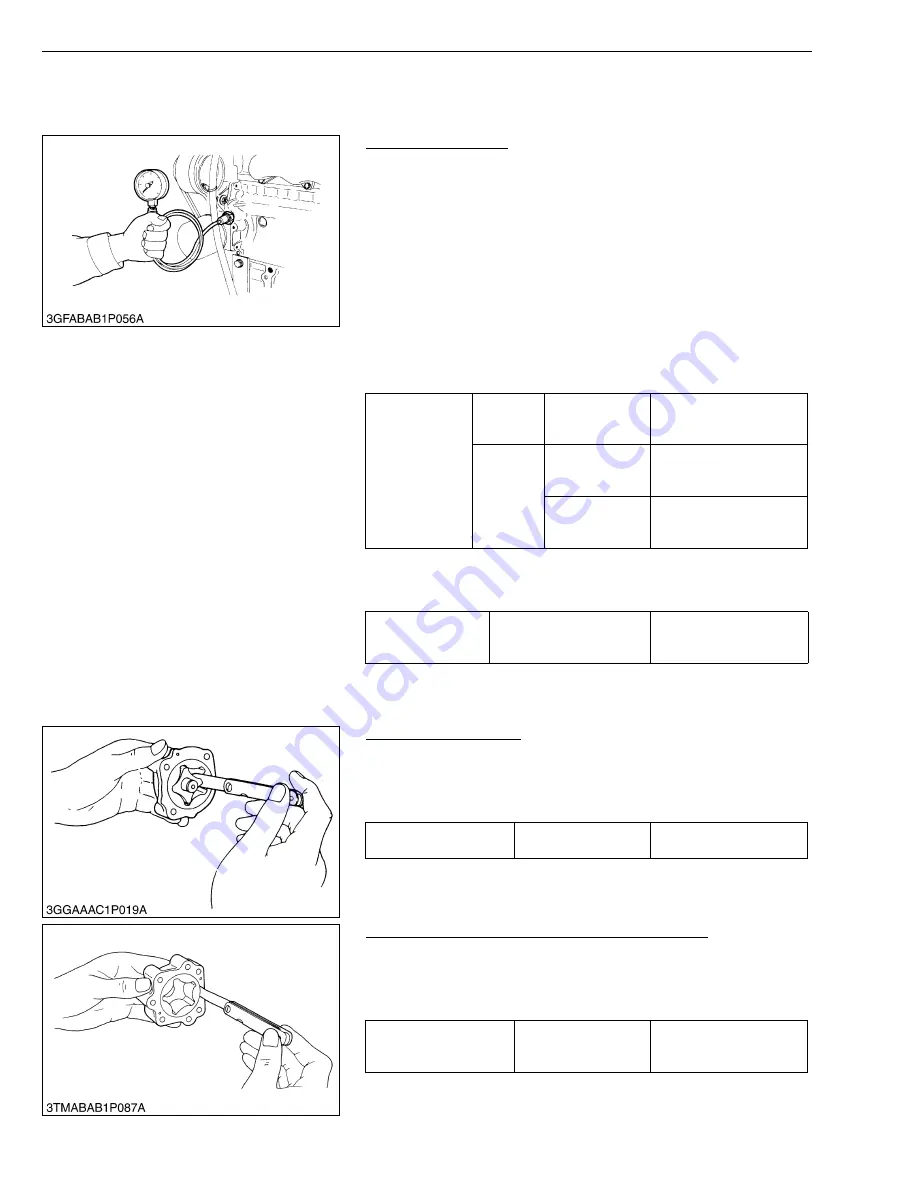
1-S46
G2160, WSM
ENGINE
[3] LUBRICATING SYSTEM
(1) Checking
Engine Oil Pressure
1. Remove the engine oil pressure switch, and set a oil pressure
tester (Code No. 07916-32032). (Adapter screw size : PT 1/8)
2. Start the engine. After warming up, measure the oil pressure of
both idling and rated speeds.
3. If the oil pressure is less than the allowable limit, check the
following.
• Engine oil insufficient
• Oil pump defective
• Oil strainer clogged
• Oil filter cartridge clogged
• Oil gallery clogged
• Excessive oil clearance
• Foreign matter in the relief valve
(When reassembling)
• After checking the engine oil pressure, tighten the engine oil
pressure switch to the specified torque.
W10373890
(2) Servicing
Rotor Lobe Clearance
1. Measure the clearance between lobes of the inner rotor and the
outer rotor with a feeler gauge.
2. If the clearance exceeds the factory specifications, replace the oil
pump rotor assembly.
W10378950
Clearance between Outer Rotor and Pump Body
1. Measure the clearance between the outer rotor and the pump
body with a feeler gauge.
2. If the clearance exceeds the factory specifications, replace the oil
pump rotor assembly.
W10381420
Engine oil
pressure
At idle
speed
Factory spec.
More then 68 kPa
0.7 kgf/cm
2
10.0psi
At rated
speed
Factory spec.
196 to 441 kPa
2.0 to 4.5 kgf/cm
2
28 to 64 psi
Allowable limit
98 kPa
1.0 kgf/cm
2
14 psi
Tightening torque
Oil switch
14.7 to 19.6 N·m
1.5 to 2.0 kgf·m
10.8 to 14.5 ft-lbs
Rotor lobe clearance
Factory spec.
0.03 to 0.14 mm
0.0012 to 0.0055 in.
Clearance between
outer rotor and pump
body
Factory spec.
0.07 to 0.15 mm
0.0028 to 0.0059 in.
KiSC issued 11, 2006 A
Содержание G2160
Страница 1: ...WORKSHOP MANUAL G2160 G2160 R48S G2460G TRACTOR KiSC issued 11 2006 A...
Страница 7: ...5 G2160 WSM SAFETY INSTRUCTIONS KiSC issued 11 2006 A...
Страница 8: ...6 G2160 WSM SAFETY INSTRUCTIONS KiSC issued 11 2006 A...
Страница 9: ...7 G2160 WSM SAFETY INSTRUCTIONS KiSC issued 11 2006 A...
Страница 12: ...10 G2160 WSM DIMENSIONS DIMENSIONS KiSC issued 11 2006 A...
Страница 13: ...G GENERAL KiSC issued 11 2006 A...
Страница 59: ...1 ENGINE KiSC issued 11 2006 A...
Страница 115: ...2 TRANSMISSION AND REAR AXLE KiSC issued 11 2006 A...
Страница 123: ...2 S1 G2160 WSM TRANSMISSION AND REAR AXLE 1 TROUBLESHOOTING 1 HYDROSTATIC TRANSMISSION KiSC issued 11 2006 A...
Страница 124: ...2 S2 G2160 WSM TRANSMISSION AND REAR AXLE KiSC issued 11 2006 A...
Страница 125: ...2 S3 G2160 WSM TRANSMISSION AND REAR AXLE 2 TRANSMISSION KiSC issued 11 2006 A...
Страница 148: ...3 BRAKE KiSC issued 11 2006 A...
Страница 157: ...4 FRONT AXLE KiSC issued 11 2006 A...
Страница 164: ...5 STEERING KiSC issued 11 2006 A...
Страница 174: ...5 S2 G2160 WSM STEERING 2 TROUBLESHOOTING 1 TROUBLESHOOTING BASED ON EACH SYMPTOM KiSC issued 11 2006 A...
Страница 175: ...5 S3 G2160 WSM STEERING KiSC issued 11 2006 A...
Страница 176: ...5 S4 G2160 WSM STEERING KiSC issued 11 2006 A...
Страница 177: ...5 S5 G2160 WSM STEERING KiSC issued 11 2006 A...
Страница 179: ...5 S7 G2160 WSM STEERING 2 Error code 03 3 Error code 05 KiSC issued 11 2006 A...
Страница 180: ...5 S8 G2160 WSM STEERING 4 Error code 06 5 Error code 11 KiSC issued 11 2006 A...
Страница 181: ...5 S9 G2160 WSM STEERING 6 Error code 12 and 13 7 Error code 15 KiSC issued 11 2006 A...
Страница 182: ...5 S10 G2160 WSM STEERING 8 Error code 17 9 Error code 19 and 22 KiSC issued 11 2006 A...
Страница 183: ...5 S11 G2160 WSM STEERING 10 Error code 23 KiSC issued 11 2006 A...
Страница 184: ...5 S12 G2160 WSM STEERING 11 Error code 32 12 Error code 34 KiSC issued 11 2006 A...
Страница 185: ...5 S13 G2160 WSM STEERING 13 Error code 35 KiSC issued 11 2006 A...
Страница 205: ...6 HYDRAULIC SYSTEM KiSC issued 11 2006 A...
Страница 220: ...7 PTO SYSTEM KiSC issued 11 2006 A...
Страница 222: ...7 S1 G2160 WSM PTO SYSTEM 1 TROUBLESHOOTING KiSC issued 11 2006 A...
Страница 228: ...8 ELECTRICAL SYSTEM KiSC issued 11 2006 A...
Страница 230: ...8 M1 G2160 WSM ELECTRICAL SYSTEM 1 WIRING DIAGRAM 1 WIRING DIAGRAM with KRA system KiSC issued 11 2006 A...
Страница 231: ...8 M2 G2160 WSM ELECTRICAL SYSTEM KiSC issued 11 2006 A...
Страница 232: ...8 M3 G2160 WSM ELECTRICAL SYSTEM 2 WIRING DIAGRAM without KRA system KiSC issued 11 2006 A...
Страница 233: ...8 M4 G2160 WSM ELECTRICAL SYSTEM KiSC issued 11 2006 A...
Страница 241: ...8 S1 G2160 WSM ELECTRICAL SYSTEM 1 TROUBLESHOOTING KiSC issued 11 2006 A...
Страница 242: ...8 S2 G2160 WSM ELECTRICAL SYSTEM KiSC issued 11 2006 A...
Страница 243: ...8 S3 G2160 WSM ELECTRICAL SYSTEM KiSC issued 11 2006 A...
Страница 244: ...8 S4 G2160 WSM ELECTRICAL SYSTEM KiSC issued 11 2006 A...
Страница 245: ...8 S5 G2160 WSM ELECTRICAL SYSTEM KiSC issued 11 2006 A...
Страница 246: ...8 S6 G2160 WSM ELECTRICAL SYSTEM KiSC issued 11 2006 A...
Страница 247: ...8 S7 G2160 WSM ELECTRICAL SYSTEM KiSC issued 11 2006 A...
Страница 248: ...8 S8 G2160 WSM ELECTRICAL SYSTEM KiSC issued 11 2006 A...
Страница 272: ...9 MOWER KiSC issued 11 2006 A...
Страница 274: ...9 S1 G2160 WSM MOWER 1 TROUBLESHOOTING KiSC issued 11 2006 A...
Страница 289: ...P G2460G Supplement Printed in Japan 2001 02 S EI EI e 97897 15041 KiSC issued 11 2006 A...
Страница 296: ...P 5 G2460G WSM SAFETY INSTRUCTIONS KiSC issued 11 2006 A...
Страница 342: ...P8 M1 G2460G WSM ELECTRICAL SYSTEM 1 WIRING DIAGRAM AND ELECTRICAL CIRCUIT 1 WIRING DIAGRAM KiSC issued 11 2006 A...
Страница 343: ...P8 M2 G2460G WSM ELECTRICAL SYSTEM KiSC issued 11 2006 A...
Страница 344: ...P8 M3 G2460G WSM ELECTRICAL SYSTEM 2 ELECTRICAL CIRCUIT KiSC issued 11 2006 A...
Страница 345: ...P8 M4 G2460G WSM ELECTRICAL SYSTEM KiSC issued 11 2006 A...
Страница 353: ...Q3 G2160 R48S WSM SAFETY INSTRUCTIONS KiSC issued 11 2006 A...
Страница 354: ...Q4 G2160 R48S WSM SAFETY INSTRUCTIONS KiSC issued 11 2006 A...
Страница 355: ...Q5 G2160 R48S WSM SAFETY INSTRUCTIONS KiSC issued 11 2006 A...
Страница 358: ...Q8 G2160 R48S WSM DIMENSIONS DIMENSIONS KiSC issued 11 2006 A...
Страница 377: ...Q6 S2 G2160 R48S WSM HYDRAULIC SYSTEM 2 SERVICING 1 Troubleshooting KiSC issued 11 2006 A...
Страница 383: ...Q8 M1 G2160 R48S WSM ELECTRICAL SYSTEM 8 ELECTRICAL SYSTEM 1 MECHANISM 1 Wiring Diagram KiSC issued 11 2006 A...
Страница 384: ...Q8 M2 G2160 R48S WSM ELECTRICAL SYSTEM KiSC issued 11 2006 A...