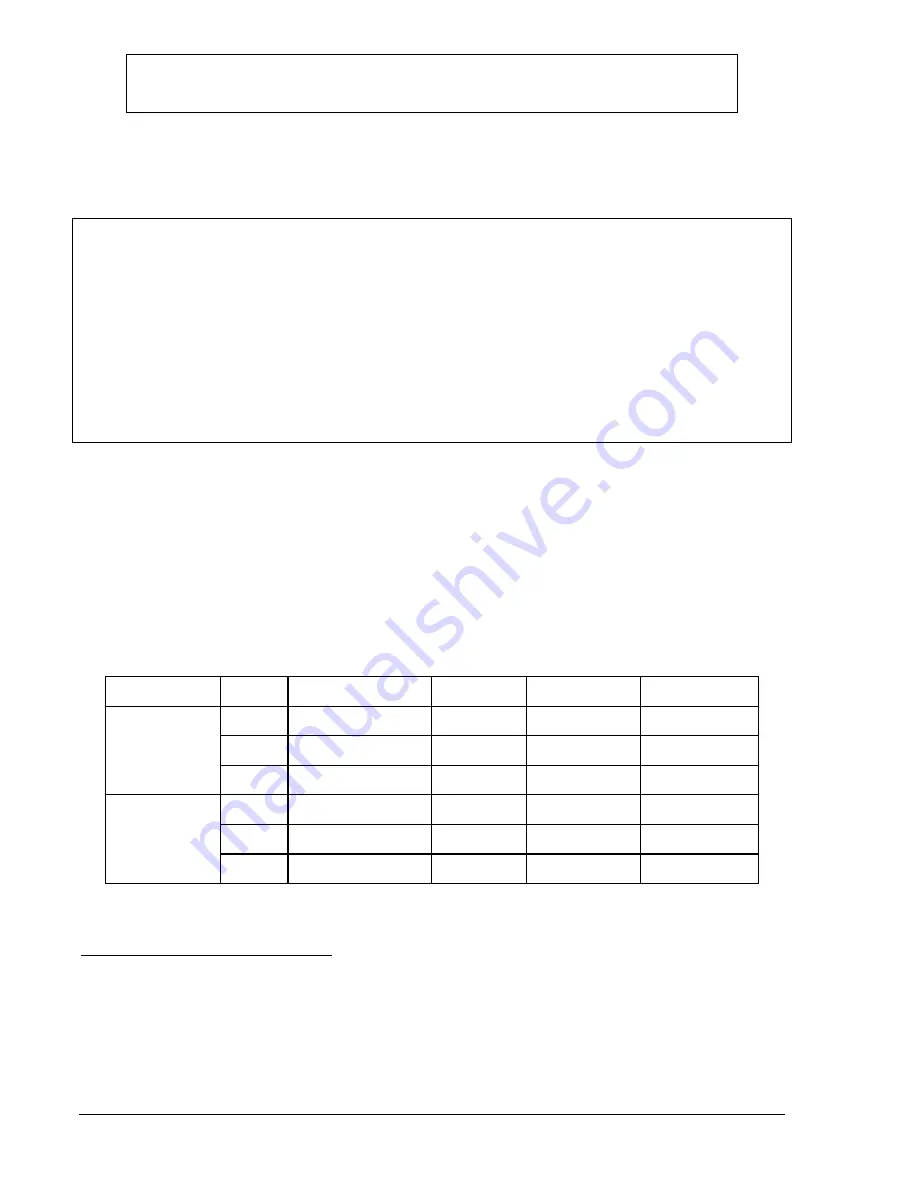
13-48
Testing And Maintenance
BE1-CDS220
NOTE
With the relay in service, it is necessary to view the 87ND tap factors by accessing the
HMI screen \PROT\SGn\87ND\87ND.
Step 3.
The relay auto tap compensation logic will calculate TAPN and TAPG values based on the CT
ratios for the designated phase CTs and the ground CT. Since CTR2 and CTRG are both
equal to 1:1 for this test, the TAPN and TAPG values are both equal to the minimum settings
for either 5 ampere or 1 ampere relays (2.0 and 0.4 respectively). For more information on auto
tap compensation, see Sidebar 13-9.
Sidebar 13-9. Auto Tap Compensation
Tap adjustment factors for the 87ND function are automatically calculated based on the equation:
TAPN * CTRn = TAPG * CTRG
where CTRn is the CT ratio for the CT designated in the SL-87ND setting in the active logic. Currents are
tap adjusted based on the CT ratios with the driving tap (CT input with the highest CTR) set at the
minimum setting (2.0 for 5 ampere sensing relays and 0.4 for 1 ampere sensing relays) and the other tap
adjusted to the driving tap based on the equation above. For more information on Auto Tap
Compensation, refer to Section 4,
Protection and Control Functions, Differential Protection, 87ND Neutral
Differential Function.
Step 4.
Apply current to the ground input and slowly ramp up until OUT1 closes.
Step 5.
Accuracy when increasing or decreasing the input current is
±
4% of setting or 75 milliamperes
(whichever is larger) for 5 ampere sensing inputs and
±
4% of setting or 25 milliamperes
(whichever is larger) for 1 ampere sensing inputs. Verify that pickup occurred within the
specified accuracy of the relay.
Step 6.
Decrease the current to the ground input until the relay drops out.
Step 7.
Repeat for all other values shown in Table 13-36 by substituting for minpu in the S#-87ND
command or if supplied with the HMI option, by navigating to screen \PROT\SGn\87ND\87ND
and editing the MIN PICKUP value.
Table 13-36. Minimum Pickup Accuracy Limits (87ND)
Sensing Type MINPU Calculated TAPG
Pickup (A)
Low Limit (A)
High Limit (A)
5 A
0.10
2.00
0.20
0.125
0.275
0.50
2.00 1.00
0.925
1.075
1.00
2.00 2.00
1.920
2.080
1 A
0.10
0.40
0.04
0.015
0.065
0.50
0.40 0.20
0.175
0.225
1.00
0.40 0.40
0.375
0.425
Step 8.
(Optional) Repeat Steps 2 through 8 for setting groups 1 through 3, using the CS/CO-GROUP
command to change setting groups.
Restrained Pickup Verification (87ND)
Purpose:
To verify the accuracy of the restraint operation of the 87ND element.
Reference Commands:
SL-87ND, SL- VO, SG-CT, S(n)-87, S(n)-TAP87
Step 1.
Connect one current source to terminals B9 and B10 (A-phase input 2) and a second source at
180
o
to terminals B7 and B8 (ground input). See Figure 13-16. An ohm-meter or continuity
tester may be used to monitor output contact status.
Содержание BE1-CDS220
Страница 2: ......
Страница 10: ...viii Introduction BE1 CDS220 This page intentionally left blank...
Страница 36: ...ii Quick Start BE1 CDS220 This page intentionally left blank...
Страница 48: ...ii Input And Output Functions BE1 CDS220 This page intentionally left blank...
Страница 66: ...iv Protection and Control BE1 CDS220 This page intentionally left blank...
Страница 112: ...ii Metering BE1 CDS220 This page intentionally left blank...
Страница 116: ...5 4 Metering BE1 CDS220 This page intentionally left blank...
Страница 166: ...ii BESTlogic Programmable Logic BE1 CDS220 This page intentionally left blank...
Страница 176: ...7 10 BESTlogic Programmable Logic BE1 CDS220 This page intentionally left blank...
Страница 234: ...8 56 Application BE1 CDS220 This page intentionally left blank...
Страница 236: ...ii Security BE1 CDS220 This page intentionally left blank...
Страница 240: ...9 4 Security BE1 CDS220 This page intentionally left blank...
Страница 242: ...ii Human Machine Interface BE1 CDS220 This page intentionally left blank...
Страница 256: ...10 14 Human Machine Interface BE1 CDS220 This page intentionally left blank...
Страница 258: ...ii ASCII Command Interface BE1 CDS220 This page intentionally left blank...
Страница 289: ...BE1 CDS220 Installation 12 7 Figure 12 8 MX Case Horizontal Panel Mount Front View Overall Dimensions...
Страница 422: ...14 32 BESTCOMS Software BE1 CDS220 This page intentionally left blank...
Страница 424: ...ii Time Current Characteristics BE1 CDS220 This page intentionally left blank...
Страница 441: ...BE1 CDS220 Time Overcurrent Characteristic Curves A 17 Figure A 13 Time Characteristic Curve A Standard Inverse 99 1621...
Страница 442: ...A 18 Time Overcurrent Characteristic Curves BE1 CDS220 Figure A 14 Time Characteristic Curve B Very Inverse 99 1376...
Страница 443: ...BE1 CDS220 Time Overcurrent Characteristic Curves A 19 Figure A 15 Time Characteristic Curve C Extremely Inverse 99 1377...
Страница 444: ...A 20 Time Overcurrent Characteristic Curves BE1 CDS220 Figure A 16 Time Characteristic Curve G Long Time Inverse 99 1622...
Страница 452: ...ii Terminal Communication BE1 CDS220 This page intentionally left blank...
Страница 456: ...C 4 Terminal Communication BE1 CDS220 This page intentionally left blank...
Страница 458: ...ii Settings Calculations BE1 CDS220 This page intentionally left blank...
Страница 475: ......