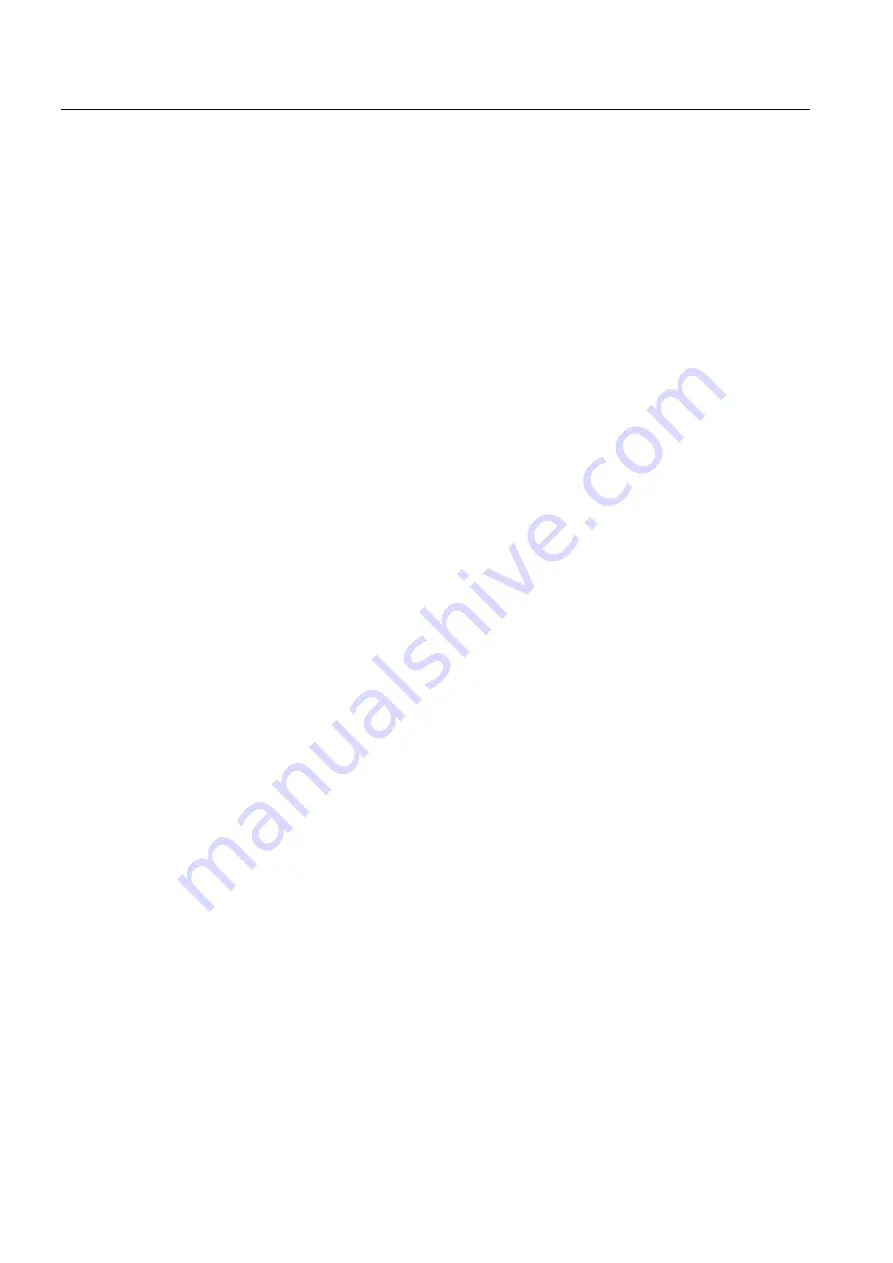
Detailed description
2.7 Program operation mode
Basic logic functions: Mode group, channel, program operation, reset response (K1)
130
Function Manual, 11/2006, 6FC5397-0BP10-2BA0
Parameterization by SETINT
An interrupt signal must be assigned to the part programs via NC instruction SETINT. This
turns the part program into an interrupt routine.
The following parameters can still be used in the SETINT instruction:
•
LIFTFAST: When the interrupt signal arrives, a "Fast retraction of the tool from the
contour" is executed before the interrupt routine starts. The motion direction for the fast
retraction is specified by NC address ALF.
•
BLSYNC: If this parameter is set, the current program block is processed and only then is
the interrupt routine started.
Variants for LIFTFAST fast retraction
If mirroring is active for execution via frames, then the following machine data can be used to
control whether the direction of retraction is to be mirrored as well during fast retraction.
MD21202 $MC_LIFTFAST_WITH_MIRROR (fast retraction with mirroring)
The displacement for the fast retraction is stored for the 3 geometry axes in MD21200
$MC_LIFTFAST_DIST (Displacement during fast retraction from contour).
In case of parameterized LIFTFAST (fast retraction) the maximum axis accelereation for
positioning operations is reduced by MD32300 $MA_MAX_AX_ACCEL (axis acceleration) by
the factor specified in the machine data MD20610 $MC_ADD_MOVE_ACCEL_RESERVE
(acceleration reserve for overlaid motions).
Activation of interrupt routine
Interrupt routines can be activated by two different methods:
•
By a 0/1 transition of the interrupt signal, triggered by a 0/1 transition at the rapid NC
input
•
By the call of function call ASUPST (/B1/, /P3/)
Upon activation, all machine axes are decelerated to a standstill according to the
acceleration ramp
(MD32300 $MA_MAX_AX_ACCEL (axis acceleration)), and the axis positions are stored.
Reorganizing
In addition to decelerating the axes, the previously decoded calculation blocks are calculated
back to the interruption block. i.e., all the variables, frames and G codes are assigned the
value that they would have at the point of interruption if the part program had not been
previously decoded. These values are put in the buffer so that they can be called up again
when the interrupt routine is completed.
Exceptions, where no reorganization is possible:
•
In thread cutting blocks
•
With complex geometries (e.g., spline or radius compensation)
Summary of Contents for SINUMERIK 840D sl
Page 282: ...Index Basic logic functions Acceleration B2 64 Function Manual 11 2006 6FC5397 0BP10 2BA0 ...
Page 388: ...Basic logic functions Travel to fixed stop F1 Function Manual 11 2006 6FC5397 0BP10 2BA0 52 ...
Page 962: ...Index Basic logic functions Emergency Stop N2 20 Function Manual 11 2006 6FC5397 0BP10 2BA0 ...
Page 1704: ...Constraints Basic logic functions Spindles S1 94 Function Manual 11 2006 6FC5397 0BP10 2BA0 ...
Page 1716: ...Index Basic logic functions Spindles S1 106 Function Manual 11 2006 6FC5397 0BP10 2BA0 ...
Page 1996: ...Index Basic logic functions Tool Offset W1 208 Function Manual 11 2006 6FC5397 0BP10 2BA0 ...
Page 2150: ...Table of contents Basic logic functions Appendix 4 Function Manual 11 2006 6FC5397 0BP10 2BA0 ...
Page 2184: ...Glossary Basic logic functions Appendix 38 Function Manual 11 2006 6FC5397 0BP10 2BA0 ...