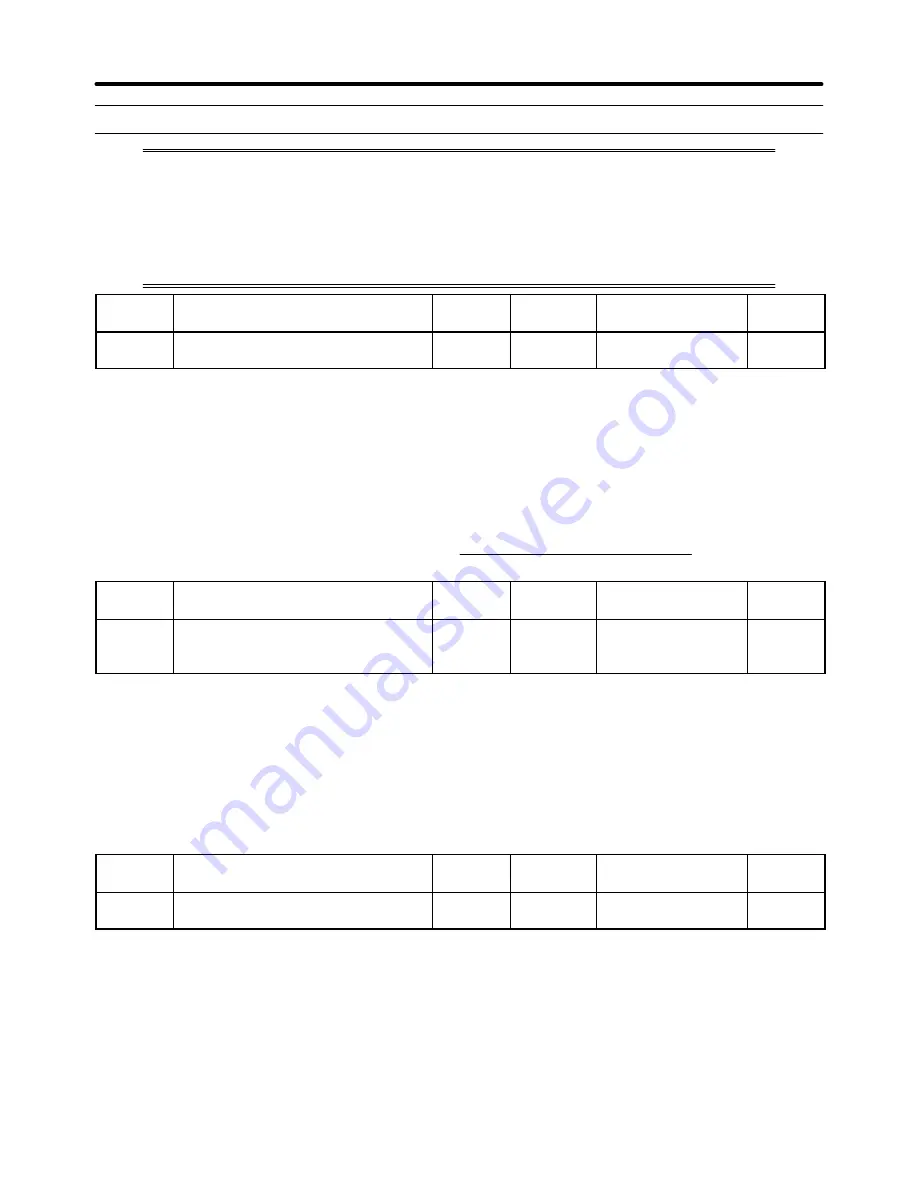
6-37
6-9
Slip Compensation Function
The slip compensation function calculates the motor torque according to the output cur-
rent, and sets gain to compensate for output frequency.
This function is used to improve speed accuracy when operating with a load. It is mainly
valid for V/f control.
Set the rated motor current (n036) and the motor no-load current (n110) before using the
slip compensation function. If n036 = 0, the slip compensation function cannot be used.
n106
Rated Motor Slip
Register
016A Hex
Changes during
operation
Yes
Setting
range
0.0 to 20.0 (Hz)
Unit of
setting
0.1 Hz
Default setting
(See
note.)
Note
The default setting varies with the capacity of the Inverter model.
Set Values
•
Set the rated slip value of the motor in use.
•
This parameter is used as a slip compensation constant.
•
Calculate the rated motor slip value from the rated frequency (Hz) and rpm on the motor nameplate by
using the following formula.
Rated slit value (Hz)
+
Rated frequency (Hz) –
Rated rpm
Number of poles
120
n111
Slip Compensation Gain
Register
016F Hex
Changes during
operation
Yes
Setting
range
0.0 to 2.5
Unit of
setting
0.1
Default setting
0.0
(See
note 1.)
Note 1.
If set to vector control mode, the default value will be 1.0.
Note 2.
This parameter is disabled with the value set to 0.0.
Set Values
•
Set the parameter to 1.0 first and check the operation of the Inverter. Then fine-tune the gain with
0.1-gain increments or decrements.
If the speed is lower than the target value, increase the set value.
If the speed is higher than the target value, decrease the set value.
n112
Slip Compensation Primary Delay
Time
Register
0170 Hex
Changes during
operation
No
Setting
range
0.0 to 25.5 (s)
Unit of
setting
0.1 s
Default setting
2.0 (See
note.)
Note
If set to vector control mode, the default value will be 0.2.
Set Values
•
This parameter is used for the response adjustment of the slip compensation function.
•
The default setting does not need any changes in normal operation.
•
Change the default setting in the following cases.
The motor vibrates:
Set the value to a larger value.
The motor response is low:
Set the value to a smaller value.
Advanced Operation
Chapter 6
Summary of Contents for SYSDRIVE 3G3MV-A2001
Page 1: ...Cat No I527 E1 04 USER S MANUAL SYSDRIVE 3G3MV Multi function Compact Inverter...
Page 2: ......
Page 3: ...USER S MANUAL Multi function Compact Inverter SYSDRIVE 3G3MVSERIES...
Page 18: ......
Page 23: ...Chapter 1 Overview 1 1 Functions 1 2 Nomenclature 1 3 New Features 1...
Page 32: ......
Page 33: ...Chapter 2 Design 2 1 Installation 2 2 Wiring 2...
Page 74: ......
Page 93: ...Chapter 4 Test Run 4 1 Procedure for Test Run 4 2 Operation Example 4...
Page 102: ......
Page 142: ......
Page 242: ......
Page 268: ......
Page 269: ...Chapter 9 Specifications 9 1 Inverter Specifications 9 2 Option Specifications 9...
Page 303: ...Chapter 10 List of Parameters 10...
Page 337: ...Chapter 11 Using the Inverter for a Motor 11...
Page 343: ......
Page 344: ...I527 E1 04...