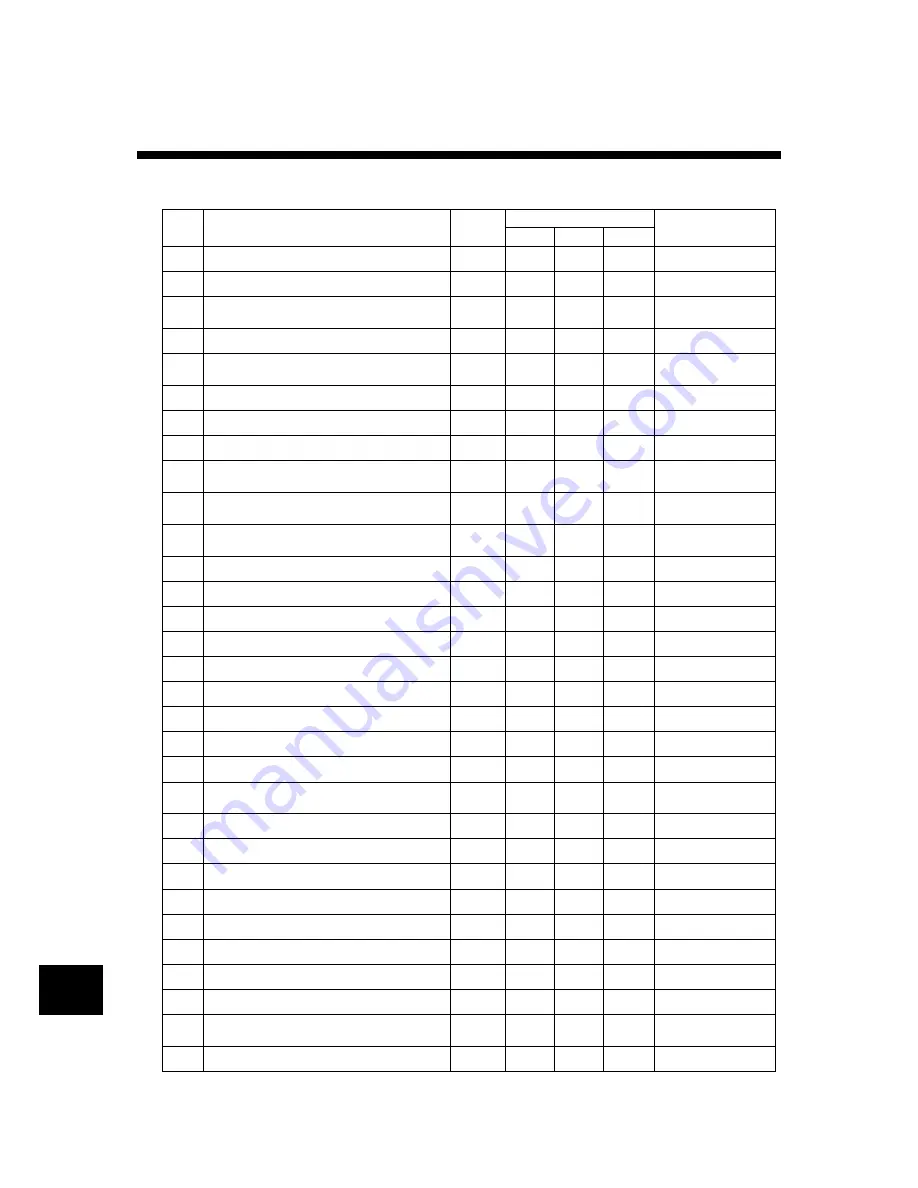
CHAPTER 15 APPENDIXES
15-6
Parameter List
15
15.4 Parameter List
PA1_: Basic setting parameters
Control mode
No. Name
Power
Position
Speed
Torque
Record of reference
value
01 Control mode selection
02 INC/ABS system selection
03 Command pulse input method and form
selection
-
-
04 Rotation direction selection
05
Number of command input pulses per
revolution
-
-
06 Numerator 0 of electronic gear
-
-
-
07 Denominator of electronic gear
-
-
-
08 Number of output pulses per revolution
09
Numerator of electric gear for output
pulses
10
Denominator of electric gear for output
pulses
11
Output pulse phase selection at CCW
rotation
12 Z-phase position offset
13 Tuning mode selection
-
-
14 Load inertia ratio
-
-
15 Auto tuning gain 1
-
-
16 Auto tuning gain 2
-
-
-
20 Easy tuning: stroke setting
-
21 Easy tuning: speed setting
-
22 Easy tuning: timer setting
-
23 Easy tuning: direction selection
-
25
Max. rotation speed (for position and
speed control)
-
-
26 Max. rotation speed (for torque control)
-
-
-
27 Forward rotation torque limit
-
28 Reverse rotation torque limit
-
29 Speed coincidence range
-
-
30 Zero speed range
-
31 Deviation unit selection
-
-
-
32 Zero deviation range/In-position range
-
-
-
33 In-position output format
-
-
34 In-position minimum OFF time/ Single shot
ON time
-
-
-
35 In-position judgment time
-
-
-
Summary of Contents for ALPHA5 Smart
Page 1: ...24C7 E 0016c FUJI SERVO SYSTEM ALPHA5 Smart USER S MANUAL...
Page 2: ......
Page 4: ...ii...
Page 36: ...CHAPTER 0 INTRODUCTION 0 16 Combination between Servomotor and Servo Amplifier 0...
Page 276: ...CHAPTER 4 PARAMETER 4 108 Output Terminal Function Setting Parameter 4...
Page 368: ...CHAPTER 6 KEYPAD 6 56 Test Operation Mode 6...
Page 392: ...CHAPTER 7 MAINTENANCE AND INSPECTION 7 24 Troubleshooting 7...
Page 472: ...CHAPTER 11 ABSOLUTE POSITION SYSTEM 11 8 Calculation of Battery Life 11...
Page 488: ...CHAPTER 12 POSITIONING DATA 12 16 Response Time 12...
Page 592: ...CHAPTER 14 PC LOADER 14 48 Parameter Conversion Tool 14 1 2 3 4 6 7 8 9 10 11...
Page 633: ...CHAPTER 15 APPENDIXES Product Warranty 15 41 15 15 9 Product Warranty...
Page 634: ...CHAPTER 15 APPENDIXES 15 42 Service Network 15 15 10 Service Network...
Page 635: ......