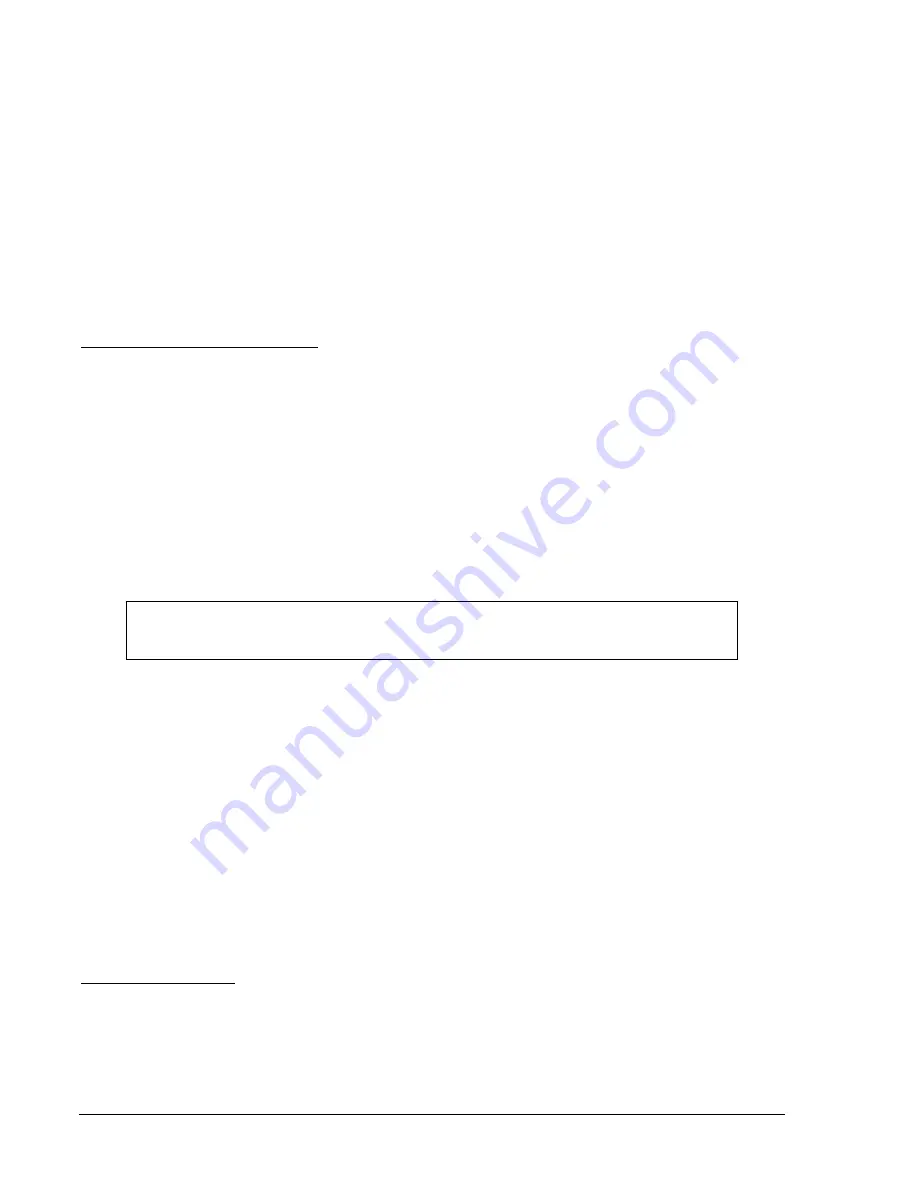
13-18
Testing And Maintenance
BE1-CDS220
Step 5-1. Use the starting current calculated in Step 4 and the appropriate equation under the column
heading Trip If Slope in Figure 13-3 to calculate the test point for each setting group and record
that point before starting the test.
Step 5-2. Record the phases that are expected to respond.
Step 6.
Test the slope for each setting group.
Step 6-1. Slowly ramp the test current on CT input circuit 1 in desired direction until the relay trips.
Step 6-2. Monitor an appropriate contact per the logic settings and the trip LED, and record the trip
values for each setting group.
Step 6-3. Record whether the proper phases targeted and if the test was passed. The accuracy should
be
±
4% of the setting or 0.75 milliamperes, whichever is greater, for 5 ampere units and
±
4%
or 25 milliamperes, whichever is greater, for 1 ampere units.
Phase Differential Unrestrained Trip
The following test is similar to the restrained minimum pickup test. For this test, you will apply a single
phase test current to one CT input circuit at a time. It is only necessary to apply one phase per input to
verify response and settings correctly entered. For example, apply phase A for CT circuit 1 and 2 for
group 0, phase B for CT circuit 1 and 2 for group 1, etc. to verify all phases and all set points.
Step 7.
Calculate test points for the unrestrained test.
Step 7-1. Calculate the test points using the compensation settings recorded in Step 1 and the
appropriate equations shown in Tables 13-8 through 13-10. In this case, substitute the
unrestrained pickup setting for the restrained minimum pickup setting in the equations. Record
the calculated test point for each setting group before running the test.
Step 7-2. Record the phases that will respond to the test.
NOTE
Depending upon your relay settings, it may be necessary to disable the restrained
differential element to test the unrestrained differential element.
Step 8.
Begin the unrestrained pickup test.
Step 8-1. Slowly ramp up the test current until the relay trips.
Step 8-2. Monitor an appropriate contact per the logic settings and the trip LED, and record the value.
Step 8-3. Record whether the proper phases targeted and if the test was passed. The accuracy should
be
±
3% of the setting or 0.75 milliamperes, whichever is greater, for 5 ampere units and
±
3%
of the setting or 25 milliamperes, whichever is greater, for 1 ampere units.
Verify Other Set Points as Appropriate
Consult Functional Testing in this Section of the manual for guidelines on how to test other functions to
verify set points of other protection and control functions.
Digital I/O Connection Verification
Contact Sensing Inputs
Purpose: To verify contact sensing input settings and connections
Reference Commands: SN-IN, SG-IN
Step 1.
Verify contact sensing input settings.
•
Transmit the SN-IN1 command to verify the input 1 user-defined name, TRUE label, and FALSE
label.
Содержание BE1-CDS220
Страница 2: ......
Страница 10: ...viii Introduction BE1 CDS220 This page intentionally left blank...
Страница 36: ...ii Quick Start BE1 CDS220 This page intentionally left blank...
Страница 48: ...ii Input And Output Functions BE1 CDS220 This page intentionally left blank...
Страница 66: ...iv Protection and Control BE1 CDS220 This page intentionally left blank...
Страница 112: ...ii Metering BE1 CDS220 This page intentionally left blank...
Страница 116: ...5 4 Metering BE1 CDS220 This page intentionally left blank...
Страница 166: ...ii BESTlogic Programmable Logic BE1 CDS220 This page intentionally left blank...
Страница 176: ...7 10 BESTlogic Programmable Logic BE1 CDS220 This page intentionally left blank...
Страница 234: ...8 56 Application BE1 CDS220 This page intentionally left blank...
Страница 236: ...ii Security BE1 CDS220 This page intentionally left blank...
Страница 240: ...9 4 Security BE1 CDS220 This page intentionally left blank...
Страница 242: ...ii Human Machine Interface BE1 CDS220 This page intentionally left blank...
Страница 256: ...10 14 Human Machine Interface BE1 CDS220 This page intentionally left blank...
Страница 258: ...ii ASCII Command Interface BE1 CDS220 This page intentionally left blank...
Страница 289: ...BE1 CDS220 Installation 12 7 Figure 12 8 MX Case Horizontal Panel Mount Front View Overall Dimensions...
Страница 422: ...14 32 BESTCOMS Software BE1 CDS220 This page intentionally left blank...
Страница 424: ...ii Time Current Characteristics BE1 CDS220 This page intentionally left blank...
Страница 441: ...BE1 CDS220 Time Overcurrent Characteristic Curves A 17 Figure A 13 Time Characteristic Curve A Standard Inverse 99 1621...
Страница 442: ...A 18 Time Overcurrent Characteristic Curves BE1 CDS220 Figure A 14 Time Characteristic Curve B Very Inverse 99 1376...
Страница 443: ...BE1 CDS220 Time Overcurrent Characteristic Curves A 19 Figure A 15 Time Characteristic Curve C Extremely Inverse 99 1377...
Страница 444: ...A 20 Time Overcurrent Characteristic Curves BE1 CDS220 Figure A 16 Time Characteristic Curve G Long Time Inverse 99 1622...
Страница 452: ...ii Terminal Communication BE1 CDS220 This page intentionally left blank...
Страница 456: ...C 4 Terminal Communication BE1 CDS220 This page intentionally left blank...
Страница 458: ...ii Settings Calculations BE1 CDS220 This page intentionally left blank...
Страница 475: ......