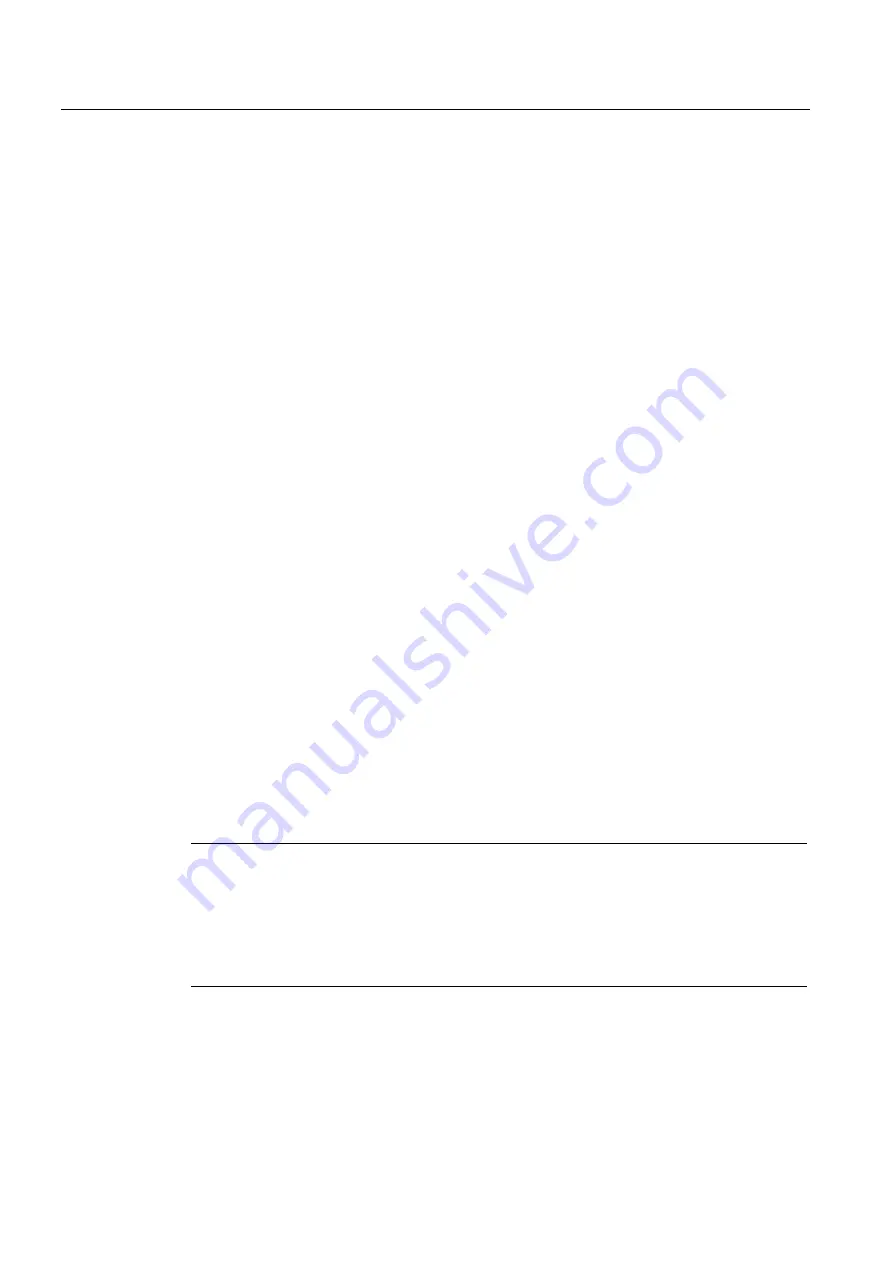
Detailed description
2.12 Block descriptions
Basic logic functions: PLC Basic program powerline (P3 pl)
170
Function Manual, 11/2006, 6FC5397-0BP10-2BA0
2.12.9
FB 11: Brake test
Description of Functions
The braking operation check should be used for all axes, which must be prevented from
moving in an uncontrolled manner by a holding brake. This check function is primarily
intended for the socalled "vertical axes".
The machine manufacturer can use his PLC user program to close the brake at a suitable
moment in time (guide value every 8 hours, similar to the SI test stop) and allow the drive to
produce an additional torque/additional force equivalent to the weight of the axis. In errorfree
operation, the brake can produce the necessary braking torque/braking force and keep the
axis at a virtual standstill. When an error occurs, the actual position value exits the
parameterizable monitoring window. In this instance, the position controller prevents the axis
from sagging and negatively acknowledges the mechanical brake test.
The necessary parameterization of NC and the drive is described in:
References:
/FBSI/ Function Description Safety Integrated
The brake test must always be started when the axis is at a standstill. For the entire duration
of the brake test, the enable signals of the parameterized axis must be set to Enable (e.g.,
the servo disable, feedrate enable signals). Further, the signal to axis/spindle DB31, ...
DBX28.7 (PLC controls axis) is to be set to state 1 by the user program during the complete
test.
Before activating the signal DB31, ... DBX28.7 (PLC controls axis) the axis is to be switched
as "neutral axis" e.g. the DB31 is, ... DB8.0-8.3 (assign NC-axis channel) is to be set to
channel 0 as well as DB31, ... DB8.4 (activation signal when the byte is changed) is to be
set.
The checkback signal
•
about the current state can be queried in the byte DB31, ... DBB68.
•
the NC about the signal DB31, ... DBX63.1 (PLC controls axis) is to be awaited before the
block is started. The direction in which the drive must produce its torque/force is specified
by the PLC in the form of a "traversing motion" (e.g., via FC 18).
The axis must be able to reach the destination of this movement without risk of collision if the
brake is unable to produce the necessary torque/force.
Note
Instructions for FC 18
In case FC 15, FC 16 or FC 18 are called for the same axis in the remainder of the user
programs, the calls must be mutually interlocked. For example, this can be achieved via a
common call of this function with an interlocked common data interface for the FC 18
parameters. A second option is to call the FC18 repeatedly, in which case the inactive FC18
will not be processed by the program. A multiple-use interlock must be provided.
Summary of Contents for SINUMERIK 840D sl
Page 282: ...Index Basic logic functions Acceleration B2 64 Function Manual 11 2006 6FC5397 0BP10 2BA0 ...
Page 388: ...Basic logic functions Travel to fixed stop F1 Function Manual 11 2006 6FC5397 0BP10 2BA0 52 ...
Page 962: ...Index Basic logic functions Emergency Stop N2 20 Function Manual 11 2006 6FC5397 0BP10 2BA0 ...
Page 1704: ...Constraints Basic logic functions Spindles S1 94 Function Manual 11 2006 6FC5397 0BP10 2BA0 ...
Page 1716: ...Index Basic logic functions Spindles S1 106 Function Manual 11 2006 6FC5397 0BP10 2BA0 ...
Page 1996: ...Index Basic logic functions Tool Offset W1 208 Function Manual 11 2006 6FC5397 0BP10 2BA0 ...
Page 2150: ...Table of contents Basic logic functions Appendix 4 Function Manual 11 2006 6FC5397 0BP10 2BA0 ...
Page 2184: ...Glossary Basic logic functions Appendix 38 Function Manual 11 2006 6FC5397 0BP10 2BA0 ...