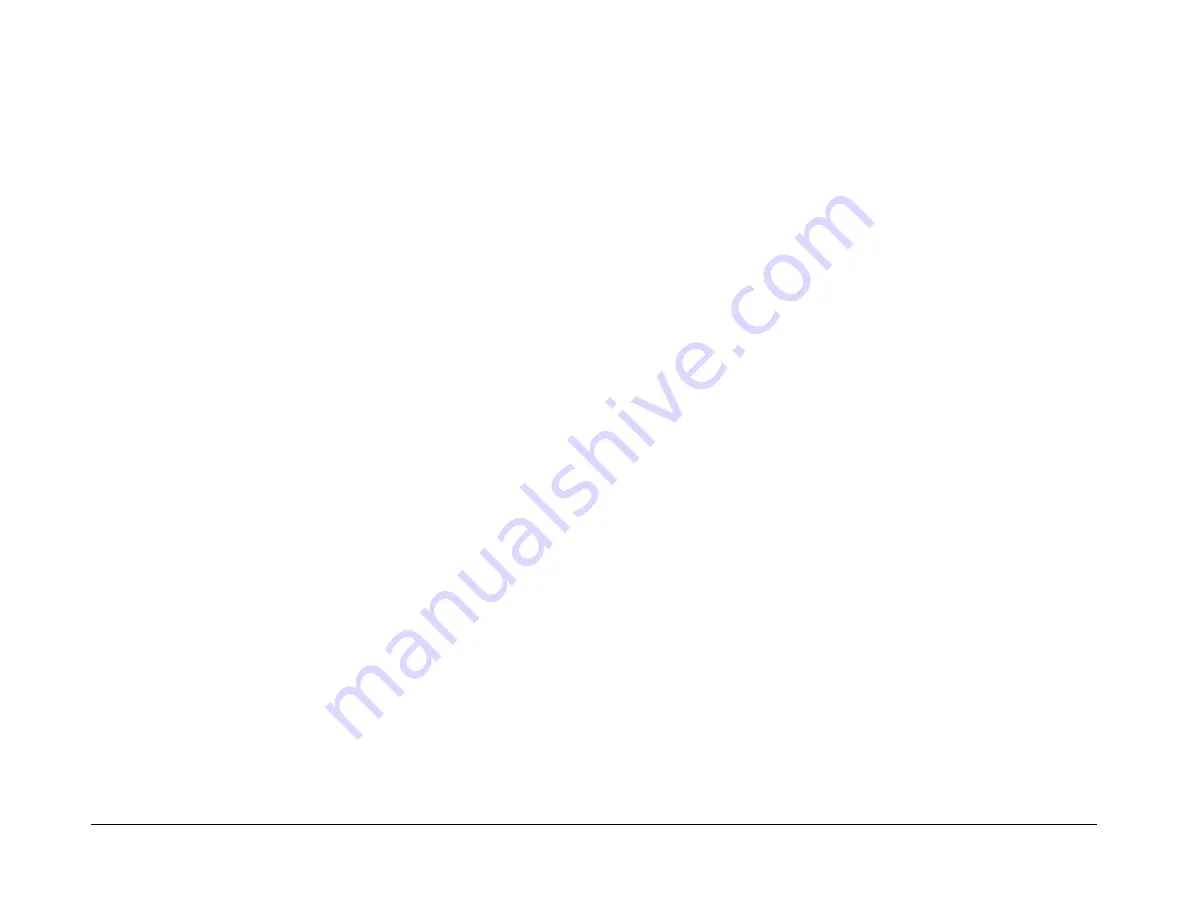
February 2013
2-102
ColorQube® 9303 Family
12H-110, 12J-110
Status Indicator RAPs
12H-110 Copy Damage in the LCSS RAP
Use this RAP to identify and correct the causes of copy damage in the LCSS.
Procedure
WARNING
Ensure that the electricity to the machine is switched off while performing tasks that do
not need electricity. Refer to
GP 14
. Disconnect the power cord. Electricity can cause
death or injury. Moving parts can cause injury.
WARNING
Take care not to topple the LCSS. The LCSS is unstable when undocked from the
machine. Do not show the customer how to undock the LCSS.
Check the following:
•
Look for torn paper in the LCSS paper path. Torn fragments can pass through the IOT and
LCSS paper path without causing a problem until they finally wedge themselves at some
point. A likely place for a piece of paper to be wedged is at the hole punch assembly,
where the top and bottom guides form the narrowest part of the paper path.
•
Ensure that the shaft diverter assembly,
PL 12.60 Item 13
, operates correctly and has full
movement.
•
Ensure that the hole punches park at the fully open position. If they protrude even slightly,
a jam will occur in the narrow paper path of the hole punch.
•
Ensure that the jam clearance guide,
PL 12.70 Item 6
, closes and latches correctly. Check
that the magnet at the rear is located and functions correctly. Check the clip at the front is
positioned correctly,
PL 12.70 Item 7
.
•
Ensure that all idler rolls in the LCSS paper path are free to rotate, particularly those on
the jam clearance guide, where the paper turns through 90 degrees.
•
Ensure that the paper path ribs of the jam clearance guide,
PL 12.70 Item 6
, and the entry
guide cover,
PL 12.70 Item 5
, are free of scores and nicks. Check also for contamination
and glue from label stock.
12J-110 Mis-Registration in Stapled Sets and Non-Stapled
Sets RAP
Use this RAP to identify and correct the causes of mis-registration in stapled sets, resulting in
staples missing some sheets in the set, or poorly registered non-stapled sets.
Procedure
WARNING
Ensure that the electricity to the machine is switched off while performing tasks that do
not need electricity. Refer to
GP 14
. Disconnect the power cord. Electricity can cause
death or injury. Moving parts can cause injury.
WARNING
Take care not to topple the LCSS. The LCSS is unstable when undocked from the
machine. Do not show the customer how to undock the LCSS.
The most likely cause of mis-registration is paper condition and/or damage such as curl, wrin-
kle, creases, dog ears, etc.
Curl, wrinkle and creases are probably caused in the IOT, go to
IQ 1
Image Quality Entry RAP.
For other copy/print damage and dog ears, go to the
12H-110
Copy Damage in the LCSS RAP.
Check the following:
•
Check that bin 1 is seated correctly and the bin 1 alignment clip is in position,
PL 12.10
Item 13
.
•
Turn over the paper stack in the tray in use.
•
Use a new ream of paper in the tray in use.
•
Paper type, especially recycled paper, can lead to registration problems. Try changing to
a different brand or type of paper.
•
Ensure that the guides in the paper trays are correctly set and reported on the UI for the
paper size loaded.
•
Check that paper type is set correctly. If heavyweight paper is used but not set in the UI,
the compiler capacity can be exceeded.
•
Check for obstructions in the compiler.
•
Ensure that the paddle roll operates correctly and that the paddles are not damaged. The
paddles should park completely inside the top section of the compiler, with the shorter
paddle in a vertical position. If all of the paddles are out of position, check the paddle roll
position sensor,
PL 12.25 Item 11
, the flag,
PL 12.25 Item 7
and the paddle motor assem-
bly,
PL 12.25 Item 10
. If only one paddle is mis-aligned with the others, it can be re-posi-
tioned by hand (they are not bonded to the shaft).
•
Ensure that the tampers operate correctly, i.e. are not stalling or losing position during the
job. Inspect the tampers for damage, if necessary install new parts.
PL 12.45
.
•
Inspect the bin 1 entry nips for roll damage. The idlers should be held against the rubber
driving rolls and they should be free to rotate within their support springs. If necessary,
install new parts,
PL 12.65
.
•
Inspect the four spring loaded guides on the output cover,
PL 12.10 Item 7
. Ensure that
they are correctly located and are free to move up and down.
Summary of Contents for ColorQube 9303 Series
Page 1: ...Xerox ColorQube 9303 Family Service Manual 708P90290 February 2013...
Page 4: ...February 2013 ii ColorQube 9303 Family Introduction...
Page 18: ...February 2013 1 2 ColorQube 9303 Family Service Call Procedures...
Page 92: ...February 2013 2 68 ColorQube 9303 Family 05F Status Indicator RAPs...
Page 104: ...February 2013 2 80 ColorQube 9303 Family 12 701 00 65 Status Indicator RAPs...
Page 200: ...February 2013 2 176 ColorQube 9303 Family 12N 171 Status Indicator RAPs...
Page 292: ...February 2013 2 268 ColorQube 9303 Family 16D Status Indicator RAPs...
Page 320: ...February 2013 2 296 ColorQube 9303 Family 42 504 00 42 505 00 Status Indicator RAPs...
Page 500: ...February 2013 2 476 ColorQube 9303 Family 94B Status Indicator RAPs...
Page 648: ...February 2013 3 2 ColorQube 9303 Family Image Quality...
Page 653: ...February 2013 3 7 ColorQube 9303 Family IQ 1 Image Quality Figure 1 IQ defects 1...
Page 654: ...February 2013 3 8 ColorQube 9303 Family IQ 1 Image Quality Figure 2 IQ defects 2...
Page 655: ...February 2013 3 9 ColorQube 9303 Family IQ 1 Image Quality Figure 3 IQ defects 3...
Page 656: ...February 2013 3 10 ColorQube 9303 Family IQ 1 Image Quality Figure 4 IQ defects 4...
Page 657: ...February 2013 3 11 ColorQube 9303 Family IQ 1 Image Quality Figure 5 IQ defects 5...
Page 658: ...February 2013 3 12 ColorQube 9303 Family IQ 1 Image Quality Figure 6 IQ defects 6...
Page 660: ...February 2013 3 14 ColorQube 9303 Family IQ 1 Image Quality Figure 9 IQ defects 9...
Page 661: ...February 2013 3 15 ColorQube 9303 Family IQ 1 Image Quality Figure 10 IQ defects 10...
Page 662: ...February 2013 3 16 ColorQube 9303 Family IQ 1 Image Quality Figure 11 IQ defects 11...
Page 663: ...February 2013 3 17 ColorQube 9303 Family IQ 1 Image Quality Figure 12 IQ defects 12...
Page 664: ...February 2013 3 18 ColorQube 9303 Family IQ 1 Image Quality Figure 13 IQ defects 13...
Page 728: ...February 2013 3 82 ColorQube 9303 Family IQ 29 IQ 30 Image Quality...
Page 736: ...February 2013 3 90 ColorQube 9303 Family TP 15 Image Quality Figure 2 Media path test pages...
Page 758: ...February 2013 3 112 ColorQube 9303 Family IQS 7 IQS 8 Image Quality...
Page 778: ...February 2013 4 20 ColorQube 9303 Family REP 1 9 Repairs Adjustments...
Page 794: ...February 2013 4 36 ColorQube 9303 Family REP 3 10 Repairs Adjustments...
Page 1144: ...February 2013 4 386 ColorQube 9303 Family REP 94 1 Repairs Adjustments...
Page 1176: ...February 2013 4 418 ColorQube 9303 Family ADJ 62 3 ADJ 62 4 Repairs Adjustments...
Page 1182: ...February 2013 4 424 ColorQube 9303 Family ADJ 75 3 Repairs Adjustments...
Page 1184: ...February 2013 4 426 ColorQube 9303 Family ADJ 82 1 Repairs Adjustments...
Page 1186: ...February 2013 4 428 ColorQube 9303 Family ADJ 91 1 Repairs Adjustments...
Page 1552: ...February 2013 6 260 ColorQube 9303 Family dC140 General Procedures Information...
Page 1576: ...February 2013 6 284 ColorQube 9303 Family dC640 General Procedures Information...
Page 1578: ...February 2013 6 286 ColorQube 9303 Family dC708 dC715 General Procedures Information...
Page 1600: ...February 2013 7 2 ColorQube 9303 Family Wiring Data...
Page 1696: ...February 2013 8 2 ColorQube 9303 Family Principles of Operation...
Page 1808: ...February 2013 8 114 ColorQube 9303 Family Principles of Operation...
Page 1809: ...XEROX EUROPE...
Page 1810: ...XEROX EUROPE...
Page 1811: ...XEROX EUROPE...
Page 1812: ...XEROX EUROPE...