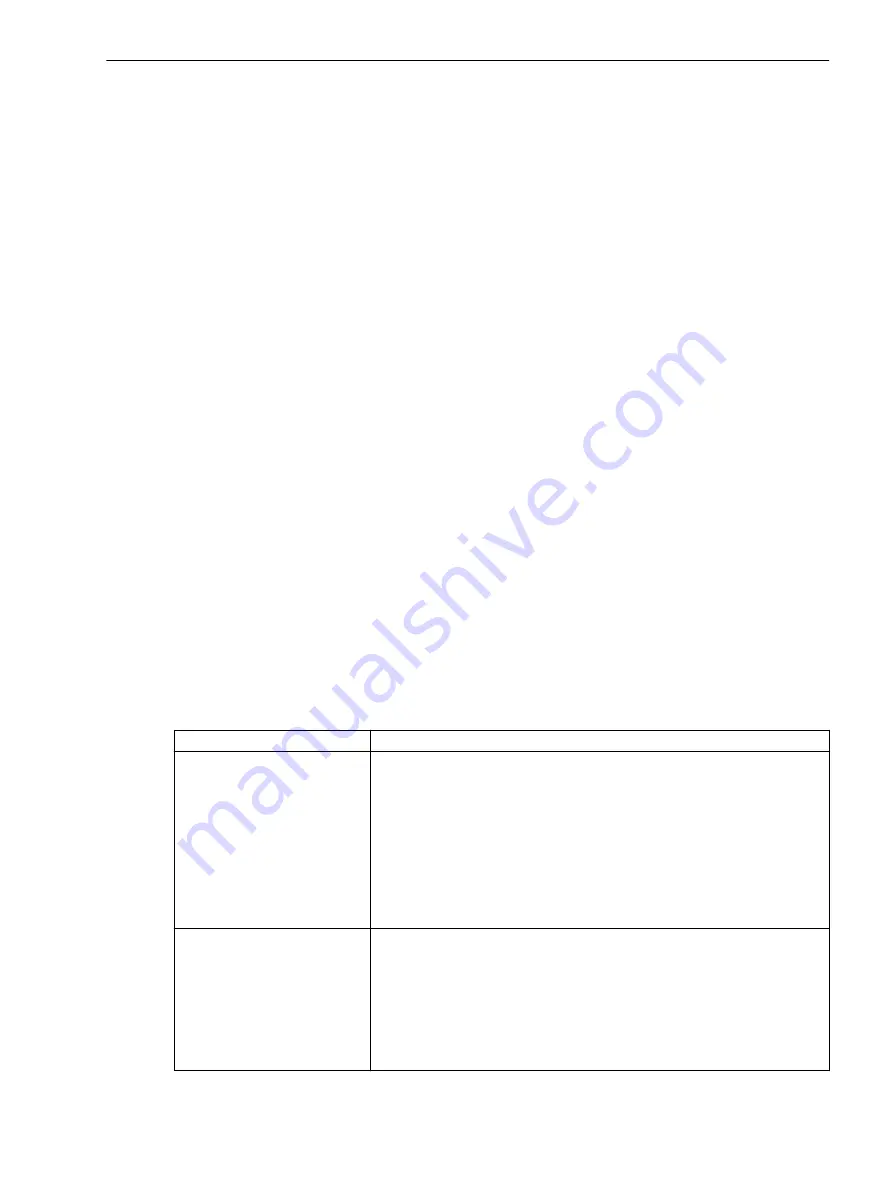
An integrating method of measurement totalizes the weighted time. The weighted time results from the char-
acteristic curve. For this, the time that is associated with the present current value is determined from the
characteristic curve. Once the weighted time exceeds the value 1, the stage operates.
When the measured value falls below the pickup value by 1.045 times (0.95 x 1.1 x threshold value), the
dropout is started. The pickup will be indicated as clearing. You can influence the dropout behavior via setting
parameters. You can select between instantaneous dropout (totalized time is deleted) or dropout according to
the characteristic curve (reduction of totalized time depending on the characteristic curve). The dropout
according to the characteristic curve (disk emulation) is the same as turning back a rotor disk. The weighted
reduction of the time is started from 0.9 of the set threshold value.
The characteristic curve and associated formulas are shown in the Technical data.
Influence On the Operate Curve
The current pickup threshold is decreased proportional to the voltage decrease. Consequently, for a constant
current I the I/Threshold-value ratio is increased and the operate time is reduced. Compared with the standard
curves represented in the Technical Data, the operate curve shifts to the left side as the voltage decreases.
Measuring-Voltage Failure Detection
In case of a measuring-voltage failure detection the input voltage value is automatically set to V
rated
, so that
the pickup threshold factor will be 1.
Blocking of the Time Delay
You can use the binary input signal
>Block delay & op.
to prevent the start of the time delay and thus
also the operate signal. A running time delay is reset. The pickup is indicated and the fault logging and
recording takes place.
Blocking of the Operate Delay and the Operate Signal via the Device-Internal Inrush-Current Detection Function
Blocking of the operate delay and the operate signal via the device-internal Inrush-current detection function
is described in chapter
Application and Setting Notes
Parameter:
Blk. w. inrush curr. detect.
•
Default setting
(_:11491:27) Blk. w. inrush curr. detect.
=
no
Parameter Value
Description
no
The transformer inrush-current detection does not affect the stage. Select
this setting in the following cases:
•
In cases where the device is not used on transformers.
•
In cases where the device is used on transformers and the threshold
value of the stage is set above the maximum inrush current of the
transformer. This applies, for example, to the high-current stage that is
set according to the short-circuit voltage Vsc of the transformer in such
a way that the stage only picks up on faults from the high-voltage side.
The transformer-inrush current cannot become larger than the
maximum transmittable short-circuit current.
yes
When the transformer inrush-current detection detects an inrush current
that would lead to a tripping of the stage, the start of the time delay and
tripping of the stage are blocked.
Select this setting if the device is used on transformers and the threshold
value of the stage is set below the maximum inrush current of the trans-
former. This applies to the overcurrent-protection stage, which is used as a
backup stage with grading time for faults on the undervoltage side of the
transformer.
6.4.3.2
Protection and Automation Functions
6.4 Voltage-Dependent Overcurrent Protection, Phases
SIPROTEC 5, Overcurrent Protection, Manual
363
C53000-G5040-C017-8, Edition 07.2017
Summary of Contents for 7SJ82
Page 8: ...8 SIPROTEC 5 Overcurrent Protection Manual C53000 G5040 C017 8 Edition 07 2017 ...
Page 38: ...38 SIPROTEC 5 Overcurrent Protection Manual C53000 G5040 C017 8 Edition 07 2017 ...
Page 60: ...60 SIPROTEC 5 Overcurrent Protection Manual C53000 G5040 C017 8 Edition 07 2017 ...
Page 186: ...186 SIPROTEC 5 Overcurrent Protection Manual C53000 G5040 C017 8 Edition 07 2017 ...
Page 194: ...194 SIPROTEC 5 Overcurrent Protection Manual C53000 G5040 C017 8 Edition 07 2017 ...
Page 966: ...966 SIPROTEC 5 Overcurrent Protection Manual C53000 G5040 C017 8 Edition 07 2017 ...
Page 1072: ...1072 SIPROTEC 5 Overcurrent Protection Manual C53000 G5040 C017 8 Edition 07 2017 ...
Page 1236: ...1236 SIPROTEC 5 Overcurrent Protection Manual C53000 G5040 C017 8 Edition 07 2017 ...
Page 1306: ...1306 SIPROTEC 5 Overcurrent Protection Manual C53000 G5040 C017 8 Edition 07 2017 ...
Page 1370: ...1370 SIPROTEC 5 Overcurrent Protection Manual C53000 G5040 C017 8 Edition 07 2017 ...
Page 1404: ...1404 SIPROTEC 5 Overcurrent Protection Manual C53000 G5040 C017 8 Edition 07 2017 ...
Page 1576: ...1576 SIPROTEC 5 Overcurrent Protection Manual C53000 G5040 C017 8 Edition 07 2017 ...
Page 1614: ...1614 SIPROTEC 5 Overcurrent Protection Manual C53000 G5040 C017 8 Edition 07 2017 ...
Page 1634: ...1634 SIPROTEC 5 Overcurrent Protection Manual C53000 G5040 C017 8 Edition 07 2017 ...