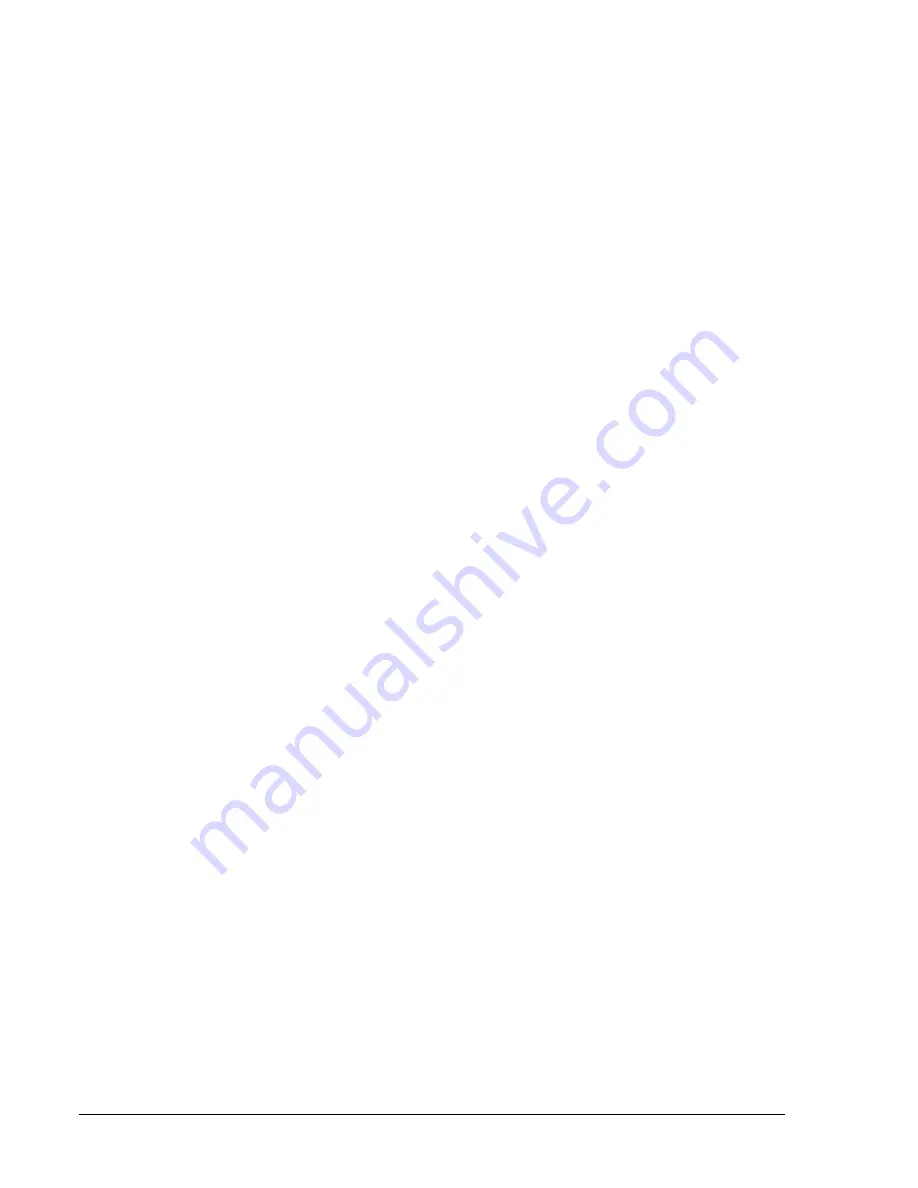
8-36 Application BE1-CDS220
Protection Elements
Referring to Figure 8-12, the 87, 150/151, 50/51 protection elements are connected to CT input 1, and the
Feeder Side of the 87 protection element is connected to input 2. The 87, 150/151, and 50/51 protection
elements are logic enabled to provide a trip by the settings shown in Table 8-21. Protection elements set
to 0 are setting disabled and will not provide a trip output even if logic enabled.
As shown in Figure 8-12, the BUS-W-BU scheme is typically applied with a BE1-851 on the feeder circuits
and a BE1-CDS220 on the transformer (not shown) supplying the bus. The transformer BE1-CDS220
provides an independent backup for bus faults with a coordination interval of 18 to 20 cycles. This
combination provides independent, overlapping backup protection in the event of a common mode failure
(refer to the discussion in Details of Preprogrammed Logic Schemes).
Typically, the 87 protection element provides high-speed percent restrained phase and ground protection
for faults inside the differential zone. For the BUS-W-BU application shown in Figure 8-12, the percent-
restrained differential protection function is the only function of the 87 protection element required. Set the
pickup of the 2
nd
, 5
th
, and 87U functions to 0 (setting disabled). The 87U function has a setting only when
the 2
nd
and 5
th
harmonic restraint functions are set for transformers (refer to the discussion in Overview of
Preprogrammed Logic Schemes).
Typically, the 150 and 151 protection elements are coordinated with the bus and feeder protection to
provide Phase, Neutral, and Negative Sequence instantaneous and timed backup protection for bus and
feeder faults.
Typically, the 51 protection element is coordinated with the low-side feeder protection to provide Phase,
Neutral, and Negative Sequence timed backup protection for feeder faults should feeder protection be out
of service. When a Feeder Relay out of Service signal is detected through IN7 of the BE1-CDS220
BUS-W-BU scheme, the relay switches from normal mode to feeder backup mode. The 251 protection
element is reset from setting group 0 to setting group 1 to provide time overcurrent feeder replacement
protection.
Typically, the 50T protection element is set to provide high-speed bus fault protection (2-4 cycles
coordination interval) when used with 851 feeder protection inputs as part of a bus interlocking scheme
(IN5 of the Bus BE1-CDS220). For normal mode, the 250T protection element should have a pickup
setting greater than the highest feeder instantaneous element to ensure that it will not pickup before any
feeder relay. When a Feeder Relay out of Service signal is detected through IN7 of the BE1-CDS220
BUS-W-BU, the relay switches from normal mode to feeder backup mode. The 250T protection element is
reset from setting group 0 to setting group 1 to provide instantaneous overcurrent feeder replacement
protection.
Integration of Protection, Control, and I/O Elements
The logic settings in Table 8-21 also include the logic equations that establish the control connections or
logic wiring between elements of the BUS-W-BU scheme. For example, the two underlined equations in
the settings of Table 8-21 provide the electrical connection between the 87 element (trip enabled by the
settings) and trip outputs 1 and 4. Referring to Figures 8-12 and 8-13, during the normal mode, the 87, 50,
and 51 protection elements (each trip enabled by the settings) trip through outputs 1 and 4. The 150 and
151 protection elements and the 101 virtual switch element (also trip enabled by the settings) trip through
output 4. During the feeder backup mode, the 50T and 51 protection elements are rerouted from output 1
and output 4, to output 3 to provide feeder protection. Protection elements set at 0 are setting disabled
and will not provide a trip output even if logic enabled.
As shown in Figure 8-12, IN7 of the BUS-W-BU signals the scheme that a feeder relay is out of service.
This input instructs the BE1-CDS220 relay to switch from the normal mode of interlocked bus protection to
the feeder backup mode.
As shown in Figure 8-12, IN5 of the BUS-W-BU scheme is hard wired to the feeder protection relays
(BE1-851). This signal path provides the intelligence that allows the BUS-W-BU to determine if a fault is
on the bus or on a feeder circuit. When any feeder overcurrent elements are picked up and timing, a
signal at IN5 of the BE1-CDS220 bus blocks the 50T protection elements. The pickup of the 50T
protection element is delayed 2 to 4 cycles to allow time for the feeder protection to detect, pickup, and
start timing. If the fault is not on a feeder, the 50T protection element of the BE1-CDS220 bus is not
blocked and trips in 2 to 4 cycles through outputs 1 and 4 as previously discussed. The overlapping 250T
Содержание BE1-CDS220
Страница 2: ......
Страница 10: ...viii Introduction BE1 CDS220 This page intentionally left blank...
Страница 36: ...ii Quick Start BE1 CDS220 This page intentionally left blank...
Страница 48: ...ii Input And Output Functions BE1 CDS220 This page intentionally left blank...
Страница 66: ...iv Protection and Control BE1 CDS220 This page intentionally left blank...
Страница 112: ...ii Metering BE1 CDS220 This page intentionally left blank...
Страница 116: ...5 4 Metering BE1 CDS220 This page intentionally left blank...
Страница 166: ...ii BESTlogic Programmable Logic BE1 CDS220 This page intentionally left blank...
Страница 176: ...7 10 BESTlogic Programmable Logic BE1 CDS220 This page intentionally left blank...
Страница 234: ...8 56 Application BE1 CDS220 This page intentionally left blank...
Страница 236: ...ii Security BE1 CDS220 This page intentionally left blank...
Страница 240: ...9 4 Security BE1 CDS220 This page intentionally left blank...
Страница 242: ...ii Human Machine Interface BE1 CDS220 This page intentionally left blank...
Страница 256: ...10 14 Human Machine Interface BE1 CDS220 This page intentionally left blank...
Страница 258: ...ii ASCII Command Interface BE1 CDS220 This page intentionally left blank...
Страница 289: ...BE1 CDS220 Installation 12 7 Figure 12 8 MX Case Horizontal Panel Mount Front View Overall Dimensions...
Страница 422: ...14 32 BESTCOMS Software BE1 CDS220 This page intentionally left blank...
Страница 424: ...ii Time Current Characteristics BE1 CDS220 This page intentionally left blank...
Страница 441: ...BE1 CDS220 Time Overcurrent Characteristic Curves A 17 Figure A 13 Time Characteristic Curve A Standard Inverse 99 1621...
Страница 442: ...A 18 Time Overcurrent Characteristic Curves BE1 CDS220 Figure A 14 Time Characteristic Curve B Very Inverse 99 1376...
Страница 443: ...BE1 CDS220 Time Overcurrent Characteristic Curves A 19 Figure A 15 Time Characteristic Curve C Extremely Inverse 99 1377...
Страница 444: ...A 20 Time Overcurrent Characteristic Curves BE1 CDS220 Figure A 16 Time Characteristic Curve G Long Time Inverse 99 1622...
Страница 452: ...ii Terminal Communication BE1 CDS220 This page intentionally left blank...
Страница 456: ...C 4 Terminal Communication BE1 CDS220 This page intentionally left blank...
Страница 458: ...ii Settings Calculations BE1 CDS220 This page intentionally left blank...
Страница 475: ......