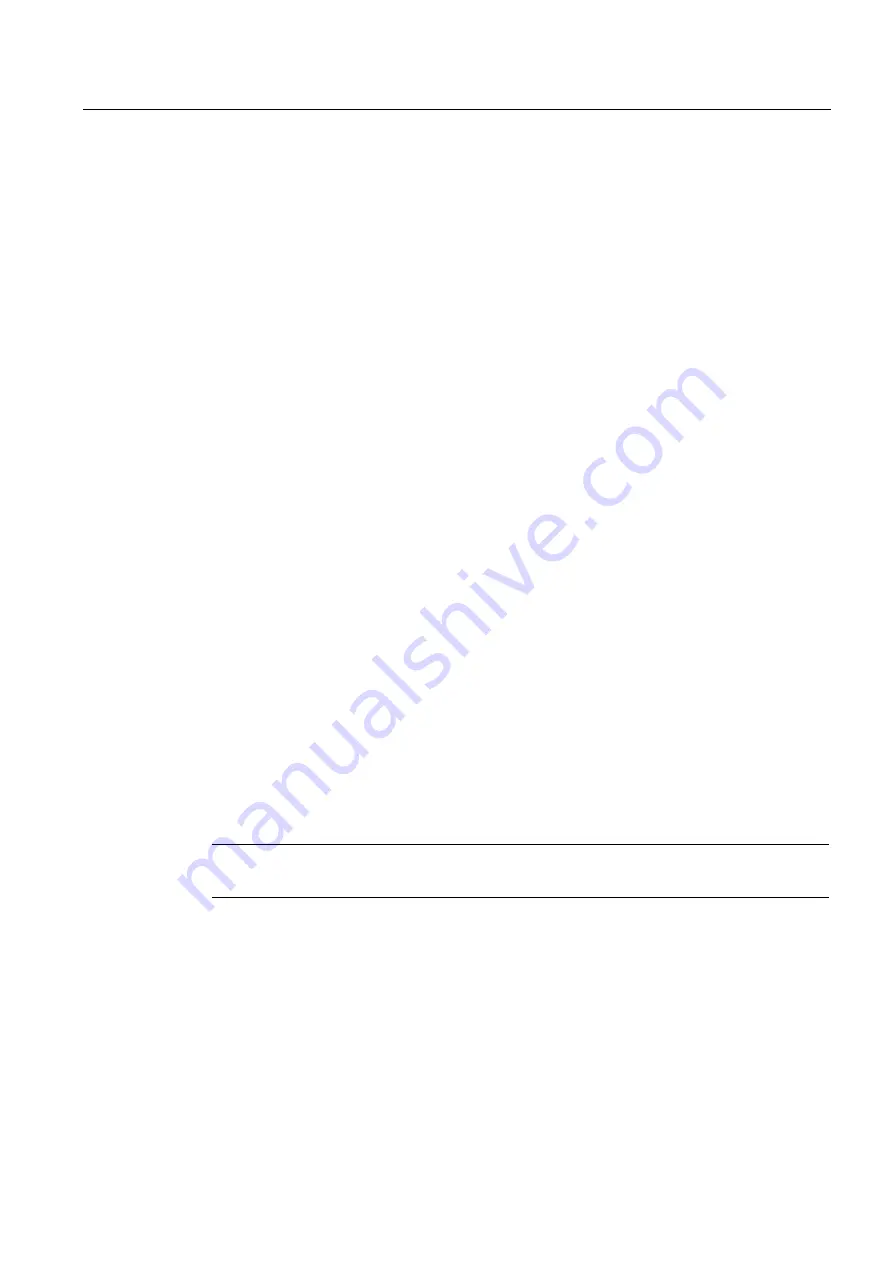
Detailed description
2.12 Block descriptions
Basic logic functions: PLC Basic program powerline (P3 pl)
Function Manual, 11/2006, 6FC5397-0BP10-2BA0
255
Multiple calls of FC 25 or FC 19, FC 24, FC 26 are permitted in a single PLC cycle. In this
case, the first call in the cycle drives the LED displays. Furthermore, all actions of the
parameterized block are carried out in the first call. In the following calls, only a reduced level
of processing of the channel and mode group interface takes place. The geometry axes are
supplied with directional data only in the first block call in the cycle.
Single block processing can be selected/deselected only in the first cycle.
The second machine control panel can be processed, when the parameter
"BAGNo" is incremented by B#16#10. When parameterizing, the HHU number is contained
in the lower nibble (lower 4 bits).
"BAGNo" = 0 or B#16#10 means that the mode group signals are not processed.
ChanNo = 0 means that the channel signals are not processed.
Flexible axis configuration
With SW V6 and higher, it is possible to be flexible in the assignment of axis selections or
direction keys of machine axis numbers.
Better support is now provided by the MSTT blocks for use of two MCPs, which are operated
simultaneously, in particular for an application using two channels and two mode groups.
The module call for the 2nd machine control panel in OB1 cycle must come after the call of
the 1st Note that the axis-numbers are also specified in the parameterized mode group
number of the MCP block in the axis tables of the relevant MCP.
For this flexibility there are tables for axis numbers in DB 10.
For 1. Machine control panel (MCP) the table starts from the byte 8
(symbolic name: MCP1AxisTbl[1..22]) and
for 2. Machine control panel (MCP) starts from the byte 32
(symbolic name: MCP2AxisTbl[1..22]) for the second MCP. The machine axis numbers must
be entered byte by byte here.
It is permissible to enter a value of 0 in the axis table. Checks are not made to find
impermissible axis numbers, meaning that false entries can lead to a PLC Stop.
The restriction of the possible axis selections in FC 25 is done via the 0-values in the axis
table. The axis numbers can also be adapted dynamically. Axis numbers may not be
switched over while the axes are being traversed via the relevant direction keys.
The compatibility mode is preset with axis numbers 1 to 4 for both MCPs and the restriction
for the configured number of axes.
Note
For supplementary information see functions description of FC 19.
Summary of Contents for SINUMERIK 840D sl
Page 282: ...Index Basic logic functions Acceleration B2 64 Function Manual 11 2006 6FC5397 0BP10 2BA0 ...
Page 388: ...Basic logic functions Travel to fixed stop F1 Function Manual 11 2006 6FC5397 0BP10 2BA0 52 ...
Page 962: ...Index Basic logic functions Emergency Stop N2 20 Function Manual 11 2006 6FC5397 0BP10 2BA0 ...
Page 1704: ...Constraints Basic logic functions Spindles S1 94 Function Manual 11 2006 6FC5397 0BP10 2BA0 ...
Page 1716: ...Index Basic logic functions Spindles S1 106 Function Manual 11 2006 6FC5397 0BP10 2BA0 ...
Page 1996: ...Index Basic logic functions Tool Offset W1 208 Function Manual 11 2006 6FC5397 0BP10 2BA0 ...
Page 2150: ...Table of contents Basic logic functions Appendix 4 Function Manual 11 2006 6FC5397 0BP10 2BA0 ...
Page 2184: ...Glossary Basic logic functions Appendix 38 Function Manual 11 2006 6FC5397 0BP10 2BA0 ...