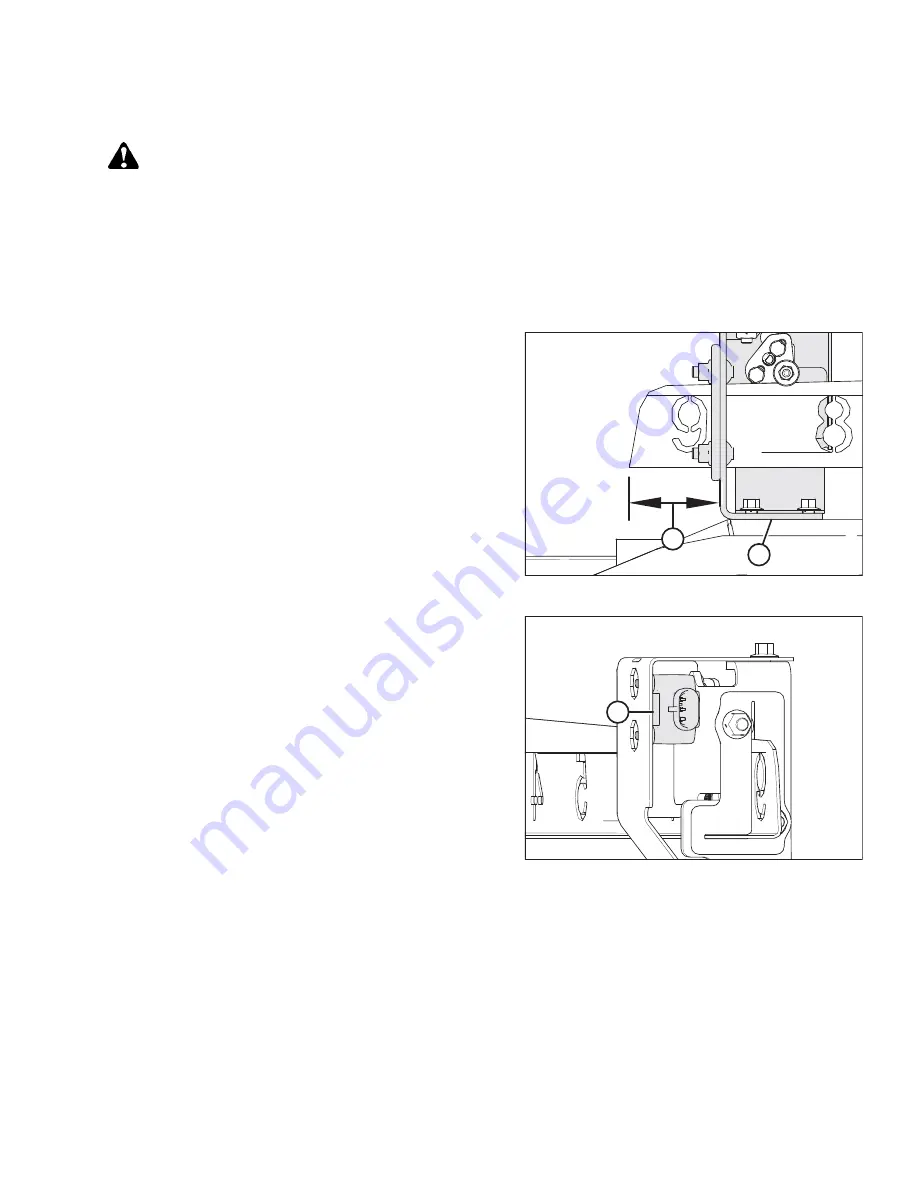
MAC215990
151
Revision A
Checking and adjusting sensor output voltage
DANGER
Ensure that all bystanders have cleared the area.
4.
Engage the parking brake.
IMPORTANT:
To measure the output voltage of the fore-aft sensor, the engine needs to be running and supplying power to the
sensor.
5.
Start the engine.
1032692
A
B
Figure 3.169: Fore-Aft Bracket
6.
Adjust the reel to the fully forward position. Ensure that
dimension (B) (from the sensor bracket to the end of the
indicator) is 62
–
72 mm (2.4
–
2.8 in.).
1032694
A
1
2
3
Figure 3.170: Fore-Aft Sensor
7.
Use the combine display or a voltmeter (if measuring the
sensor manually) to measure the voltage range. If using a
voltmeter, check sensor voltage (A) between pin 2 (ground)
and pin 3 (signal).
•
For Case and New Holland combines, the voltage range
should be 0.7
–
1.1 V
8.
Shut down the engine, and remove the key from
the ignition.