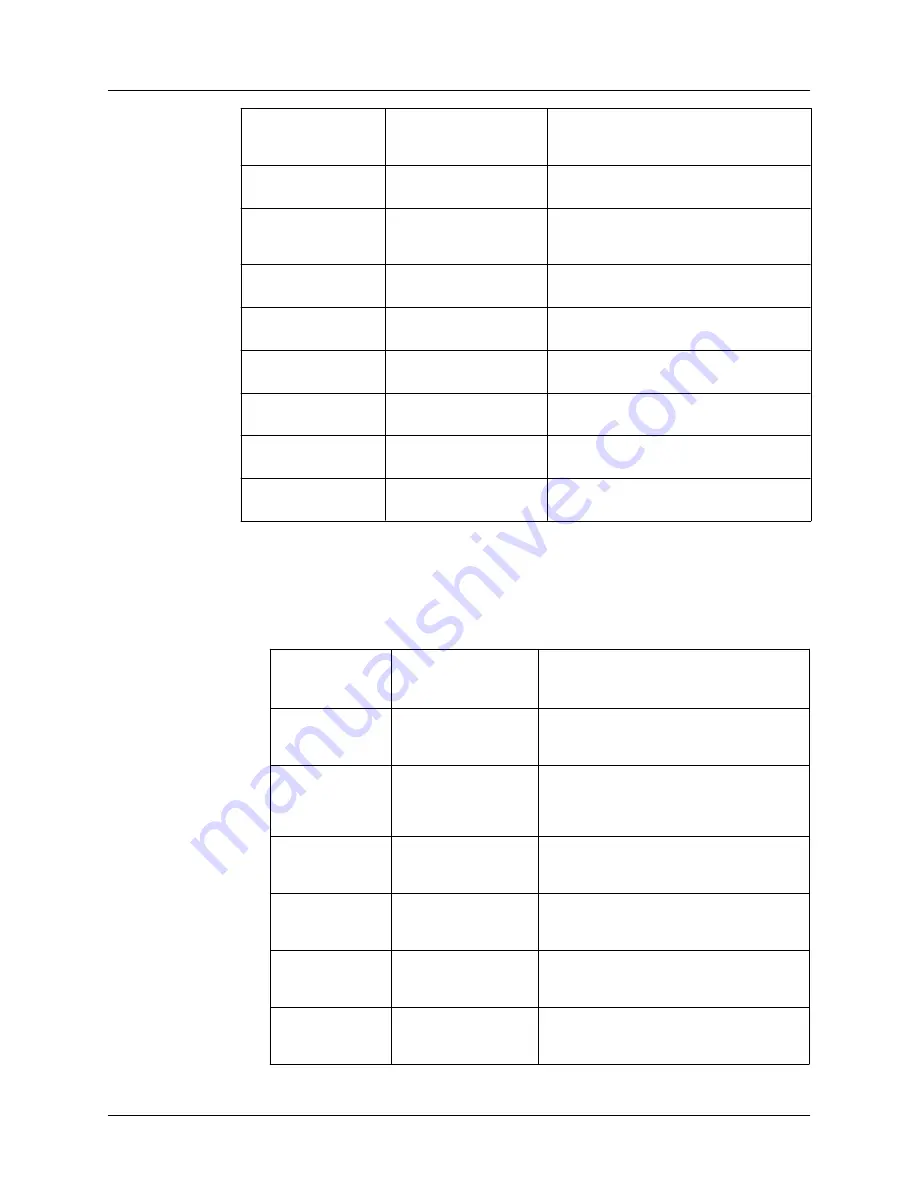
M
500 msec
Cassette advance (starts reading
bar-code)
M
10 min.
Cassette to clear chute switch
M
10 sec
Chute switch closure to reset
cassette counter
C
400 msec
Injector pump pawl lift
M
15 sec
Eject cassette time-out
M
1 min.
Close throttle valve (time-out)
M
15 sec
Door to close
M
15 sec
Door to open
M
2 min.
Printer fault
Pressure
A capacitance manometer, mounted on the top of chamber with a
connection tube oriented 30° from vertical, monitors pressure within the
chamber.
Control/
Monitor
Alarm Limits
Process Equipment Specification
M
300 mTorr
Minimum injection pressure
threshold (10 sec)
M
< mV
Injection System Interrupted
detection algorithm (2 * P60 - P56 -
P64 60 mV for good injection)
M
6 Torr
Low injection pressure alarm (6-20
min.)
M
12 Torr
Upper injection pressure alarm (
min.)
M
6 Torr
Low diffusion pressure alarm
(20-48 min.)
M
14 Torr
Upper diffusion pressure alarm (6
min.)
System Operation
Theory of Operation-Overview
2-12
STERRAD® 100 Sterilizer
ASP Service Guide rev. D
Содержание STERRAD 100
Страница 284: ......
Страница 285: ......
Страница 286: ......
Страница 287: ......
Страница 288: ......
Страница 289: ......
Страница 290: ......
Страница 291: ......
Страница 292: ......
Страница 293: ......
Страница 294: ......
Страница 295: ......
Страница 296: ......
Страница 297: ......
Страница 298: ......
Страница 299: ......
Страница 300: ......
Страница 301: ......
Страница 302: ......
Страница 303: ......
Страница 304: ......
Страница 305: ......
Страница 306: ......
Страница 307: ......
Страница 308: ......
Страница 309: ......