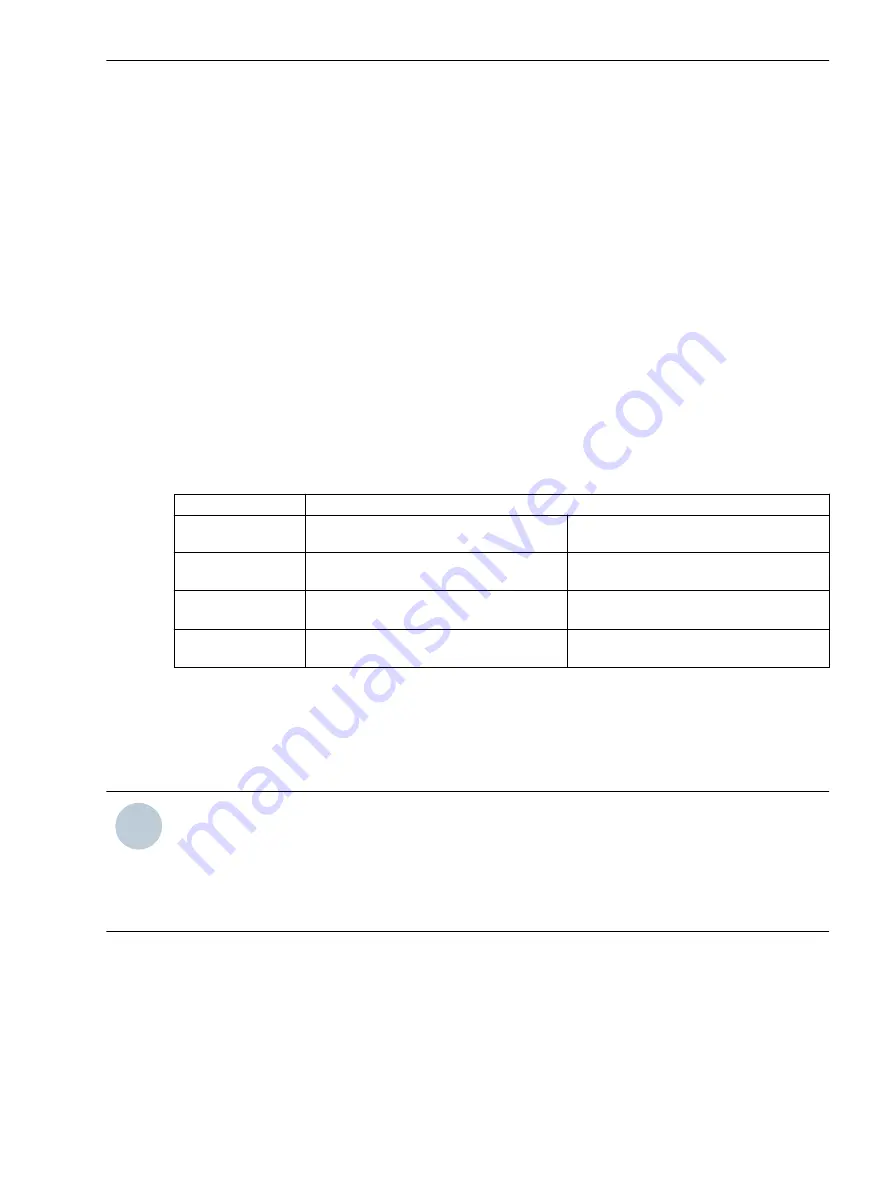
The angle error between voltage transformer and current transformer has a strong influence on the measuring
accuracy. With the parameter
(_:2311:101) Angle correction
, you can correct the angle error. The
following 2 methods are possible here:
•
Determine the angle error from the transformer test report data. Ask the transformer manufacturer for
these values when you order the transformer.
•
While the generator is connected to the power system, measure to determine the angle error (see
chapter
The influence on the power-system voltage makes it very difficult to test high-power generators with a meas-
urement while the generator is connected to the power system. In this case, you must determine the angle
error from the transformer test report data (see chapter
6.38.3.2 Application and Setting Notes
you can use instrument transformers with small angle errors. This is ensured with class 0.2 instrument trans-
formers (voltage and current). The following equation describes the influence of the angle error:
P = 3V
1
I
1
cos(φ
V
+ φ
V,F
- (φ
I
+ φ
I,F
)) = 3V
1
I
1
cos(φ
U
- φ
I
+ (φ
V,F
- φ
I,F
))
The angle error to be corrected results as:
ϕ
Corr
= φ
V,F
- φ
I,F
To rotate in the correct direction, the correction angle is considered with inverted sign inside the unit.
Functional Measured Values
You can use the following functional measured values to check the behavior of the protection function and to
support commissioning. The total power is represented as the measured value.
Measured Value
Description
P1fast
Positive-sequence system active power
calculated per cycle
Angle correction influences the measured
value
Q1fast
Positive-sequence system reactive power
calculated per cycle
Angle correction influences the measured
value
P1avg
Positive-sequence system active power
calculated from
P1fast
over 16 cycles
Input value for Reverse-power protection
Q1avg
Positive-sequence system reactive power
calculated from
Q1fast
over 16 cycles
–
Application and Setting Notes
In the general functionality, you can adjust the parameter
(_:2311:101) Angle correction
. The param-
eter results from the angle error of the primary transformer. In SIPROTEC 5, the input transformers are cali-
brated so that the angle error is negligible. You can assume an error of < 0.1°. There is no difference between
a protection input and an instrument-transformer input.
i
i
NOTE
If you use class 0.2 instrument transformers on the primary side to avoid the influence of the angle, you
can connect a protection device with a protection current transformer without any problems.
Class 0.2 voltage transformers have a maximum admissible angle error of 10 min (0.17°). The angle error
of a class 0.2 measuring current transformer at rated current is approximately 10 min, at 0.2 I
rated
= 15 min,
and at 0.05 I
rated
= 30 min.
Parameter:
Angle correction
•
Default setting
(_:2311:101) Angle correction
= 0°
To determine the correction angle via measurement with the primary system, follow the instructions in
chapter
.
You can use the method that is explained in the following section to derive the necessary correction angle
from the transformer measuring reports.
6.38.3.2
Protection and Automation Functions
6.38 Reverse-Power Protection
SIPROTEC 5, Overcurrent Protection, Manual
811
C53000-G5040-C017-8, Edition 07.2017
Summary of Contents for 7SJ82
Page 8: ...8 SIPROTEC 5 Overcurrent Protection Manual C53000 G5040 C017 8 Edition 07 2017 ...
Page 38: ...38 SIPROTEC 5 Overcurrent Protection Manual C53000 G5040 C017 8 Edition 07 2017 ...
Page 60: ...60 SIPROTEC 5 Overcurrent Protection Manual C53000 G5040 C017 8 Edition 07 2017 ...
Page 186: ...186 SIPROTEC 5 Overcurrent Protection Manual C53000 G5040 C017 8 Edition 07 2017 ...
Page 194: ...194 SIPROTEC 5 Overcurrent Protection Manual C53000 G5040 C017 8 Edition 07 2017 ...
Page 966: ...966 SIPROTEC 5 Overcurrent Protection Manual C53000 G5040 C017 8 Edition 07 2017 ...
Page 1072: ...1072 SIPROTEC 5 Overcurrent Protection Manual C53000 G5040 C017 8 Edition 07 2017 ...
Page 1236: ...1236 SIPROTEC 5 Overcurrent Protection Manual C53000 G5040 C017 8 Edition 07 2017 ...
Page 1306: ...1306 SIPROTEC 5 Overcurrent Protection Manual C53000 G5040 C017 8 Edition 07 2017 ...
Page 1370: ...1370 SIPROTEC 5 Overcurrent Protection Manual C53000 G5040 C017 8 Edition 07 2017 ...
Page 1404: ...1404 SIPROTEC 5 Overcurrent Protection Manual C53000 G5040 C017 8 Edition 07 2017 ...
Page 1576: ...1576 SIPROTEC 5 Overcurrent Protection Manual C53000 G5040 C017 8 Edition 07 2017 ...
Page 1614: ...1614 SIPROTEC 5 Overcurrent Protection Manual C53000 G5040 C017 8 Edition 07 2017 ...
Page 1634: ...1634 SIPROTEC 5 Overcurrent Protection Manual C53000 G5040 C017 8 Edition 07 2017 ...