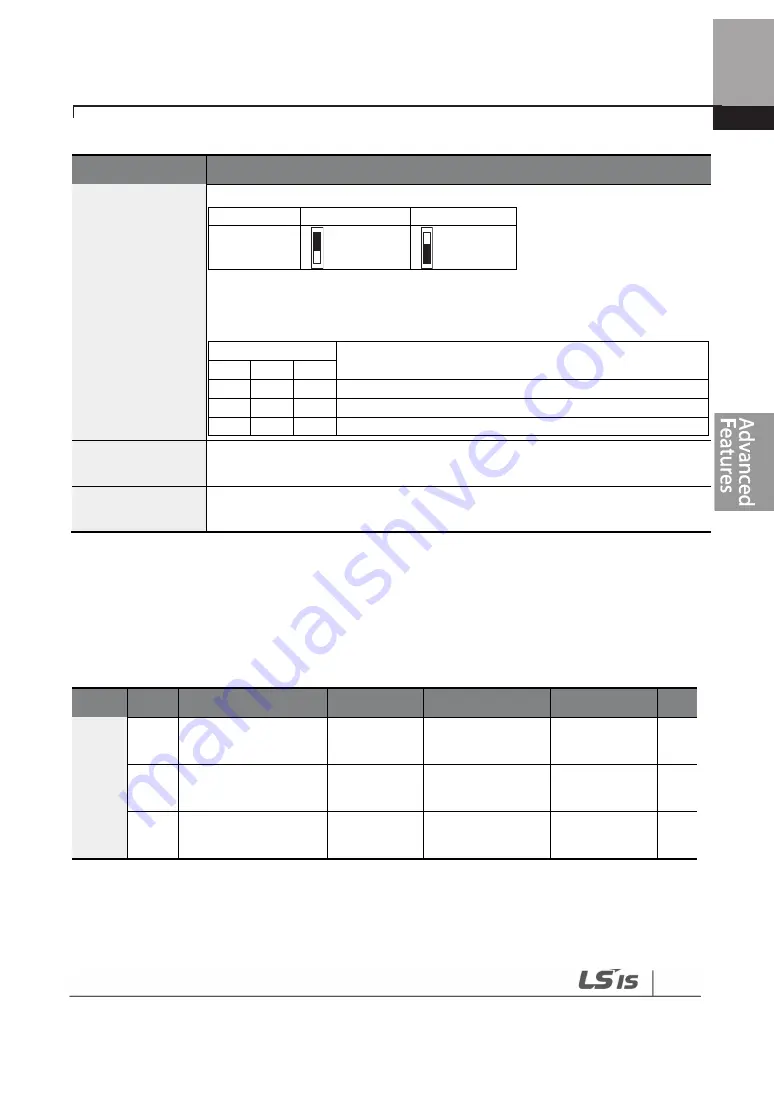
315
Learning Advanced Features
Fault Trip Output by Multi-function Output Terminal and Relay - Setting Details
5.48.3
Multi-function Output Terminal Delay Time Settings
Set on-delay and off-delay times separately to control the output terminal and relay operation
times. The delay time set at codes OUT-50–51 applies to multi-function output terminal (Q1) and
relay, except when the multi-function output function is in fault trip mode.
Group Code
Name
LCD Display
Parameter Setting
Setting Range
Unit
OUT
50
Multi-function output
On delay
DO On Delay 0.00
0.00–100.00
sec
51
Multi-function output
Off delay
DO Off Delay 0.00
0.00–100.00
sec
52
Select multi-function
output terminal
DO NC/NO
Sel
000000*
00–11
bit
*Multi-function output terminals are numbered. Starting from the right (number 1), the number
increases to the left.
Code
Description
OUT-30
Trip Out Mode
Fault trip relay operates based on the fault trip output settings.
Item
bit on
bit off
Keypad
display
Select a fault trip output terminal/relay and select ‘29’ (Trip Mode) at codes OUT- 31–
33. When a fault trip occurs in the inverter, the relevant terminal and relay will
operate. Depending on the fault trip type, terminal and relay operation can be
configured as shown in the table below.
Setting
Function
bit3 bit2
bit1
Operates when low voltage fault trips occur
Operates when fault trips other than low voltage occur
Operates when auto restart fails (PRT-08–09)
OUT-31–35 Relay1–
5
Set relay output (Relay 1–5).
OUT-36
Q1 Define
Select output for multi-function output terminal (Q1). Q1 is open collector TR output.
Summary of Contents for 6731001500
Page 1: ......
Page 17: ...Preparing the Installation 4 37 90kW 3 Phase ...
Page 18: ...Preparing the Installation 5 110 132kW 3 Phase ...
Page 19: ...Preparing the Installation 6 160 185kW 3 Phase ...
Page 20: ...Preparing the Installation 7 220 250kW 3 Phase ...
Page 21: ...Preparing the Installation 8 315 400kW 3 Phase ...
Page 22: ...Preparing the Installation 9 500kW 3 Phase ...
Page 34: ...21 Installing the Inverter 400 V 220 500kW ...
Page 50: ...37 Installing the Inverter Inputand OutputControlTerminalBlockWiringDiagram 5 5 90kW ...
Page 66: ...Perform BasicOperations 53 ...
Page 106: ...93 Learning BasicFeatures 0 10V InputVoltageSettingDetails V1 Quantizing ...
Page 107: ...94 Learning BasicFeatures ...
Page 187: ...174 Learning Advanced Features PIDCommandBlock ...
Page 188: ...175 Learning Advanced Features ...
Page 189: ...176 Learning Advanced Features PIDFeedbackBlock ...
Page 190: ...177 Learning Advanced Features PIDOutputBlock ...
Page 191: ...178 Learning Advanced Features PIDOutputModeBlock ...
Page 205: ...192 Learning Advanced Features EPID1Controlblock ...
Page 206: ...193 Learning Advanced Features EPID2Controlblock ...
Page 228: ...215 Learning Advanced Features ...
Page 244: ...231 Learning Advanced Features TheTime Chartfor the Exception Day ...
Page 260: ...247 Learning Advanced Features SpeedSearchOperation SettingDetails ...
Page 405: ...392 RS 485 Communication Features 7 3 9 2 Control Area Parameter Read Write ...
Page 555: ...Table ofFunctions 542 8 16 4 CoolingTower MC4 Group ...
Page 558: ...Tableof Functions 545 8 16 5 Circulation Pump MC5 Group ...
Page 562: ...Tableof Functions 549 8 16 6 Vacuum Pump MC6 Group ...
Page 588: ...575 Troubleshooting ...
Page 608: ...TechnicalSpecification 595 11 3 External Dimensions 0 75 30kW 3 phase 37 90kW 3 phase ...
Page 609: ...TechnicalSpecification 596 110 185kW 3 phase ...
Page 632: ...TechnicalSpecification 619 400 V 37 500 kW Current Derating Rate ...
Page 643: ...630 ...
Page 644: ...631 ...
Page 645: ...632 ...