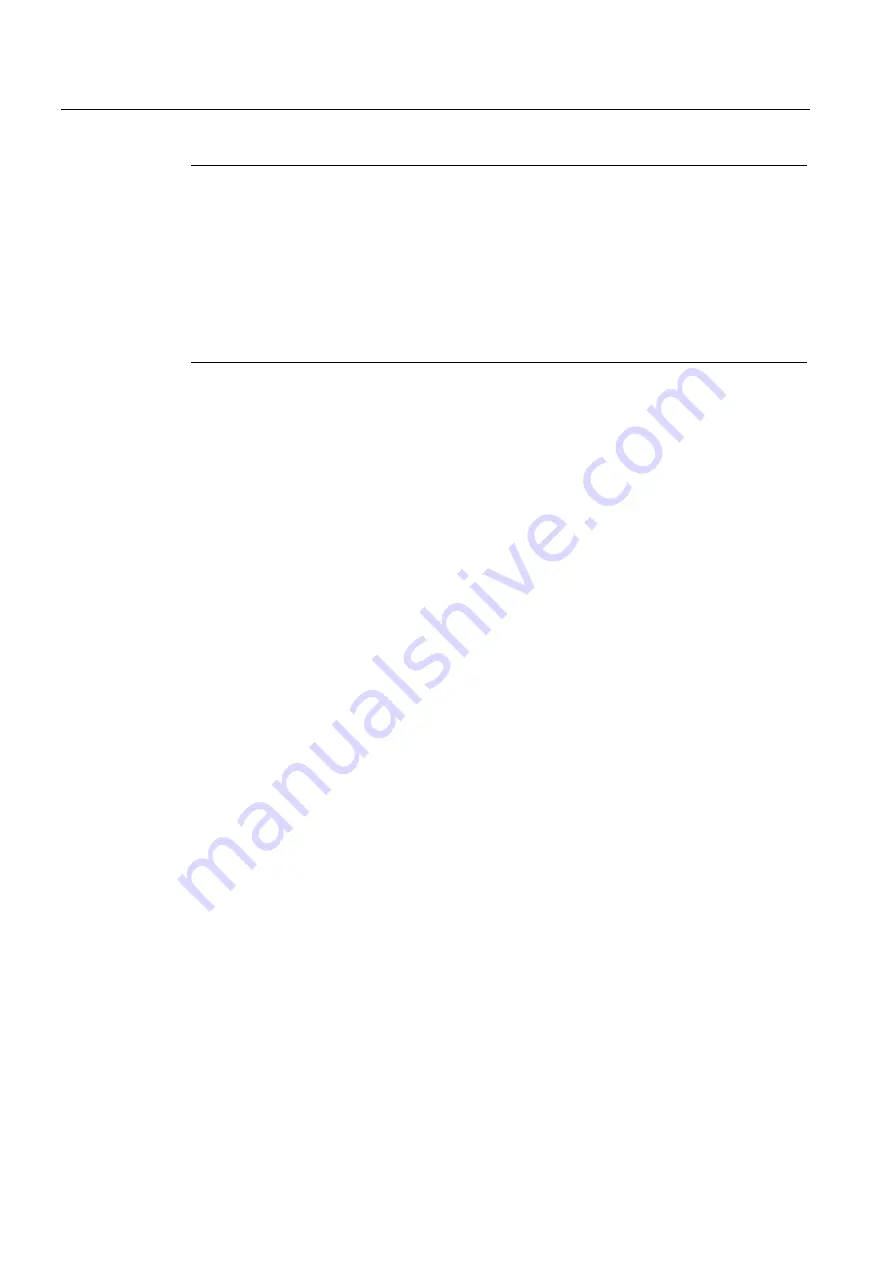
Detailed Description
2.5 Toolholder with orientation capability
Basic logic functions: Tool Offset (W1)
110
Function Manual, 11/2006, 6FC5397-0BP10-2BA0
Note
The required data cannot be determined unequivocally from the geometry of the toolholder,
i.e., the user is free to a certain extent to decide the data to be stored. Thus, for the example,
it is possible to specify only one z component for the tool base dimension up to the second
axis. In this case, l
2
would no longer be zero, but would contain the components of the
distance between this point on the second axis and a further point on the first axis. The point
on the first axis can also be selected freely. Depending on the point selected, l
1
must be
selected such that the reference point (which can also be selected freely) is reached.
In general: vector components that are not changed by rotation of an axis can be distributed
over any vectors "before" and "after" rotation.
2.5.3
Oblique machining with 3 + 2 axes
Description of function
Inclined machining with 3 + 2 axes describes an extension of the concept of toolholders with
orientation capability and applies this concept to machines with a rotary table, on which the
orientation of tool and table can be changed simultaneously.
The "Inclined machining with 3 + 2 axes" function is used to machine surfaces with any
rotation with reference to the main planes X/Y (
G17
), Z/X (
G18
) and Y/Z (
G19
).
It is possible to produce any orientation of the tool relative to the workpiece by rotating either
the tool, the workpiece or both the tool and the workpiece.
The software automatically calculates the necessary compensating movements resulting
from the tool lengths, lever arms and the angle of the rotary axis. It is always assumed that
the required orientation is set first and not modified during a machining process such as
pocket milling on an inclined plane.
Furthermore, the following 3 functions are described, which are required for oblique
machining:
•
Position programming in the direction of the tool orientation independent of an active
frame
•
Definition of a frame rotation by specifying the solid angle
•
Definition of the component of rotation in tool direction in the programmed frame while
maintaining the remaining frame components
Summary of Contents for SINUMERIK 840D sl
Page 282: ...Index Basic logic functions Acceleration B2 64 Function Manual 11 2006 6FC5397 0BP10 2BA0 ...
Page 388: ...Basic logic functions Travel to fixed stop F1 Function Manual 11 2006 6FC5397 0BP10 2BA0 52 ...
Page 962: ...Index Basic logic functions Emergency Stop N2 20 Function Manual 11 2006 6FC5397 0BP10 2BA0 ...
Page 1704: ...Constraints Basic logic functions Spindles S1 94 Function Manual 11 2006 6FC5397 0BP10 2BA0 ...
Page 1716: ...Index Basic logic functions Spindles S1 106 Function Manual 11 2006 6FC5397 0BP10 2BA0 ...
Page 1996: ...Index Basic logic functions Tool Offset W1 208 Function Manual 11 2006 6FC5397 0BP10 2BA0 ...
Page 2150: ...Table of contents Basic logic functions Appendix 4 Function Manual 11 2006 6FC5397 0BP10 2BA0 ...
Page 2184: ...Glossary Basic logic functions Appendix 38 Function Manual 11 2006 6FC5397 0BP10 2BA0 ...