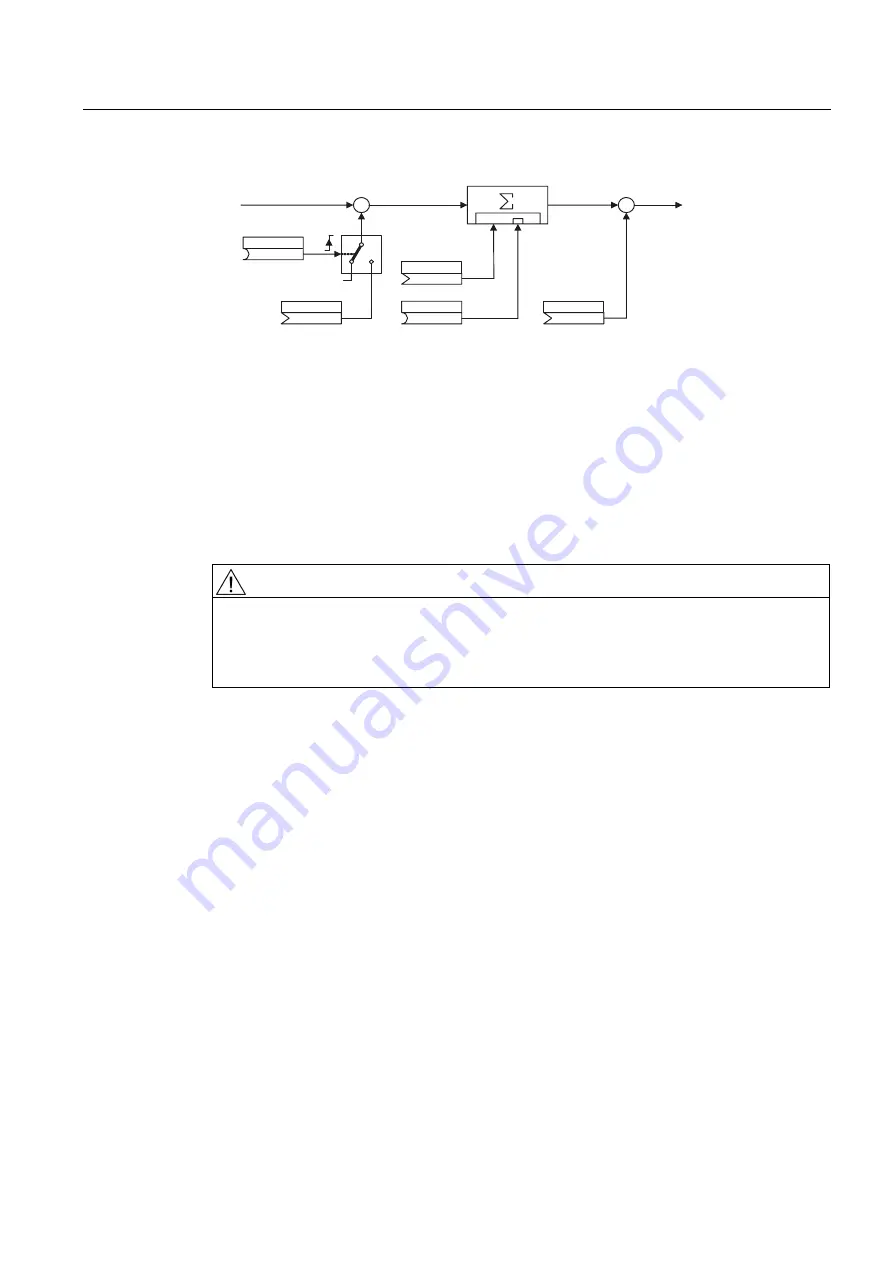
Functions, monitoring, and protective functions
9.4 Extended functions
Drive converter cabinet units
Operating Instructions, 07/07, A5E00288214A
355
( 0 )
p 2516
+
+
( 0 )
p 2515
+
+
1
0
p 2512
( 0 )
0
p 2514
( 0 )
( 0 )
p 2513
LU
DFWBYDOBFRQGFRUU
DFWBYDOBFRQGDFW
VBDFWVHWDFW
VBDFWVHWVHWYDO
3RVLWLRQRIIVHW
$FWXDOSRVLWLRQYDOXH
VBDFW
Figure 9-16 Actual position value preparation
An offset can be undertaken using connector input p2513 (actual position value preparation
offset) and a positive edge at the binector input p2512 (activate offset). When the "basic
positioner" function module is activated, p2513 is automatically connected with r2685 (EPOS
offset) and p2515 with r2684.7 (activate offset). This interconnection enables modulo offset
by EPOS, for example.
p2516 can be used to switch in position offset. Using EPOS, p2516 is automatically
interconnected to r2667. Backlash compensation is implemented using this interconnection.
Using the connector input p2515 (position setting value) and a "1" signal at binector input
p2514 (set position actual value), a position setting value can be entered.
WARNING
When the actual position value is set (p2514 = "1" signal), the actual position value of the
position controller is kept at the value of connector p2515 as standard.
Incoming encoder increments are not evaluated. A difference in position cannot be
compensated for in this situation.
An inversion of the actual position value resulting from the encoder is undertaken using
parameter p0410. An inversion of the axis motion can be entered using a negative value in
p2505.
Load gearbox position tracking
Position tracking for load gearbox functions in the same way as position tracking for the
measuring gearbox (see "Position tracking/Measuring gearbox"). Position tracking is
activated via parameter p2720.0 = 1. The position tracking of the load gearbox, however, is
only relevant for the motor encoder (encoder 1). The load gearbox ratio is entered via
parameters p2504 and p2505. Position tracking can be activated with rotary axes (modulo).
Position tracking for the load gearing can only be activated once for each motor data set
MDS.
The load position actual value in r2723 (must be requested via GnSTW.13) is limited to 232
digits. When position tracking (p2720.0 = 1) is switched on, the load position actual value
(r2723) comprises the following position information:
●
Encoder pulses per revolution (p0408)