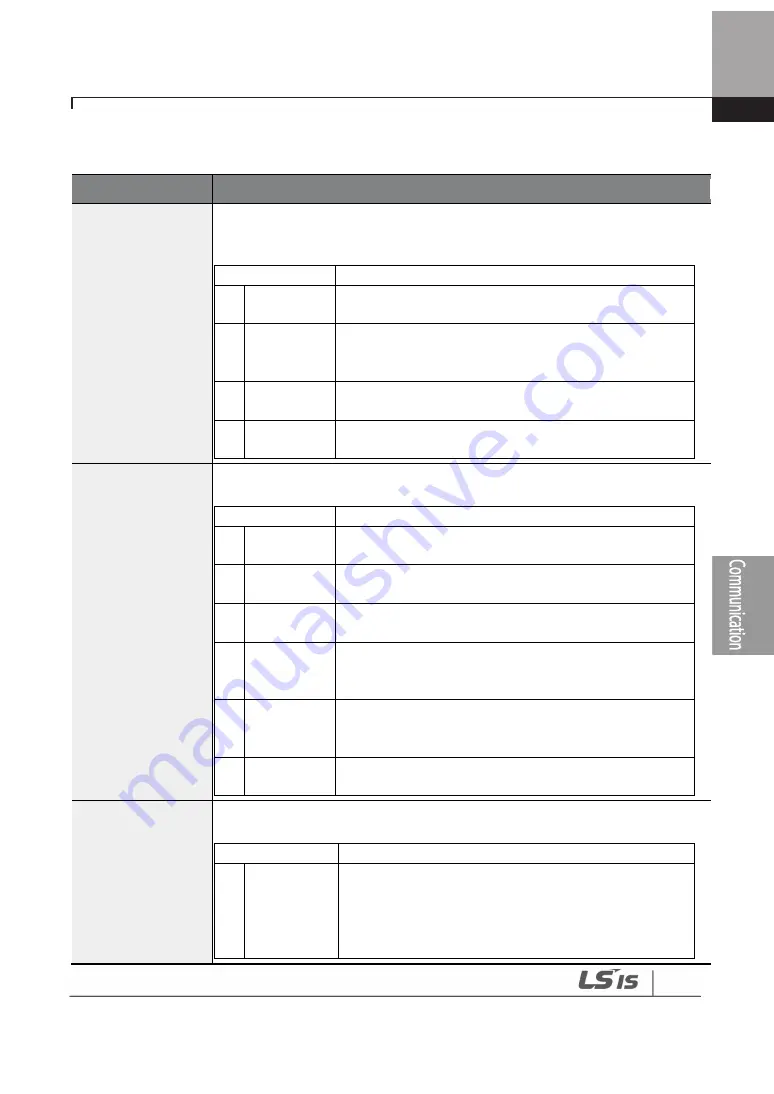
335
Learning Protection Features
Speed Command Loss Setting Details
Code
Description
PRT-11 Lost KPD
Mode
Set the operation command source to keypad. If there is a communication error
with the keypad or connection problem between the keypad and the inverter,
select the inverter’s operation.
Setting
Function
0
None
The speed command immediately becomes the
operation frequency without any protection function.
1
Warning
Select 24: Lost keypad from OUT-31–36, one of the multi
function terminal blocks, outputs a relevant warning
signal when abnormal operating conditions arise.
2
Free-Run
The inverter blocks output. The motor performs in free-
run condition.
3
Dec
The motor decelerates and then stops at the time set at
PRT-07 (Trip Dec Time).
PRT-12 Lost Cmd
Mode
In situations when speed commands are lost, the inverter can be configured to
operate in a specific mode:
Setting
Function
0
None
The speed command immediately becomes the
operation frequency without any protection function.
1
Free-Run
The inverter blocks output. The motor performs in free-
run condition.
2
Dec
The motor decelerates and then stops at the time set at
PRT-07 (Trip Dec Time).
3
Hold Input
The inverter calculates the average input value for 10
seconds before the loss of the speed command and
uses it as the speed reference.
4
Hold
Output
The inverter calculates the average output value for 10
seconds before the loss of the speed command and
uses it as the speed reference.
5
Lost Preset
The inverter operates at the frequency set at PRT- 14
(Lost Preset F).
PRT-15 AI Lost Level,
PRT-13 Lst Cmd
Time
Configure the voltage and decision time for speed command loss when using
analog input.
Setting
Function
0
Half of x1
Based on the values set at IN-08 and IN-12, a protective
operation starts when the input signal is reduced to half
of the initial value of the analog input set using the
speed command (DRV-01) and it continues for the time
(speed loss decision time) set at PRT-13 (Lost Cmd
Summary of Contents for 6731001500
Page 1: ......
Page 17: ...Preparing the Installation 4 37 90kW 3 Phase ...
Page 18: ...Preparing the Installation 5 110 132kW 3 Phase ...
Page 19: ...Preparing the Installation 6 160 185kW 3 Phase ...
Page 20: ...Preparing the Installation 7 220 250kW 3 Phase ...
Page 21: ...Preparing the Installation 8 315 400kW 3 Phase ...
Page 22: ...Preparing the Installation 9 500kW 3 Phase ...
Page 34: ...21 Installing the Inverter 400 V 220 500kW ...
Page 50: ...37 Installing the Inverter Inputand OutputControlTerminalBlockWiringDiagram 5 5 90kW ...
Page 66: ...Perform BasicOperations 53 ...
Page 106: ...93 Learning BasicFeatures 0 10V InputVoltageSettingDetails V1 Quantizing ...
Page 107: ...94 Learning BasicFeatures ...
Page 187: ...174 Learning Advanced Features PIDCommandBlock ...
Page 188: ...175 Learning Advanced Features ...
Page 189: ...176 Learning Advanced Features PIDFeedbackBlock ...
Page 190: ...177 Learning Advanced Features PIDOutputBlock ...
Page 191: ...178 Learning Advanced Features PIDOutputModeBlock ...
Page 205: ...192 Learning Advanced Features EPID1Controlblock ...
Page 206: ...193 Learning Advanced Features EPID2Controlblock ...
Page 228: ...215 Learning Advanced Features ...
Page 244: ...231 Learning Advanced Features TheTime Chartfor the Exception Day ...
Page 260: ...247 Learning Advanced Features SpeedSearchOperation SettingDetails ...
Page 405: ...392 RS 485 Communication Features 7 3 9 2 Control Area Parameter Read Write ...
Page 555: ...Table ofFunctions 542 8 16 4 CoolingTower MC4 Group ...
Page 558: ...Tableof Functions 545 8 16 5 Circulation Pump MC5 Group ...
Page 562: ...Tableof Functions 549 8 16 6 Vacuum Pump MC6 Group ...
Page 588: ...575 Troubleshooting ...
Page 608: ...TechnicalSpecification 595 11 3 External Dimensions 0 75 30kW 3 phase 37 90kW 3 phase ...
Page 609: ...TechnicalSpecification 596 110 185kW 3 phase ...
Page 632: ...TechnicalSpecification 619 400 V 37 500 kW Current Derating Rate ...
Page 643: ...630 ...
Page 644: ...631 ...
Page 645: ...632 ...