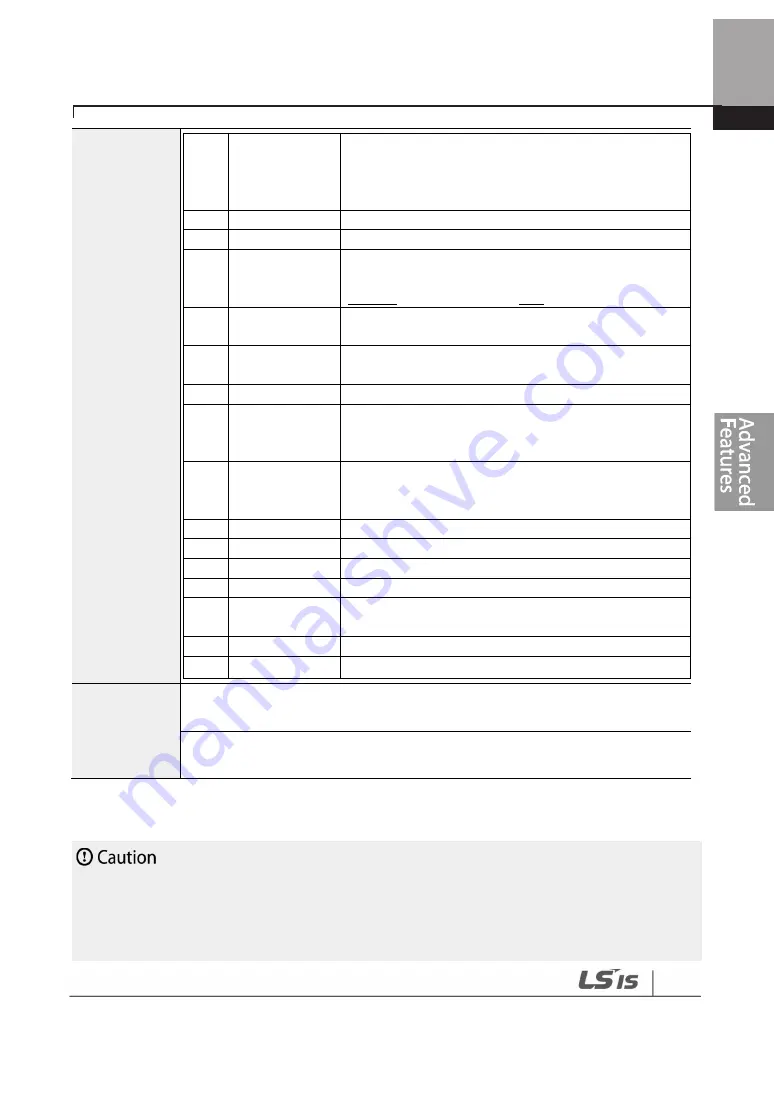
313
Learning Advanced Features
•
FDT-1 and FDT-2 functions are related to the frequency setting of the inverter. If the inverter
enters standby mode by pressing the off key during auto mode operation, FDT-1 and FDT-2
function operation may be different because the set frequency of the inverter is different
compared to the set frequency of the auto mode.
26
On/Off Control Outputs a signal using an analog input value as a
standard.
Refer to 5.45 Multi-function Output On/Off Control on
page 259 .
27
Fire Mode
Outputs a signal when Fire mode is in operation.
28
Pipe Break
Outputs a signal when a pipe is broken.
29
Damper Err
Outputs a signal when damper open signal is not
entered. For more details, refer to 0
Damper
Operation on page
194.
30
Lubrication
Outputs a signal when a lubrication function is in
operation.
31
PumpClean Sel Outputs a signal when a pump cleaning function is in
operation.
32
LDT Trip
Outputs a signal when an LDT trip occurs.
33
Damper
Control
Outputs a signal when a damper open signal is set at
IN-65–71 multi-function terminals and run command
is on.
34
CAP.Warning
Outputs a signal when value of the PRT-85 is lower
than the value of the PRT-86 (CAP life cycle
examination do not operate properly).
35
Fan Exchange
Outputs a signal when fan needs to be replaced.
36
AUTO State
Outputs a signal in AUTO mode.
37
HAND State
Outputs a signal in HAND mode.
38
TO
Outputs a signal at pulse output.
39
Except Date
Outputs a signal when operating the exception day
schedule.
40
KEB Operating
Outputs a signal at KEB operation.
41
BrokenBelt
Outputs a signal when a Broken belt is in operation.
OUT-36 Q1
Define
Select an output item for the multi-function output terminal (Q1) of the terminal
block. Q1 stands for the open collector TR output.
OUT-41 DO
State
Used to check On/Off state of the D0 by each bit.
Summary of Contents for 6731001500
Page 1: ......
Page 17: ...Preparing the Installation 4 37 90kW 3 Phase ...
Page 18: ...Preparing the Installation 5 110 132kW 3 Phase ...
Page 19: ...Preparing the Installation 6 160 185kW 3 Phase ...
Page 20: ...Preparing the Installation 7 220 250kW 3 Phase ...
Page 21: ...Preparing the Installation 8 315 400kW 3 Phase ...
Page 22: ...Preparing the Installation 9 500kW 3 Phase ...
Page 34: ...21 Installing the Inverter 400 V 220 500kW ...
Page 50: ...37 Installing the Inverter Inputand OutputControlTerminalBlockWiringDiagram 5 5 90kW ...
Page 66: ...Perform BasicOperations 53 ...
Page 106: ...93 Learning BasicFeatures 0 10V InputVoltageSettingDetails V1 Quantizing ...
Page 107: ...94 Learning BasicFeatures ...
Page 187: ...174 Learning Advanced Features PIDCommandBlock ...
Page 188: ...175 Learning Advanced Features ...
Page 189: ...176 Learning Advanced Features PIDFeedbackBlock ...
Page 190: ...177 Learning Advanced Features PIDOutputBlock ...
Page 191: ...178 Learning Advanced Features PIDOutputModeBlock ...
Page 205: ...192 Learning Advanced Features EPID1Controlblock ...
Page 206: ...193 Learning Advanced Features EPID2Controlblock ...
Page 228: ...215 Learning Advanced Features ...
Page 244: ...231 Learning Advanced Features TheTime Chartfor the Exception Day ...
Page 260: ...247 Learning Advanced Features SpeedSearchOperation SettingDetails ...
Page 405: ...392 RS 485 Communication Features 7 3 9 2 Control Area Parameter Read Write ...
Page 555: ...Table ofFunctions 542 8 16 4 CoolingTower MC4 Group ...
Page 558: ...Tableof Functions 545 8 16 5 Circulation Pump MC5 Group ...
Page 562: ...Tableof Functions 549 8 16 6 Vacuum Pump MC6 Group ...
Page 588: ...575 Troubleshooting ...
Page 608: ...TechnicalSpecification 595 11 3 External Dimensions 0 75 30kW 3 phase 37 90kW 3 phase ...
Page 609: ...TechnicalSpecification 596 110 185kW 3 phase ...
Page 632: ...TechnicalSpecification 619 400 V 37 500 kW Current Derating Rate ...
Page 643: ...630 ...
Page 644: ...631 ...
Page 645: ...632 ...