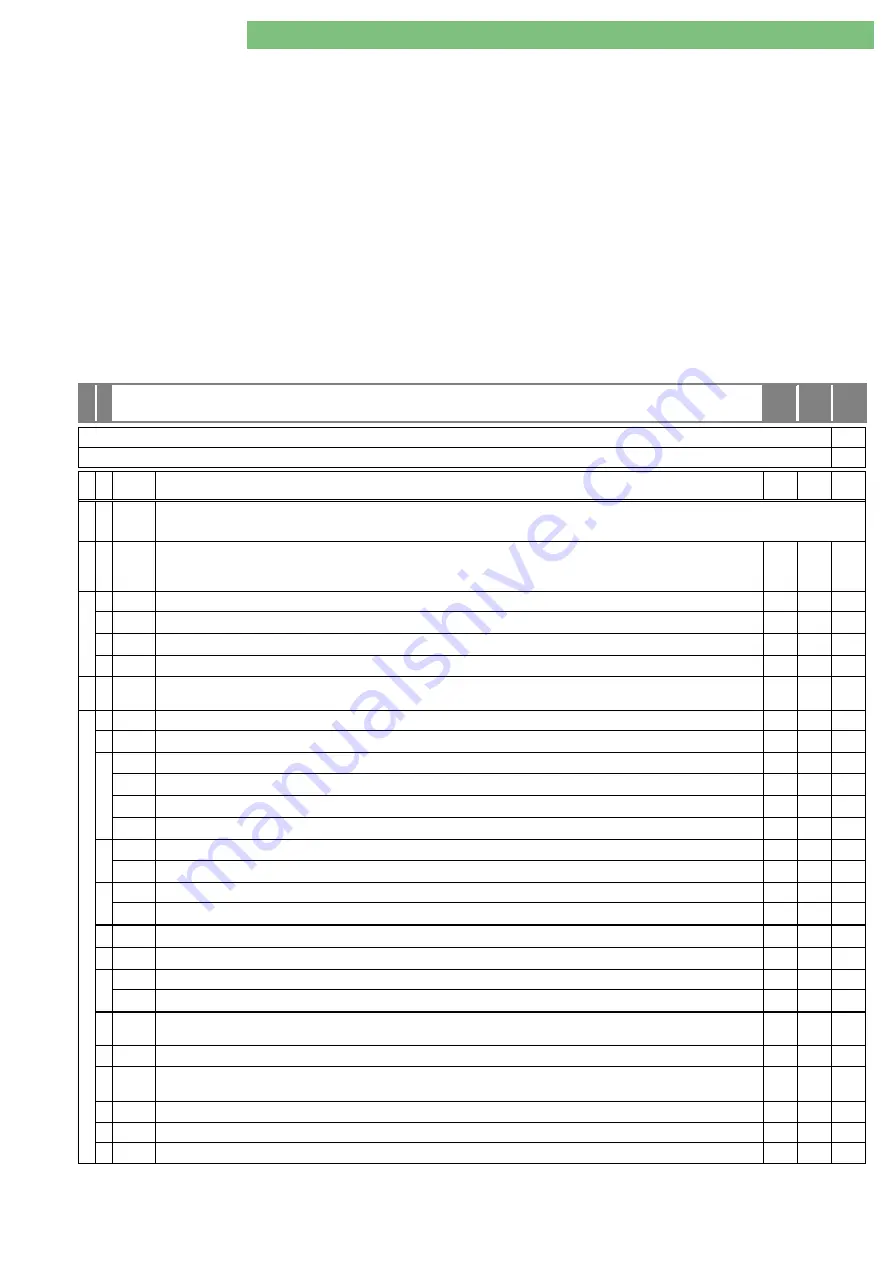
5. Technical Safety Inspection and Preventive Maintenance
1 / 2 0 1 0
5 - 3
BA-TE-DE08C M.KAY
SW9xx_SM_Chapter 5-1_1-2010.doc/pdf <110301> yymmdd
B. Braun Avitum AG
Dialog
+
SW 9.xx
5.1 Check List for Technical Safety Inspection
and Preventive Maintenance
For
SW 9.xx
The technical safety inspection shall be performed and documented every 12 months, according to
the specified check list and with reference to the service manual and instructions for use.
The preventive maintenance is recommended every 12 months, according to the specified check
list and with reference to the service manual and instructions for use and shall be documented.
REF {Type/Typ}: ........................................
SN {Serien-No./Nr.}: .................................................
Year of Purchase: ................... Responsible Organisation (User): .................................................
..................................................................................................................................................................
Operating Hours: ................................... h Inventory No.: ..............................................................
SW Version: ...............................................
Manufacturer:
B. Braun Avitum AG
34209 Melsungen, Germany
S M
Check List (S = Technical Safety Inspection Points; M = Preventive Maintenance Points)
Note:
Text in { } brackets is information for the execution of the check list!
NO YES OK
Technical Safety Inspection
Technical Safety Inspection with Preventive Maintenance
M
1.
Disinfection/decalcification was performed
2.
Visual Inspection with Maintenance Procedures
S
2.1
Visual Inspection
{Machine: clean/complete; no damages/moisture influences (protection covers) or loose assemblies; no moveable parts
touching tubings or wires; casters are moveable; type plate legible}
M
2.2
Clean interior space and exterior surfaces
M
2.3
Suction tubing for disinfection and concentrate exchanged
M
2.4
O-rings at suction rod exchanged
M
2.5
Balance chamber – no visible leakages
S
2.6
Check tight seat and damages of mains supply (power supply cord, strain relief), potential equalisation cable, staff call/data
lines (if present) and connectors
M
2.7
Tubing connectors , clamps and couplings (internal/external) are assembled correctly
M
2.8
Membranes, o-rings and tubings at the dialyser couplings exchanged
M
2.9
HDF Online
Option present
2.9.1
O-rings {12.37 x 2.62} and membranes {for HDF filter with couplings} exchanged
2.9.2
Hydrophobic filter HFB exchanged
2.9.3
Filter FSU {between PSABF and VSAA} exchanged
M
2.10
DF Filter
Option present
2.10.1 Membranes exchanged
M
2.11
Tight seat of boards and connectors (incl. mains connection in switch mode power supply)
2.12
Exchange dust filter of fan (rear door)
M
2.13
Filter (FVD, FB, FK, FBK1/2, FBIC, FEP) exchanged
M
2.14
Filter level regulation module (HFA, HFV, HFE (HFS if present)) exchanged
M
2.15
BIC Cartridge Holder
Option present
2.15.1 O-rings exchanged
M
2.16
Battery on PC motherboard exchanged (after operating period of 4 years)
{Battery is not included in the maintenance kit, if necessary order separately.}
M
2.17
Monitor: no restriction of motion of rotation; touch membrane/keyboard membrane not damaged
M
2.18
Check non-return valve RVDA (400 mbar
±
50 mbar or 300 mmHg
±
37 mmHg) and set if necessary
(for HDF Online: 500 mbar
±
50 mbar or 375 mmHg
±
37 mmHg)
M
2.19
Check non-return valve DDE (400 mbar
±
50 mbar or 300 mmHg
±
37 mmHg) and set if necessary
M
2.20
Check non-return valve RVFPE (1,300 mbar
±
50 mbar or 975 mmHg
±
37 mmHg) and set if necessary
M
2.21
Check non-return valve RVFPA (1,300 mbar
±
50 mbar or 975 mmHg
±
37 mmHg) and set if necessary