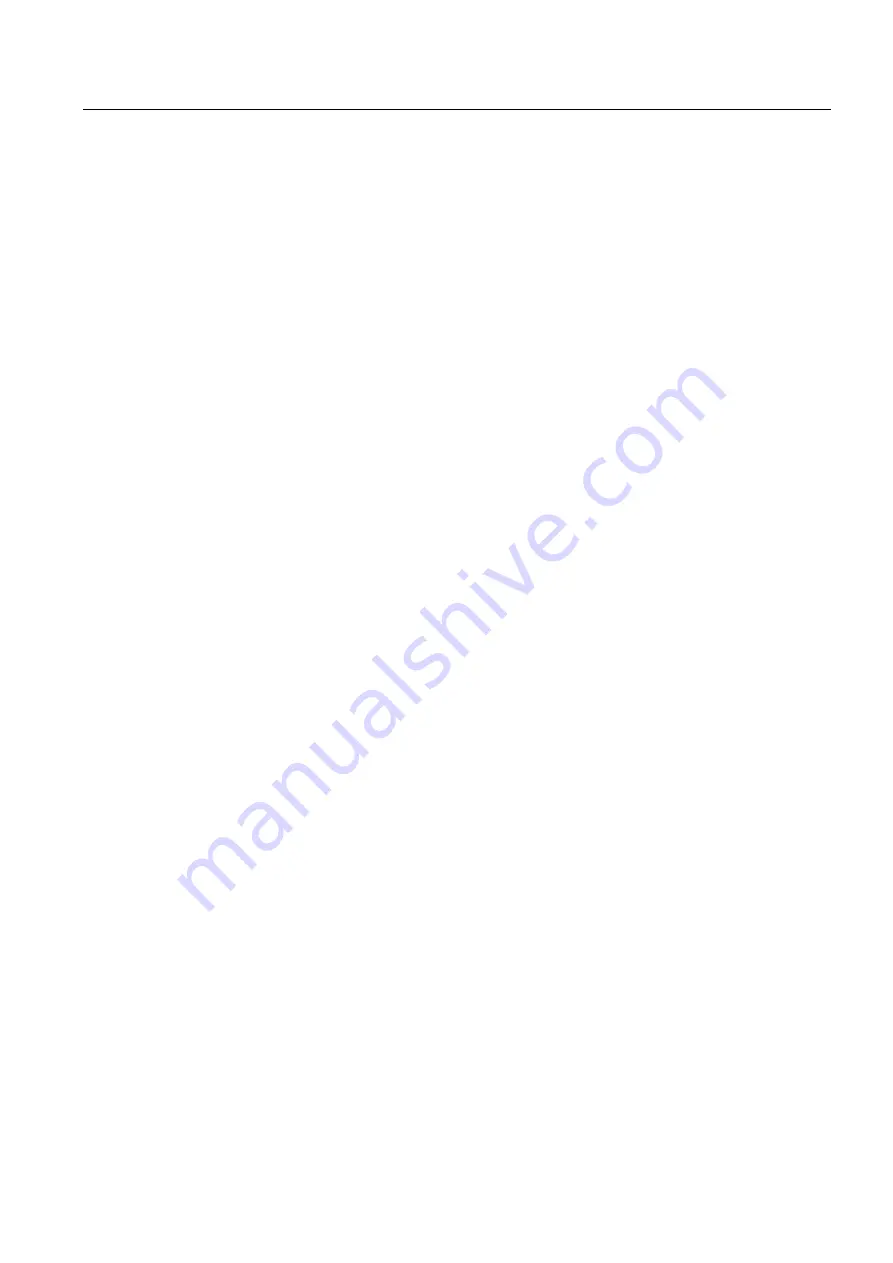
Detailed Description
2.5 Toolholder with orientation capability
Basic logic functions: Tool Offset (W1)
Function Manual, 11/2006, 6FC5397-0BP10-2BA0
123
Tool fine compensation combined with orientation
Tool fine compensations and toolholders cannot be combined. The activation of tool fine
compensation when a toolholder is active, and vice versa the activation of the toolholder
when tool fine compensation is active, produces an alarm.
Automatic toolholder selection, RESET
For
RESET
or at program start, a toolholder can be selected automatically via the machine
data:
MD20126 $MC_TOOL_CARRIER_RESET_VALUE (Active toolholder at RESET)
It is handled similar to the controlled selection of a tool via the machine data:
MD20120 $MC_TOOL_RESET_VALUE (Tool length compensation Power up (RESET/TP-
End))
The behavior at
RESET
or at program start is controlled as in the case of tool selection via
the same bit 6 in the machine data:
MD20110 $MC_RESET_MODE_MASK (definition of initial control settings after RESET/TP-
End)
Or:
MD20112 $MC_START_MODE_MASK (definition of initial control system settings at NC-
START)
References:
/FB1/ Function Manual Basic Functions; Mode Group, Channel, Program Operation, Reset
Response (K1)
SW 6.3 and higher
If
TCOABS
was active for the last selection before reset, the behavior is unchanged
compared to previous versions. A different active G code causes the toolholder with
orientation capability to be activated with the frame that was active before the last reset.
Modified toolholder data ($TC_CARR...) are also considered. If these data are unchanged,
the toolholder is activated in exactly the same state as before reset. If the toolholder data
were changed after the toolholder selection before reset, selection corresponding to the last
frame is not always possible. In this case, the toolholder with orientation capability is
selected according to the G-Code (group 42) values valid at this time and the active frame.
MD22530 output of auxiliary functions to PLC
That, optionally, a constant or an M code is output when the toolholder is selected, whose
number of the code is derived from the toolholder number. Can be set with the machine
data:
MD22530 $MC_TOCARR_CHANGE_M_CODE (M-Code at toolholder change)
References:
/FB1/ Function Manual Basic Functions; Output of Auxiliary Functions to PLC (H2)
Summary of Contents for SINUMERIK 840D sl
Page 282: ...Index Basic logic functions Acceleration B2 64 Function Manual 11 2006 6FC5397 0BP10 2BA0 ...
Page 388: ...Basic logic functions Travel to fixed stop F1 Function Manual 11 2006 6FC5397 0BP10 2BA0 52 ...
Page 962: ...Index Basic logic functions Emergency Stop N2 20 Function Manual 11 2006 6FC5397 0BP10 2BA0 ...
Page 1704: ...Constraints Basic logic functions Spindles S1 94 Function Manual 11 2006 6FC5397 0BP10 2BA0 ...
Page 1716: ...Index Basic logic functions Spindles S1 106 Function Manual 11 2006 6FC5397 0BP10 2BA0 ...
Page 1996: ...Index Basic logic functions Tool Offset W1 208 Function Manual 11 2006 6FC5397 0BP10 2BA0 ...
Page 2150: ...Table of contents Basic logic functions Appendix 4 Function Manual 11 2006 6FC5397 0BP10 2BA0 ...
Page 2184: ...Glossary Basic logic functions Appendix 38 Function Manual 11 2006 6FC5397 0BP10 2BA0 ...