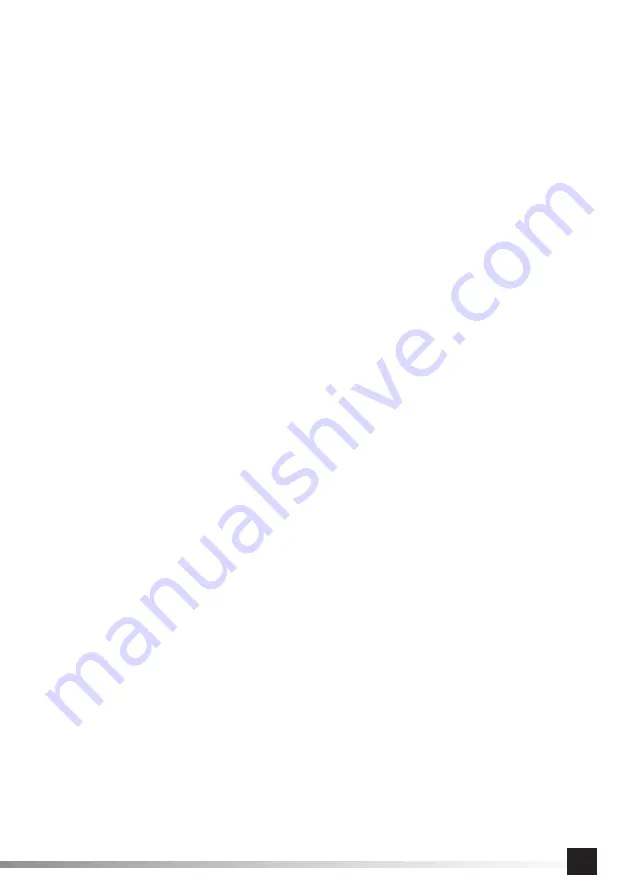
23
O R I G I N A L I N S T R U C T I O N S
EN
possible to achieve the rated output of the welder or it will not be possible to work at all. Caution! If a generator is used to power
the welder, make sure that it is earthed by means of a correctly installed system.
The connection socket must be
fi
tted with a contact and protective conductor and the mains supply must be
fi
tted with an auto-
matic protection device with a tripping current of 16 A. If the protection device is tripped too often, this may indicate that the mains
supply must be
fi
tted with a protection device with a higher tripping current.
Using long cables for connecting purposes should be avoided. If extension cables are used, they must have a capacity at least
equal to that of the welder’s power cable.
The installation of a suitable mains supply should be entrusted to a quali
fi
ed electrician. The power supply mains should be devel-
oped in accordance with EN 60204-1 or country-speci
fi
c standards.
Installation of welding cables for MMA welding with covered electrodes
Caution! Before connecting the welding cables, ensure that the power plug of the welder is disconnected from the mains socket.
Put the plug of the cable into the socket and then turn it clockwise as far as possible. Ensure that the plug cannot slide out of the
socket by itself.
Welding cables can be connected in two ways.
The spring-loaded clamp cable is connected to the “-” terminal and the electrode holder cable to the “+” terminal or vice versa.
In the
fi
rst method, most of the heat generated during the welding process is given o
ff
at the welded material and not at the elec-
trode. In the case of reverse connection, most of the heat generated during the welding process is given o
ff
at the electrode and
not at the welded material.
The choice of a connection method should be based on the technological requirements and information supplied with the elec-
trodes. Not every type of electrode may be used for welding with reverse polarity.
If an unstable arc occurs with spatters and an uneven weld during operation, reverse the polarity of the welding cables and start
welding again.
Installation of the welding cables for the lift TIG welding method (YT-81357, YT-81358)
Caution! Ensure that the device plug is disconnected from the mains socket before connecting the welding cables.
For the lift TIG lift method, using a TIG torch is recommended, equipped with a manual valve to close the shielding gas supply.
The torch must be assembled in accordance with the recommendations of the torch manufacturer. Place a properly sharpened
tungsten electrode in the welding torch. To sharpen the electrode correctly, refer to the recommendations of the manufacturer of
the electrode and the welding torch. Put the plug of the cable into the welder socket and then turn it clockwise as far as possible.
Ensure that the plug cannot not slide out of the socket by itself. Connect the current connector of the TIG torch to the “-” terminal,
and the earthing cable plug to the “+” terminal. The gas cylinder should be placed on a
fi
rm, level and stable surface and secured
against tipping over. Connect a regulator and a
fl
ow meter to the cylinder to regulate and read the
fl
ow of the shielding gas. Con-
nect the gas hose directly to the regulator located on the gas cylinder by using a quick-release coupling or a hose clamp. Tighten
the clamp with a su
ffi
cient force to achieve a tight connection and prevent the hose from being detached during operation. Do not
use excessive force that could damage the hose.
Carrying belt
CAUTION! When welding is carried out, holding the welder by the handle or having it hanging from the belt is prohibited
The welder is equipped with a belt to carry it easily. The belt should be secured to the clip at the front and the rear of the welder.
The clips are located at the top of the device housing. Do not attach the belt to the welder handle.
Operating the welder
Tips on how to carry out covered electrode welding (MMA method)
Welded surfaces should be cleared of rust, grease, oil and paint. Select an electrode suitable for the material to be welded. It is
advisable to test the electrode and the set welding current using waste material.
Hold the electrode at a distance of about 2 cm from the welding spot, and put on the welding shield. An electric arc should then
be struck using either the spark or contact method. The length of the electric arc visible through the window of the welding shield
should not be greater than 1 - 1.5 times the diameter of the electrode (II).
Maintaining the correct arc length is very important. The length is closely related to the welding voltage and current. Contamination
of the welded surfaces can adversely a
ff
ect the quality of the weld.
The electrode should be inclined at an angle of 70 to 80 degrees in relation the weld plane, in the direction of the weld bead.
Increasing the angle can cause slag to leak. Decreasing the angle can make the arc unstable, resulting in a spatter being formed
and the weld (III) becoming weaker.
It is important to maintain a constant arc length throughout the welding process. As the electrode melts during the welding process,
the electrode clamp should be gradually lowered so that the arc length remains the same.
When the electrode length decreases to about 5cm, stop welding and replace the electrode with a new one. To stop welding,
simply withdraw the electrode from the welding point. It is advisable to take away the electrode gradually by lifting it along the
Содержание YT-81355
Страница 43: ...43 RU 230 50 30...
Страница 44: ...44 RU O 16 EN 60204 1 TIG lift YT 81357 YT 81358...
Страница 45: ...45 RU TIG lift TIG TIG 2 1 1 5 II 70 80 III 5 IV TIG lift YT 81357 YT 81358 TIG 2 3 70 80 VI 6 30 VII...
Страница 54: ...54 UA 230 50 30...
Страница 55: ...55 UA 16 EN 60204 1 TIG lift YT 81357 YT 81358 TIG lift TIG...
Страница 56: ...56 UA TIG 2 1 1 5 II 70 80 III 5 IV TIG lift YT 81357 YT 81358 TIG 2 3 70 80 VI 6 30 VII 10 10...
Страница 57: ...57 UA YT 81355 HOT START ARC FORCE ANTI STICK VRD O C O C MMA I 30 140 1 6 20 50 2 40 60 2 5 60 80 3 2 80 140 O...
Страница 62: ...62 UA a 10 50 DC PULSE 2 3 O EN 60974 10 IEC 61000 3 12 0 3 toya24 pl...
Страница 168: ...168 GR 1 2 3 4 5 6 TIG 7 8 9 10 11 11 11 40 C 12 12 12 13 13 13 14 50 Hz 60 Hz 15 16 17 22 24 CE 230 V 50 Hz 30 mA...
Страница 169: ...169 GR...
Страница 170: ...170 GR O 16 A EN 60204 1 MMA TIG lift YT 81357 YT 81358 TIG lift TIG TIG...
Страница 177: ...177 GR 10 50 a DC PULSE 2 3 mm O EN 60974 10 RTV IEC 61000 3 12 0 3 MPa toya24 pl...
Страница 179: ...179 BG 1 2 3 4 5 6 TIG 7 8 9 10 11 11a 11b 40 12 12a 12b 13 13a 13b 14 50 Hz 60 Hz 15 16 17 22 24 230 V 50 Hz 30 mA...
Страница 180: ...180 BG...
Страница 181: ...181 BG O 16 A EN 60204 1 MMA TIG lift YT 81357 YT 81358 TIG lift TIG TIG...
Страница 188: ...188 BG h e a 10 50 DC PULSE j e 10 50 a DC PULSE 2 3 mm O EN 60974 10 IEC 61000 3 12 0 3 MPa toya24 pl...
Страница 211: ...211 AR TIG CE...
Страница 212: ...212 AR O EN MMA YT YT TIG lift TIG TIG lift...
Страница 213: ...213 AR TIG MMA II III IV YT YT TIG lift TIG VII VI YT HOT START ARC FORCE ANTI STICK VRD O C O C MMA MMA...
Страница 217: ...217 AR MENU DC PULSE DC PULSE DC PULSE h a e h DC PULSE e j DC PULSE O EN A IEC toya pl...
Страница 218: ...I N S T R U K C J A O R Y G I N A L N A 218...