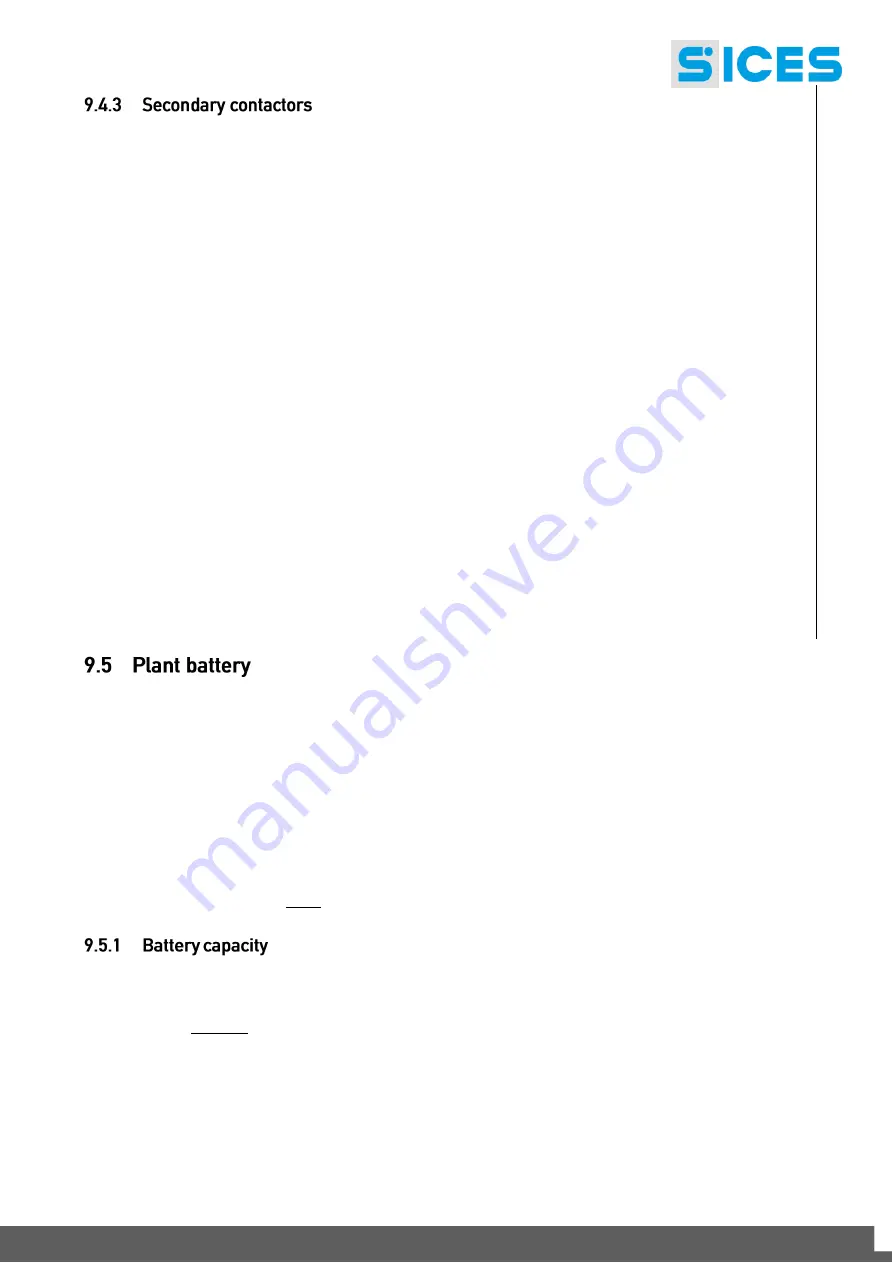
Technical Handbook 133
Starting from version 1.09, HS315 manages up to 8 secondary contactors, which can be used
to connect different groups of loads to the storage battery (or to the generator).
Note
: if an LCB circuit breaker exists (see 9.8), it must be placed upstream of the secondary
contactors: if it opens, the loads connected to any secondary contactor must result unsupplied.
For these contactors, HS315 only manages the stable closing/opening command: the
functions from DOF.2261 to DOF.2268 are defined for the configuration of the digital outputs.
It is not mandatory to use all the functions: it is possible to manage from a minimum of 2 to a
maximum of 8 contactors. If less than 8 contactors are used, it is recommended to use the
contiguous functions starting from DOF.2261 (without leaving holes). This allows for
optimizations of the display.
There is no management, instead, of any feedback of the contactors (and consequently not
even of the failure to open/close alarms).
The management logic is the same in all the operating modes of the controller (MAN and
AUTO).
•
The contactors are automatically opened (all simultaneously) if the loads are
unsupplied (if LCB is open or, in any case, if there is no voltage upstream of LCB).
•
When there voltage upstream of LCB and LCB is closed, the controller closes all the
configured contactors, one at a time, with a delay between one and the other
configurable with parameter P.9772.
Once the closing sequence is finished, the operator can manually control the contactors.
Parameter P.9771 allows to indicate which contactors must remain closed and which must be
open. This parameter can also be modified directly from page M.09.
Warning
: if you select to
open a contactor by this parameter, it will no longer be considered in the automatic closing
sequence.
The plant battery is the main part of a hybrid system. It supplies the loads. Generator and/or
auxiliary source are used only to recharge the battery. The whole system must be designed to
optimize the use of the generator, to use it as less as possible; when used, it should work in
the power range with maximum efficiency (therefore, it should be selected based on the battery
charging current). At design time, it must be considered that, during the charge procedure, the
generator supplies the loads too.
The controller acquires both voltage and current (DC) of the battery. As a rule, the current
must be positive when supplied by the battery (discharge), negative if absorbed by the battery
(charge). The connection point of the v
oltage must be “before” the BCB circuit breaker (if
present).
The controller
must
acquire both voltage and current of the battery; if not, it activates the alarm
(block) A273 (those two measurements are required for the charge/discharge processes).
The battery manufacturer specifies its rated capacity (Ah).
The real battery capacity, however, changes based on the discharge current: the rated value,
normally, must be considered correct when the battery is discharged in 20 hours (thus with a
current equal to 1/20 of the rated capacity). If the discharge current is higher, the battery
capacity decreases; if the discharge current is lower, the battery capacity increases.
The relation between the discharge current and the capacity is defined by a constant (Peukert
constant). The battery manufacturer should specify this constant, or, alternatively, it can
specify two real capacities at two given discharge currents.
Configuration of HS315, when the battery manufacturer states the Peukert constant:
Содержание HS 315
Страница 1: ...File name EAAM058607EN docx Rev 07 Date 25 09 2019 ID Document EAAM0586 Product HS315...
Страница 17: ...Technical Handbook xvii...
Страница 18: ......
Страница 23: ...Technical Handbook 5 Rear view Hall...
Страница 254: ......