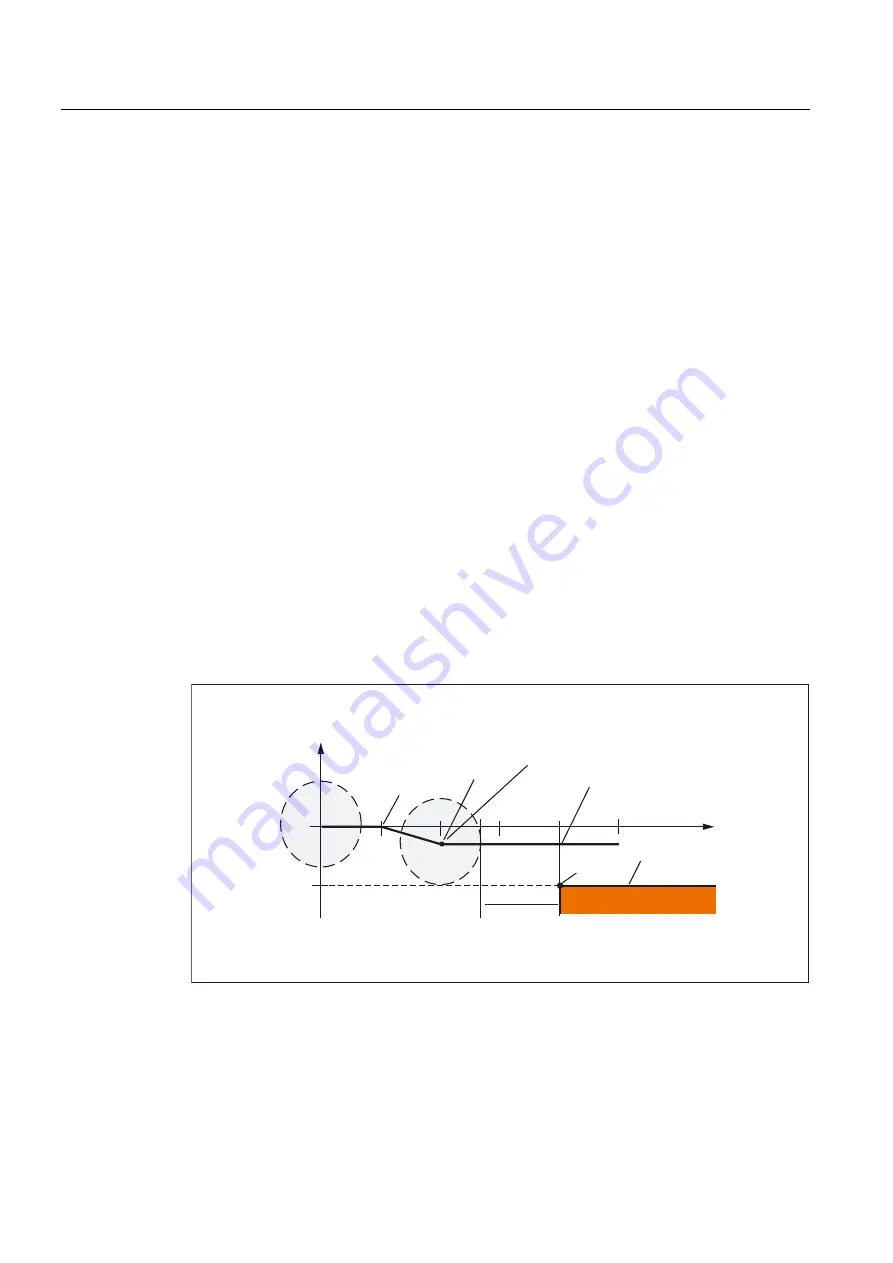
Detailed Description
2.4 Tool radius compensation 2D (TRC)
Basic logic functions: Tool Offset (W1)
64
Function Manual, 11/2006, 6FC5397-0BP10-2BA0
Example:
An approach is made with
G17
starting at position Z=20 of point P
1
. The SAR plane defined
by P
3
is at Z=0. The point defined by
DISCL
must, therefore, lie between these two points.
MD20204=0.010. If P
2
is between 20.000 and 20.010 or between 0 and -0.010, it is assumed
that the value 20.0 or 0.0 is programmed. The alarm is output if the Z position of P
2
is greater
than 20.010 or less than -0.010.
Depending on the relative position of start point P
0
and end point P
4
with reference to the
machining plane, the infeed movements are performed in the negative (normal for approach)
or positive (normal for retraction) direction, i.e., with
G17
it is possible for the Z component of
end point P
4
to be greater than that of start point P
0
.
Programming the end point P
4
(or P
0
for retraction) generally with X.... Y... Z...
Possible ways of programming the end point P
4
for approach
End point P
4
can be programmed in the actual SAR block.
P
4
can be determined by the end point of the next traversing block.
Further blocks (dummy blocks) can be inserted between the SAR block and the next
traversing block without moving the geometry axes.
The end point is deemed to have been programmed in the actual SAR block for approach if
at least one geometry axis is programmed on the machining plane (X or Y with
G17
). If only
the position of the axis perpendicular to the machining plane (Z with
G17
) is programmed in
the SAR block, this component is taken from the SAR block, but the position in the plane is
taken from the following block. In this case, an alarm is output if the axis perpendicular to the
machining plane is also programmed in the following block.
Example:
&RQWRXU
0DFKLQLQJXSWRWKLV
SRLQWZLWK*WKHQZLWK
*)
]
=
=
',65
;
3
<
Summary of Contents for SINUMERIK 840D sl
Page 282: ...Index Basic logic functions Acceleration B2 64 Function Manual 11 2006 6FC5397 0BP10 2BA0 ...
Page 388: ...Basic logic functions Travel to fixed stop F1 Function Manual 11 2006 6FC5397 0BP10 2BA0 52 ...
Page 962: ...Index Basic logic functions Emergency Stop N2 20 Function Manual 11 2006 6FC5397 0BP10 2BA0 ...
Page 1704: ...Constraints Basic logic functions Spindles S1 94 Function Manual 11 2006 6FC5397 0BP10 2BA0 ...
Page 1716: ...Index Basic logic functions Spindles S1 106 Function Manual 11 2006 6FC5397 0BP10 2BA0 ...
Page 1996: ...Index Basic logic functions Tool Offset W1 208 Function Manual 11 2006 6FC5397 0BP10 2BA0 ...
Page 2150: ...Table of contents Basic logic functions Appendix 4 Function Manual 11 2006 6FC5397 0BP10 2BA0 ...
Page 2184: ...Glossary Basic logic functions Appendix 38 Function Manual 11 2006 6FC5397 0BP10 2BA0 ...