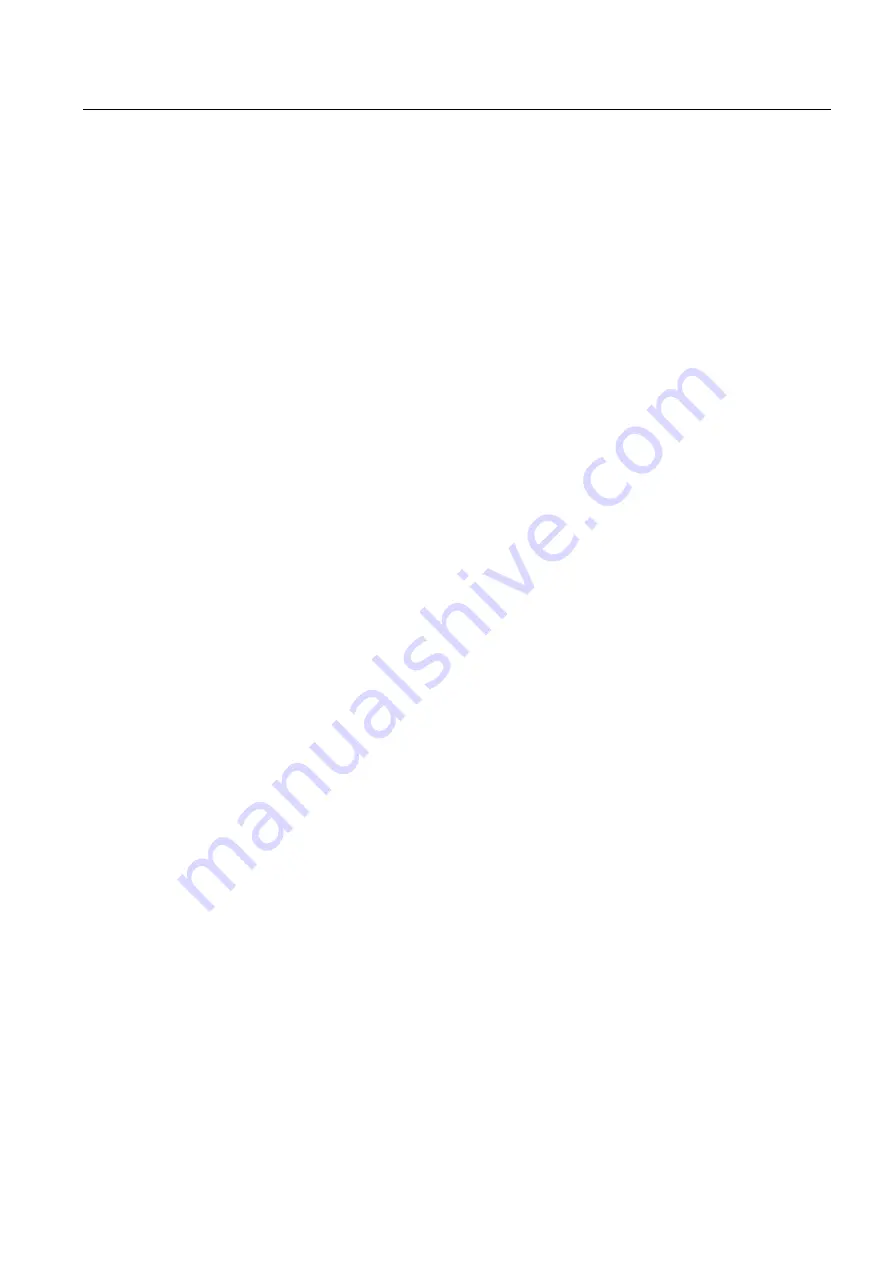
Detailed description
2.6 Interface structure
Basic logic functions: PLC Basic program powerline (P3 pl)
Function Manual, 11/2006, 6FC5397-0BP10-2BA0
43
Machine operation
All operator inputs, which lead to response actions on the machine, are monitored by the
PLC. Operator actions are usually performed on the machine control panel. However, it is
also possible to perform some operator actions from the operator interface (e.g. mode
selection, INC mode selection).
The PLC operating system enters the operating signals sent by the HMI directly into the
interface data blocks. In standard cases, the basic program, which decodes the operating
signals, allows the operator actions to be performed on the operator interface or on the MCP
- given that the capability for this type of operator action is available on the MCP. If required,
the user can switch off operation via HMI via an FB1 parameter "MMCToIF".
PLC messages
The signaling functions are based on the system diagnostic functions integrated in the
operating system of the AS 300. These have the following characteristics:
•
The PLC operating system enters all important system states and state transitions in a
diagnostics status list. Communication events and I/O module diagnostics data (for
modules with diagnostic functions) are also entered.
•
Diagnostics events, which lead to a system stop, are also entered with a time stamp in a
diagnostic buffer (circular buffer) in the chronological order of their occurrence.
•
The events entered in the diagnostic buffer are automatically transmitted to
human machine interface systems via the MPI or via the OPI through the COM module,
once these have issued a ready signal (message service). Transfer to the node ready is a
function of the PLC operating system. Receipt and interpretation of the messages are
executed by the HMI software.
•
An SFC (system function call) can also be used by the user program to enter messages
in the diagnostic buffer.
•
The events are entered in the diagnostic buffer in coded format.
The associated message texts must be stored in the operator panel.
An FC for message acquisition (FC10) is prepared in conjunction with the basic program.
This FB records events, classifies them into signal groups and reports them to the HMI via
the diagnostic buffer.
The message acquisition structure is shown in the figure "Acquisition and signaling of PLC
events".
The features include:
•
Bit fields for events related to the VDI interface are combined in a single data block (DB2)
with bit fields for user messages.
•
Bit fields are evaluated at several levels by FC10.
–
Evaluation 1; Acquisition of group signals
A group signal is generated for each group of signals when at least one bit signal is
set to "1". This signal is generally linked to the disable signal of the VDI interface (on
modules with diagnostic functions). The group signals are acquired completely in
cycles.
Summary of Contents for SINUMERIK 840D sl
Page 282: ...Index Basic logic functions Acceleration B2 64 Function Manual 11 2006 6FC5397 0BP10 2BA0 ...
Page 388: ...Basic logic functions Travel to fixed stop F1 Function Manual 11 2006 6FC5397 0BP10 2BA0 52 ...
Page 962: ...Index Basic logic functions Emergency Stop N2 20 Function Manual 11 2006 6FC5397 0BP10 2BA0 ...
Page 1704: ...Constraints Basic logic functions Spindles S1 94 Function Manual 11 2006 6FC5397 0BP10 2BA0 ...
Page 1716: ...Index Basic logic functions Spindles S1 106 Function Manual 11 2006 6FC5397 0BP10 2BA0 ...
Page 1996: ...Index Basic logic functions Tool Offset W1 208 Function Manual 11 2006 6FC5397 0BP10 2BA0 ...
Page 2150: ...Table of contents Basic logic functions Appendix 4 Function Manual 11 2006 6FC5397 0BP10 2BA0 ...
Page 2184: ...Glossary Basic logic functions Appendix 38 Function Manual 11 2006 6FC5397 0BP10 2BA0 ...