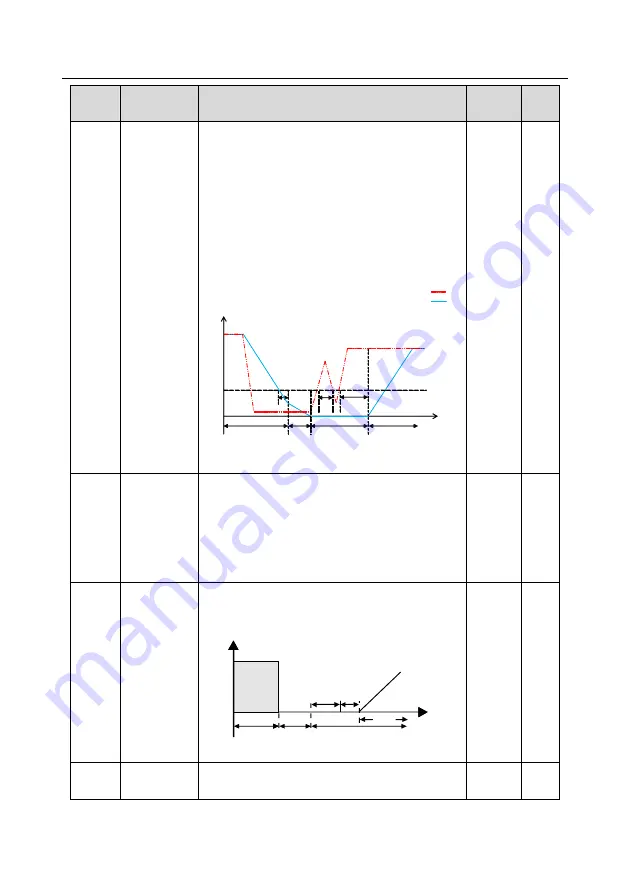
GD310-UL series VFD
Function parameter
-50-
Function
code
Name
Description
Default
value
Modify
P01.20
Hibernation
restore delay
time
This function code determines the hibernation delay
time. When the running frequency of the VFD is
lower than the lower limit one, the VFD will pause to
stand by.
When the set frequency is above the lower limit one
again and it lasts for the time set by P01.20, the VFD
will run automatically.
Note:
The time is the total value when the set
frequency is above the lower limit one.
Sleep
Run
Set frequency curve:
Running frequency curve:
t1 < P01.20, the VFD does not run
t0=P01.34, sleep delay
Run
t2
t1
t0
Frequency lower
limit f0
Frequency f
Time t
Coast to
stop
t1+t2
≥
P01.20, the VFD runs
Setting range: 0.0
–3600.0s (valid when P01.19=2)
0.0s
○
P01.21
Restart after
power off
This function can enable the VFD start or not after
the power off and then power on.
0: Disable
1: Enable, if the starting need is met, the VFD will run
automatically after waiting for the time defined by
P01.22.
0
○
P01.22
The waiting
time of restart
after power off
The function determines the waiting time before the
automatic running of the VFD when powering off and
then powering on.
Output frequency
Running
Power off
Power on
Running
t
t1
t2
t1=P01.22
=
t2=P01.23
=
Setting range: 0.0
–3600.0s (valid when P01.21=1)
1.0s
○
P01.23
Start delay
time
The function determines the brake release after the
running command is given, and the VFD is in a
0.0s
○
Содержание GD310-011P-4-UL
Страница 1: ......
Страница 269: ...6 6 0 0 1 0 0 3 9 3 ...