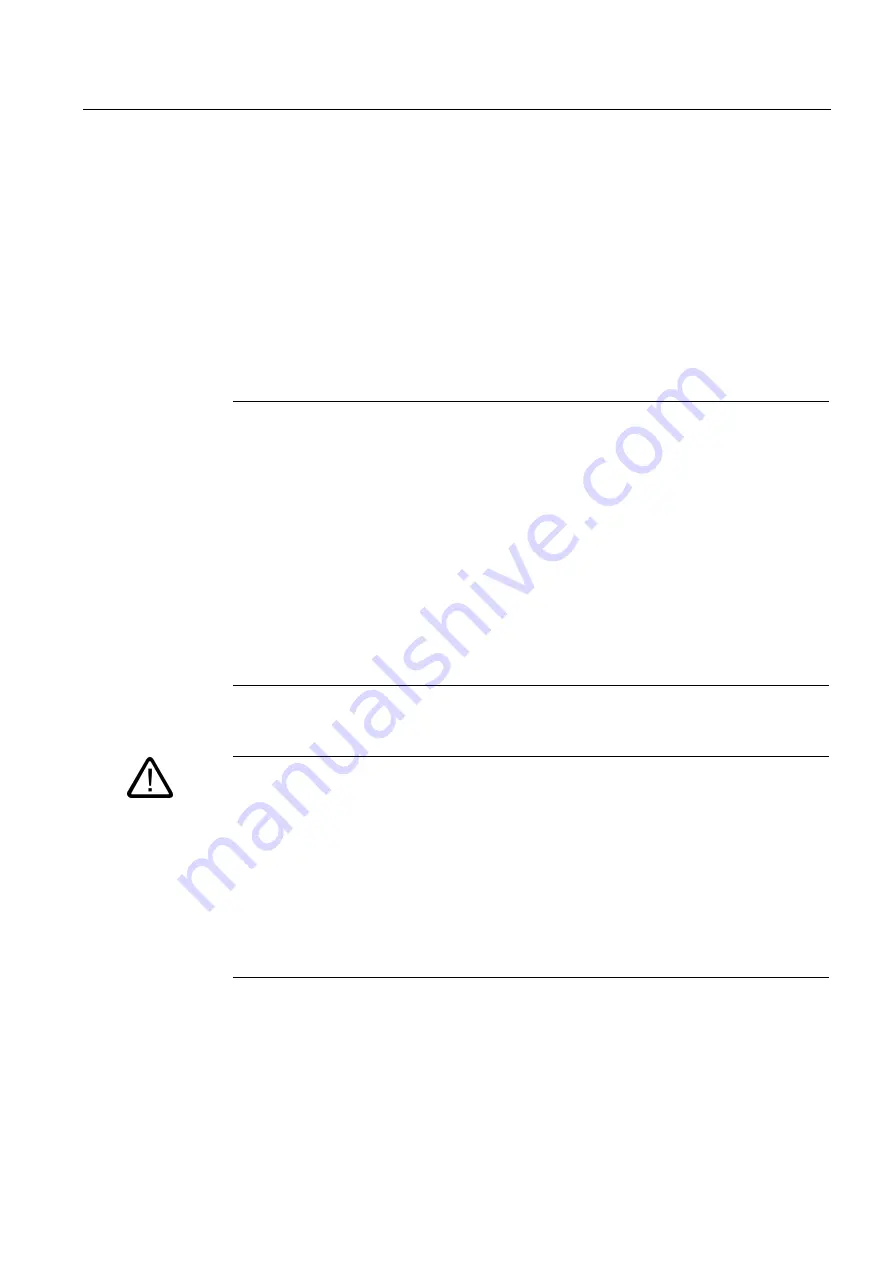
Detailed description
2.6 Referencing with absolute value encoders
Basic logic functions: Reference Point Approach (R1)
Function Manual, 11/2006, 6FC5397-0BP10-2BA0
35
Readjustment
Readjustment of the absolute encoder is required after:
•
Gear change between load and absolute encoder
•
Removal/installation of the absolute value encoder
•
Removal/installation of the motor with the absolute value encoder
•
Data loss in the static NC memory
•
Battery failure
•
Setting actual value (
PRESETON
)
Notice
The NCK can only detect a required readjustment during the following events:
•
Gear change with change of gear ratio
•
Addressing the zero-mark monitoring
•
New encoder serial number after change of the absolute value encoder
Thereupon, the status of the absolute encoder is automatically reset by NCK to 0
(encoder not calibrated) (MD34210 = 0) and the following alarm is displayed:
Alarm 25022 "Axis <Axis identifier> Encoder <Number> Warning 0"
or when addressing the zero-mark monitoring (only systems with SIMODRIVE 611D):
Alarm 25020 "Axis <Axis identifier> Zero-mark monitoring of the active encoder"
In all other cases (e.g.
PRESETON
) it is the sole responsibility of the user, by resetting the
status to 0 (encoder not adjusted), to show the misalignment of the absolute value
encoder and to carry out a readjustment.
Warning
Data backup
During the back-up of machine data of a machine A, the encoder status of the machine
axis (MD34210) is also backed up.
During loading of this data record into a machine B of the same type, e.g. in the context
of a serial start-up or after a case of maintenance, the referenced machine axes will be
automatically regarded as adjusted / referenced by the NC. It is the special responsibility
of the machine manufacturer / user to undertake a readjustment in such cases.
See also explanations regarding machine data:
MD30250 $MA_ACT_POS_ABS (Absolute encoder position at the time of switch-off)
Summary of Contents for SINUMERIK 840D sl
Page 282: ...Index Basic logic functions Acceleration B2 64 Function Manual 11 2006 6FC5397 0BP10 2BA0 ...
Page 388: ...Basic logic functions Travel to fixed stop F1 Function Manual 11 2006 6FC5397 0BP10 2BA0 52 ...
Page 962: ...Index Basic logic functions Emergency Stop N2 20 Function Manual 11 2006 6FC5397 0BP10 2BA0 ...
Page 1704: ...Constraints Basic logic functions Spindles S1 94 Function Manual 11 2006 6FC5397 0BP10 2BA0 ...
Page 1716: ...Index Basic logic functions Spindles S1 106 Function Manual 11 2006 6FC5397 0BP10 2BA0 ...
Page 1996: ...Index Basic logic functions Tool Offset W1 208 Function Manual 11 2006 6FC5397 0BP10 2BA0 ...
Page 2150: ...Table of contents Basic logic functions Appendix 4 Function Manual 11 2006 6FC5397 0BP10 2BA0 ...
Page 2184: ...Glossary Basic logic functions Appendix 38 Function Manual 11 2006 6FC5397 0BP10 2BA0 ...