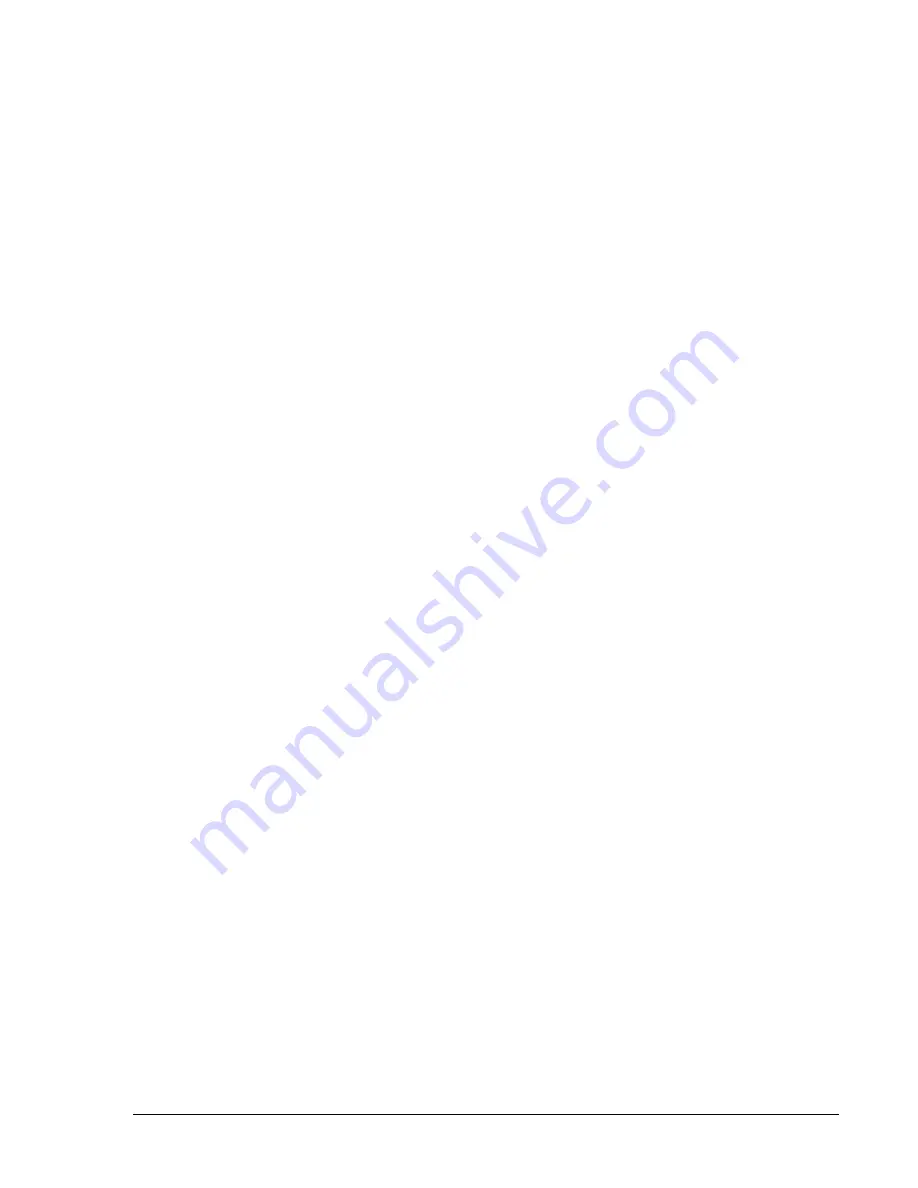
BE1-CDS220
Testing And Maintenance
13-9
Before testing each protection and control function, the logic settings should be examined to determine:
•
The mode setting for the function so that you know what the relay is supposed to do.
•
Which virtual output logic expressions contain the logic variables that represent the outputs of the
function under test so that the proper contact can be monitored.
•
The input logic expressions for the function under test (especially the block input because it
renders the function disabled if the block input is asserted).
•
That the fault reporting settings are properly set such that the relay properly indicates pickup and
trip states and records targets. These settings are set from the ASCII command interface using
the SG-TRIGGER and SG-TARG setting commands. See Section 6, Reporting and Alarm
Functions, Fault Reporting Functions, for more details.
Testing Phase Differential Protection with Internal Compensation
The internal phase and zero sequence compensation features of the relay can combine the currents from
multiple CT input circuits and/or subtract out the zero sequence components before their use by the phase
differential function. Thus, the testing of this function with the internal compensation features can be
somewhat complicated. For this reason, a detailed test procedure is provided for verifying the set points of
this function with internal compensation. See Sidebar 13-1 in this Section for more information on how the
internal compensation features work.
Step 1.
Record settings for the following tests.
The settings for the following tests should be recorded before starting the test. You will refer to these
settings throughout the test procedure.
•
Angle Compensation and Ground Source compensation can be determined by matching the SG-
CT or Screen 6.3.1.1 settings with Table 3-2 in Section 3 and reading the right two columns to
determine what angle compensation is applied.
•
Tap Compensation settings in each setting group can be determined from screens 5.x.1.2 or
5.x.1.3 on the optional HMI. Or, the S#-TAP87 settings from the ASCII command interface if
manual tap adjust is used. If automatic tap adjust is used, it will be necessary to use the settings
and equations 4-1 and 4-2 from Section 4, Protection and Control Functions, Differential
Protection.
•
Restrained Minimum Pickup, Slope, and Unrestrained Pickup settings can be determined from
screens 5.x.1.1 on the optional HMI. Or, the S#-87 settings from the ASCII command interface.
Alternatively, all of these parameters can be determined from reading the Current Check Record provided
by the Differential Alarm Function. To use this method, use the commands in Table 13-6.
Table 13-7 lists the currents that will be seen by each 87 phase differential element after phase and zero
sequence compensation. This table is based upon the internal compensation chart in Section 3, Input and
Output Functions, Input Current. Examination of this table shows that for most cases, test current injection
using only one or two current sources will result in currents being applied to more than one 87 Phase
element. See Sidebar 13-1 for more information on testing and compensated currents. The following test
procedures will enable you to determine the test points and which phases will be tested.
Содержание BE1-CDS220
Страница 2: ......
Страница 10: ...viii Introduction BE1 CDS220 This page intentionally left blank...
Страница 36: ...ii Quick Start BE1 CDS220 This page intentionally left blank...
Страница 48: ...ii Input And Output Functions BE1 CDS220 This page intentionally left blank...
Страница 66: ...iv Protection and Control BE1 CDS220 This page intentionally left blank...
Страница 112: ...ii Metering BE1 CDS220 This page intentionally left blank...
Страница 116: ...5 4 Metering BE1 CDS220 This page intentionally left blank...
Страница 166: ...ii BESTlogic Programmable Logic BE1 CDS220 This page intentionally left blank...
Страница 176: ...7 10 BESTlogic Programmable Logic BE1 CDS220 This page intentionally left blank...
Страница 234: ...8 56 Application BE1 CDS220 This page intentionally left blank...
Страница 236: ...ii Security BE1 CDS220 This page intentionally left blank...
Страница 240: ...9 4 Security BE1 CDS220 This page intentionally left blank...
Страница 242: ...ii Human Machine Interface BE1 CDS220 This page intentionally left blank...
Страница 256: ...10 14 Human Machine Interface BE1 CDS220 This page intentionally left blank...
Страница 258: ...ii ASCII Command Interface BE1 CDS220 This page intentionally left blank...
Страница 289: ...BE1 CDS220 Installation 12 7 Figure 12 8 MX Case Horizontal Panel Mount Front View Overall Dimensions...
Страница 422: ...14 32 BESTCOMS Software BE1 CDS220 This page intentionally left blank...
Страница 424: ...ii Time Current Characteristics BE1 CDS220 This page intentionally left blank...
Страница 441: ...BE1 CDS220 Time Overcurrent Characteristic Curves A 17 Figure A 13 Time Characteristic Curve A Standard Inverse 99 1621...
Страница 442: ...A 18 Time Overcurrent Characteristic Curves BE1 CDS220 Figure A 14 Time Characteristic Curve B Very Inverse 99 1376...
Страница 443: ...BE1 CDS220 Time Overcurrent Characteristic Curves A 19 Figure A 15 Time Characteristic Curve C Extremely Inverse 99 1377...
Страница 444: ...A 20 Time Overcurrent Characteristic Curves BE1 CDS220 Figure A 16 Time Characteristic Curve G Long Time Inverse 99 1622...
Страница 452: ...ii Terminal Communication BE1 CDS220 This page intentionally left blank...
Страница 456: ...C 4 Terminal Communication BE1 CDS220 This page intentionally left blank...
Страница 458: ...ii Settings Calculations BE1 CDS220 This page intentionally left blank...
Страница 475: ......