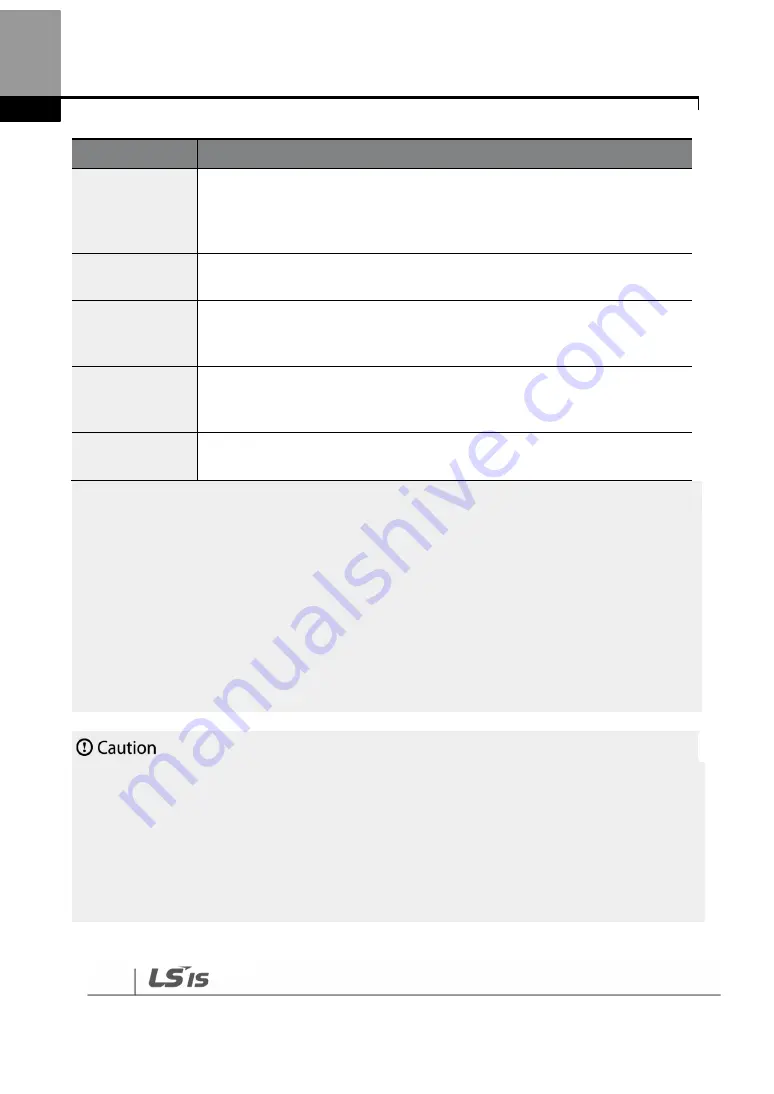
238
Learning Advanced Features
Code
Description
CON-78
KEB Start Lev,
CON-79
KEB Stop Lev
Sets the start and stop points of the kinetic energy buffering operation. The set
values must be based on the low voltage trip level at 100%, and the stop level
(CON-79) must be set higher than the start level (CON-78).
CON-80
KEB Slip Gain
Used to prevent malfunctions caused by low voltage from initial kinetic energy
buffering occurring due to power interruptions.
CON-81
KEB P Gain
Used to maintain the voltage during the kinetic energy buffering operation. It
operates the inverter by modifying the set value to prevent malfunctions
caused by low voltage after power interruptions.
CON-82
KEB I Gain
Used to maintain the voltage during the kinetic energy buffering operation.
Sets the gain value to maintain the operation until the frequency stops during
the kinetic energy buffering operation.
CON-83
KEB Acc Time
Sets the acceleration time for the frequency reference when the inverter’s
operation becomes normal after the kinetic energy buffering operation.
Note
•
The KEB functions may perform differently depending on the size of the loads. The KEB Gains can
be set for a better performance.
•
If a low voltage trip occurs after a power interruption, it indicates the load inertia and level are
high. In such cases, the KEB functions can be performed better by increasing the KEB I Gain and
the KEB Slip Gain.
•
If motor vibration or torque variation occurs during the KEB function operation after power
interruptions, the KEB functions can be performed better by increasing the KEB P Gain or
decreasing the KEB I Gain.
Depending on the duration of instantaneous power interruptions and the amount of load inertia, a low
voltage trip may occur even during a kinetic energy buffering operation. Motors may vibrate during
kinetic energy buffering operation for some loads, except for variable torque loads (for example, fan or
pump loads).
Summary of Contents for 6731001500
Page 1: ......
Page 17: ...Preparing the Installation 4 37 90kW 3 Phase ...
Page 18: ...Preparing the Installation 5 110 132kW 3 Phase ...
Page 19: ...Preparing the Installation 6 160 185kW 3 Phase ...
Page 20: ...Preparing the Installation 7 220 250kW 3 Phase ...
Page 21: ...Preparing the Installation 8 315 400kW 3 Phase ...
Page 22: ...Preparing the Installation 9 500kW 3 Phase ...
Page 34: ...21 Installing the Inverter 400 V 220 500kW ...
Page 50: ...37 Installing the Inverter Inputand OutputControlTerminalBlockWiringDiagram 5 5 90kW ...
Page 66: ...Perform BasicOperations 53 ...
Page 106: ...93 Learning BasicFeatures 0 10V InputVoltageSettingDetails V1 Quantizing ...
Page 107: ...94 Learning BasicFeatures ...
Page 187: ...174 Learning Advanced Features PIDCommandBlock ...
Page 188: ...175 Learning Advanced Features ...
Page 189: ...176 Learning Advanced Features PIDFeedbackBlock ...
Page 190: ...177 Learning Advanced Features PIDOutputBlock ...
Page 191: ...178 Learning Advanced Features PIDOutputModeBlock ...
Page 205: ...192 Learning Advanced Features EPID1Controlblock ...
Page 206: ...193 Learning Advanced Features EPID2Controlblock ...
Page 228: ...215 Learning Advanced Features ...
Page 244: ...231 Learning Advanced Features TheTime Chartfor the Exception Day ...
Page 260: ...247 Learning Advanced Features SpeedSearchOperation SettingDetails ...
Page 405: ...392 RS 485 Communication Features 7 3 9 2 Control Area Parameter Read Write ...
Page 555: ...Table ofFunctions 542 8 16 4 CoolingTower MC4 Group ...
Page 558: ...Tableof Functions 545 8 16 5 Circulation Pump MC5 Group ...
Page 562: ...Tableof Functions 549 8 16 6 Vacuum Pump MC6 Group ...
Page 588: ...575 Troubleshooting ...
Page 608: ...TechnicalSpecification 595 11 3 External Dimensions 0 75 30kW 3 phase 37 90kW 3 phase ...
Page 609: ...TechnicalSpecification 596 110 185kW 3 phase ...
Page 632: ...TechnicalSpecification 619 400 V 37 500 kW Current Derating Rate ...
Page 643: ...630 ...
Page 644: ...631 ...
Page 645: ...632 ...