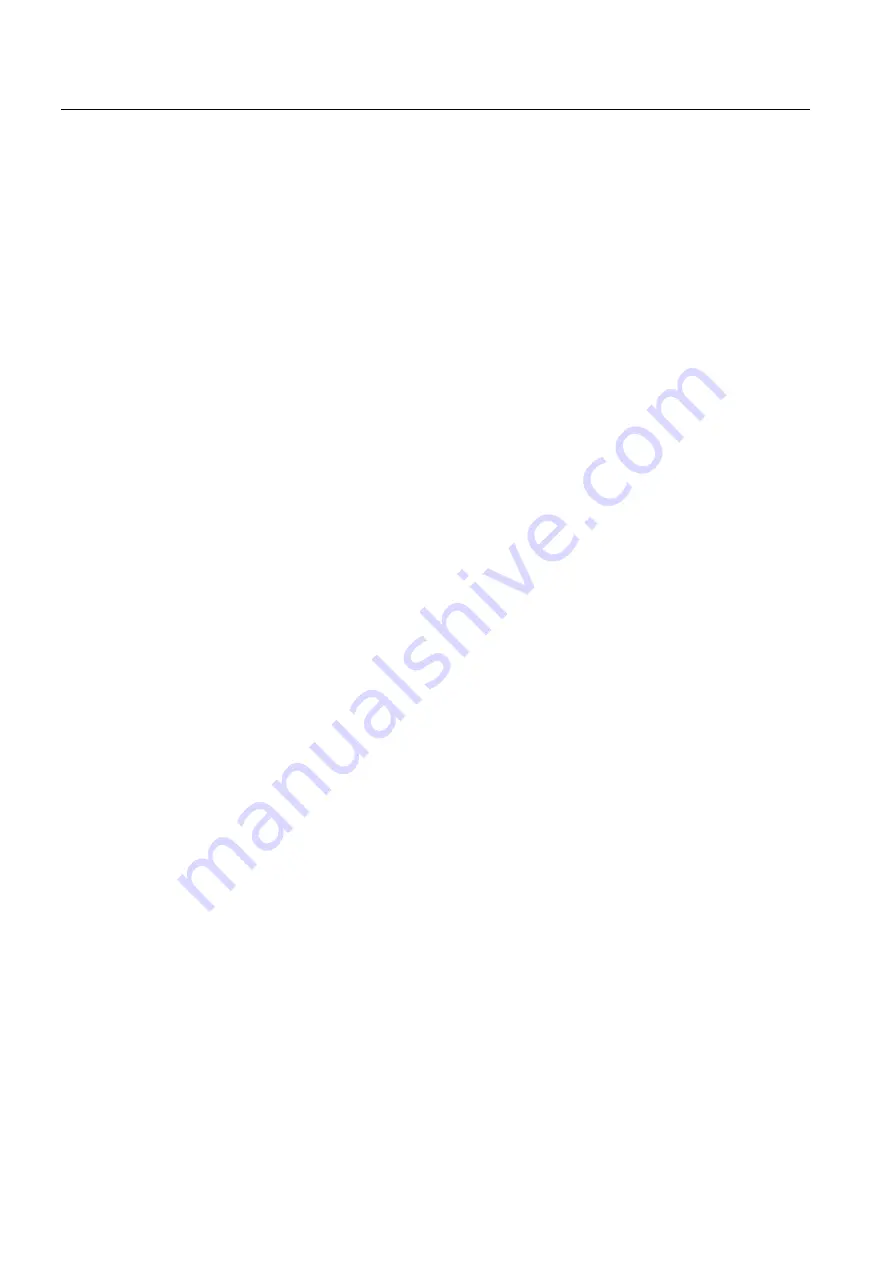
Detailed Description
2.5 Toolholder with orientation capability
Basic logic functions: Tool Offset (W1)
124
Function Manual, 11/2006, 6FC5397-0BP10-2BA0
Toolholder kinematics
The following supplementary conditions must be met for toolholder kinematics:
•
Tool orientation in initial state, both angles α
1
and α
2
zero, as per default setting, even if:
–
G17
parallel to Z
–
G18
Parallel to Y
–
G19
parallel to Z
•
A permissible position in terms of the axis limits must be achievable.
•
For any possible orientation to be set, the two rotary axes must be perpendicular to each
other.
For machines, on which the table is rotated by both axes, the tool orientation must also
be perpendicular to the first rotary axis.
For machines with mixed kinematics, the tool orientation must be perpendicular to the
axis, which rotates the tool, i.e., also the first rotary axis.
The following applies to orientations specified in a frame:
•
The orientation specified in a frame must be achievable with the defined toolholder
kinematics, otherwise an alarm is output.
This situation can occur if the two rotary axes required to define the kinematics are not
perpendicular to each other.
This applies if fewer than two rotary axes are defined and is the case:
–
With kinematic type T with rotary tool, if the tool axis, which defines the tool direction,
is not perpendicular to the second axis.
–
With kinematic types M and P with rotary workpiece, if the tool axis, which defines the
tool direction, is not perpendicular to the first axis.
•
Rotary axes, which require a frame with a defined tool orientation in order to reach a
specific position, are only determined unambiguously in the case of one rotary axis. Two
general solutions exist for two rotary axes.
•
In all cases where ambiguities may arise, it is particularly important that the approximate
angles expected from the frame are stored in the tool data, and that the rotary axes are in
the vicinity of the expected positions.
Response with ASUP, REPOS
The toolholder can be changed in an asynchronous subprogram (ASUB). When the
interrupted program is resumed with
REPOS
, the approach motion of the new toolholder is
taken into account and the program continues with this motion. The treatment here is
analogous to tool change in an ASUB.
References:
/FB1/ Function Manual Basic Functions; Mode Group, Channel, Program Operation, Reset
Response (K1)
Summary of Contents for SINUMERIK 840D sl
Page 282: ...Index Basic logic functions Acceleration B2 64 Function Manual 11 2006 6FC5397 0BP10 2BA0 ...
Page 388: ...Basic logic functions Travel to fixed stop F1 Function Manual 11 2006 6FC5397 0BP10 2BA0 52 ...
Page 962: ...Index Basic logic functions Emergency Stop N2 20 Function Manual 11 2006 6FC5397 0BP10 2BA0 ...
Page 1704: ...Constraints Basic logic functions Spindles S1 94 Function Manual 11 2006 6FC5397 0BP10 2BA0 ...
Page 1716: ...Index Basic logic functions Spindles S1 106 Function Manual 11 2006 6FC5397 0BP10 2BA0 ...
Page 1996: ...Index Basic logic functions Tool Offset W1 208 Function Manual 11 2006 6FC5397 0BP10 2BA0 ...
Page 2150: ...Table of contents Basic logic functions Appendix 4 Function Manual 11 2006 6FC5397 0BP10 2BA0 ...
Page 2184: ...Glossary Basic logic functions Appendix 38 Function Manual 11 2006 6FC5397 0BP10 2BA0 ...