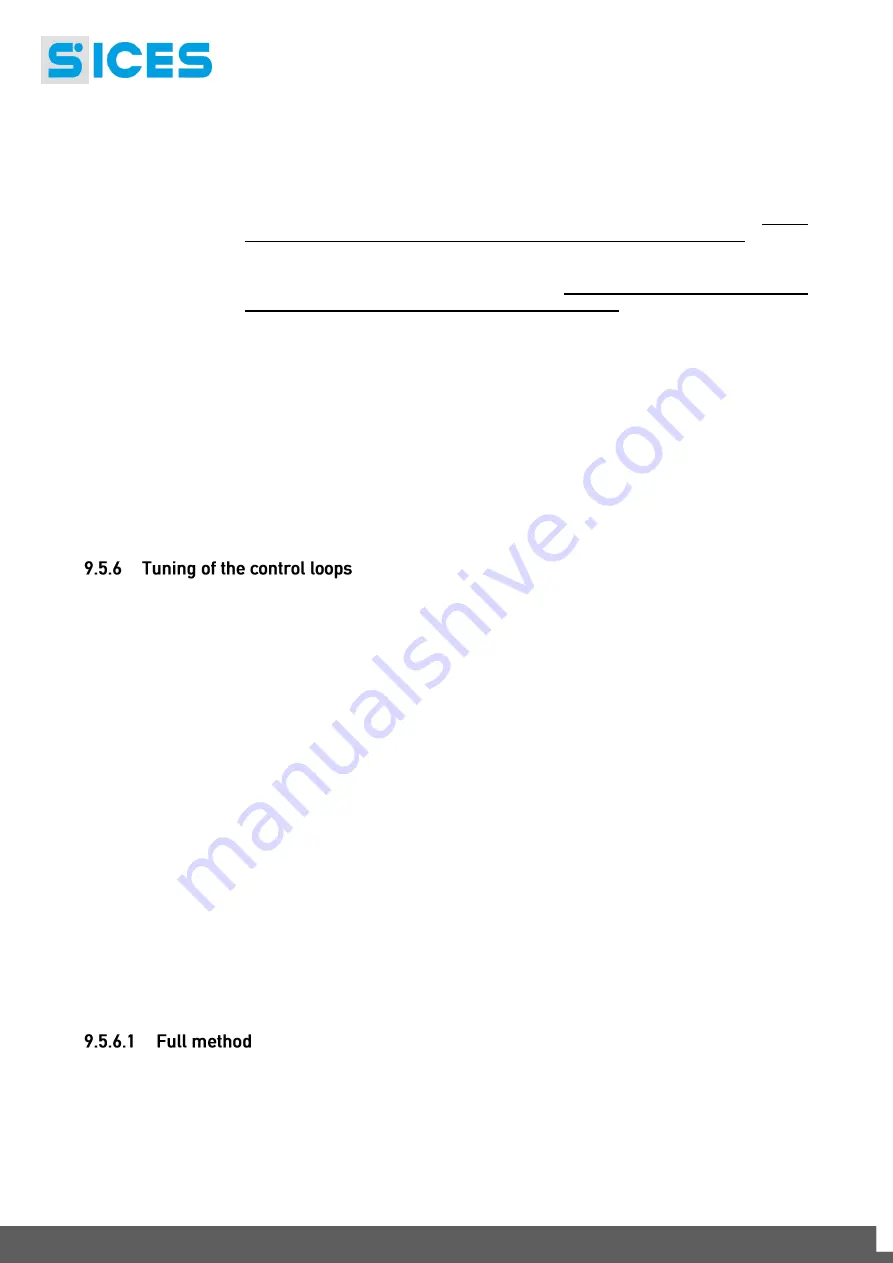
136
Technical Handbook
3. Both.
Based on charge requests and on parameter P.9661, HS315 starts the generator to recharge
the battery. The real start is activated only if the pending requests persist for at least the time
configured by P.9666
(“Delay before starting the genset”). When the charge cycle is in
progress, its end is determined in the following ways:
•
If the charg
e cycle has been requested for “low remaining charge” and not for
minimum voltage, and if P.9681 or P.9688 (see 9.5.7) is different from 1.00, then the
cycle will end when the remaining charge level will become greater than the value set
by P.9681
(“Charge (full) limit”) or P.9688 (“Charge (standard) limit”) (see 9.5.7),
defined as a percentage of the rated capacity.
In this case, the estimation of the
remaining charge is not forced to the rated capacity.
•
In all other situations, the cycle will end after the three charge phases (BULK,
ABSORBTION and FLOAT). At the end of the cycle, the estimation of the remaining
charge is forced to the rated capacity.
The controller records the requests for starting/stopping the charge process in the events log,
if it is enabled with bit 8 of the P.0441 parameter:
•
EVT.1511: charge started for minimum voltage.
•
EVT.1512: charge stopped because the final charge voltage has been reached.
•
EVT.1513:
charge started for minimum charge level.
•
EVT.1514:
charge stopped because the required charge level has been reached.
The controller internally uses several PI regulators, to determine the voltage and speed
references needed in every instant to manage the generator during charge process. All internal
PI regulators are configured with two parameters:
•
The factor proportional to current error (P), also called "gain".
•
The factor related to the integral in error time (I), also called "integrative factor".
In the following chapters the parameters associated with each PI regulator will be indicated.
These two parameters for each PI regulator should be "calibrated" on the field during the
commissioning of the generator. In fact, they depend on several factors: type of engine,
alternator power, type of alternator; different parameters for similar systems may also be
required.
However, setting these parameters is not very critical if carried out following a correct
procedure. Unfortunately, the empirical setting-up method (called Ziegler-Nichols) requires
measuring the period of oscillation of controlled condition (current, voltage), measurement that
is not always possible (or easier) to perform.
For this reason, beside the empirical method, we suggest a simplified one that should allow to
properly select the relevant parameters.
PI controllers’ parameters can also be modified while the system is running, even from the
operator panel. It is advisable to make changes using the BoardPrg3 program, available free
of charge on SICES s.r.l. website.
1) Set "P" at an initial value (0.100) and "I" at 0000.
2) Increase "P" until the controlled condition starts to oscillate (for example, if you are
adjusting the IP that manages the battery voltage, increase "P" until the voltage continually
increases/decreases). Decrease/increase the value of "P" until the starting point of the
oscillation is singled out (a good approximation is enough).
Содержание HS 315
Страница 1: ...File name EAAM058607EN docx Rev 07 Date 25 09 2019 ID Document EAAM0586 Product HS315...
Страница 17: ...Technical Handbook xvii...
Страница 18: ......
Страница 23: ...Technical Handbook 5 Rear view Hall...
Страница 254: ......