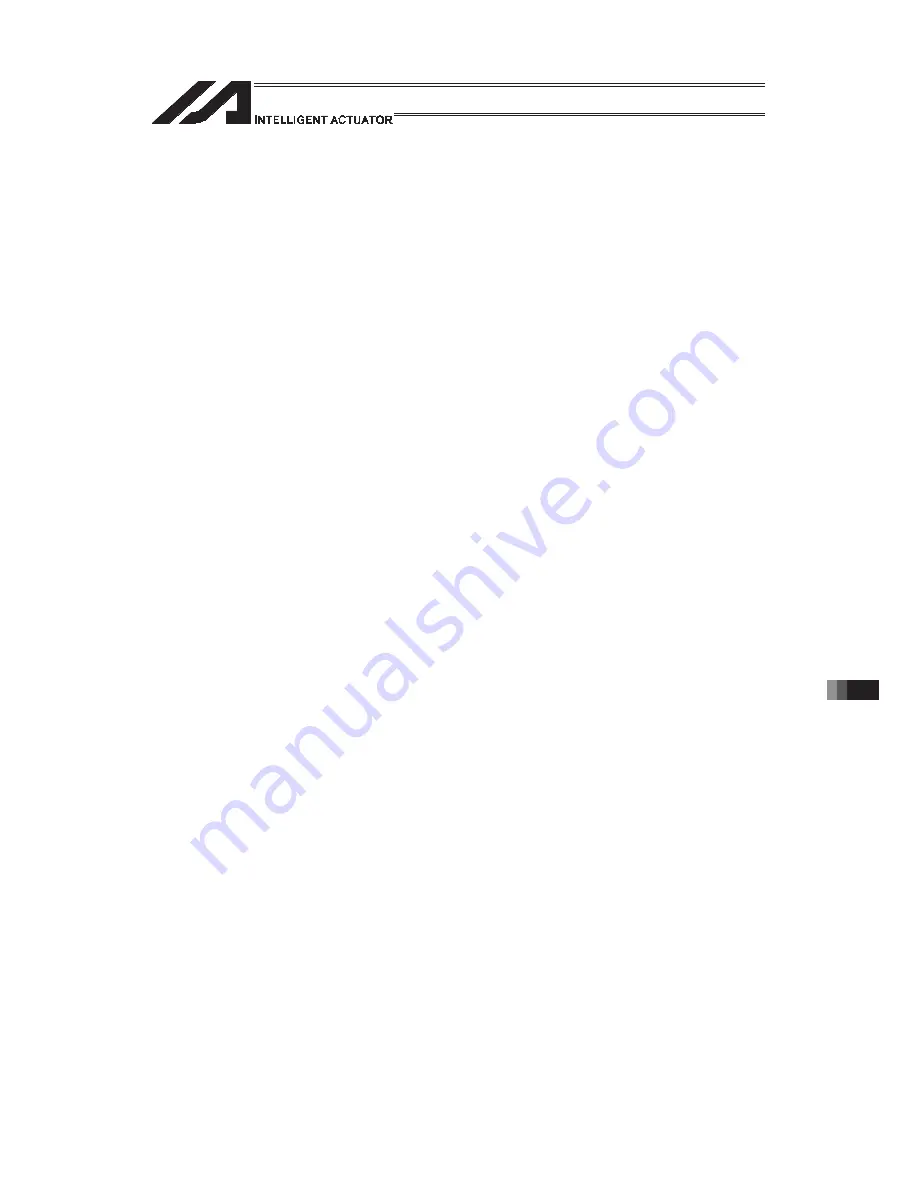
[25] Extended Command
471
(Note 6)
“Error No. C6B: Deviation overflow error” or “Error No. CA5: Stop deviation
overflow error” may be detected before “Error No. 420: Steady-state (non-push)
torque limit over error”. This is normal.
(Note 7)
If the torque is changed to a high level from a low level at which axis movement
can no longer be guaranteed, be sure to issue a STOP command to low-torque
axes and clear the deviation counter before increasing the torque (from a low
level). If the torque setting is changed from low to high when deviations are still
accumulated, the axes may move without their speed being limited and thus a
dangerous situation may occur.
(Note 8)
To return to the normal condition (maximum torque), expressly specify 1000% for
the “steady-state (non-push) torque limit (upper limit)” and 20000msec for the
“steady-state (non-push) torque limit over detection time”.
* If a value greater than the upper limit specific to each axis is set for the
“steady-state (non-push) torque limit (upper limit)” of that axis, the upper limit
specific to the axis (approx. 200 to 400%) is set.
(Note 9)
The following values are used upon power ON reset, software reset and start of
home return:
Steady-state (non-push) torque limit (upper limit) = Driver card parameter No. 40,
“Maximum toque limit (%)”
Steady-state (non-push) torque limit over detection time = 20000msec
(Note 10)
If the “steady-state (non-push) torque limit (upper limit)” and “steady-state
(non-push) torque limit over detection time” are changed, the new settings will
remain effective even after the SEL program ends. When building a system using
this extended command, therefore, expressly set the “steady-state (non-push)
torque limit (upper limit)” and “steady-state (non-push) torque limit over detection
time” in all SEL programs, before any operation is started in each program, using
this extended command. If you assume that the “steady-state (non-push) torque
limit (upper limit)” and “steady-state (non-push) torque limit over detection time”
will be reset after the end of operation in other programs, unexpected settings of
“steady-state (non-push) torque limit (upper limit)” and “steady-state (non-push)
torque limit over detection time” may be applied should the program abort due to
an error, etc., in which case unforeseen problems may result.
(Note 11)
This extended command does not rewrite the value of driver card parameter No.
40, “maximum torque limit” itself (main CPU flash memory) (in non-volatile
memory).
Summary of Contents for PSEL
Page 2: ......
Page 10: ......
Page 18: ...8 Part 1 Installation ...
Page 37: ...27 Part 1 Installation 2 2 axis specification with battery ...
Page 382: ...372 Appendix Micro cylinder RCL Series Current limiting value ratio Push force N ...
Page 476: ...466 Appendix ...
Page 480: ...470 ...
Page 485: ...475 ...
Page 487: ...INTELLIGENT ACTUATOR SEL Language Programming Manual Eighth Edition ...
Page 488: ......
Page 490: ......
Page 494: ......
Page 518: ...24 ...
Page 526: ...32 ...
Page 831: ... 11 Actuator Control Declaration 337 Example DFIF 1 170 ...
Page 1060: ......
Page 1061: ......