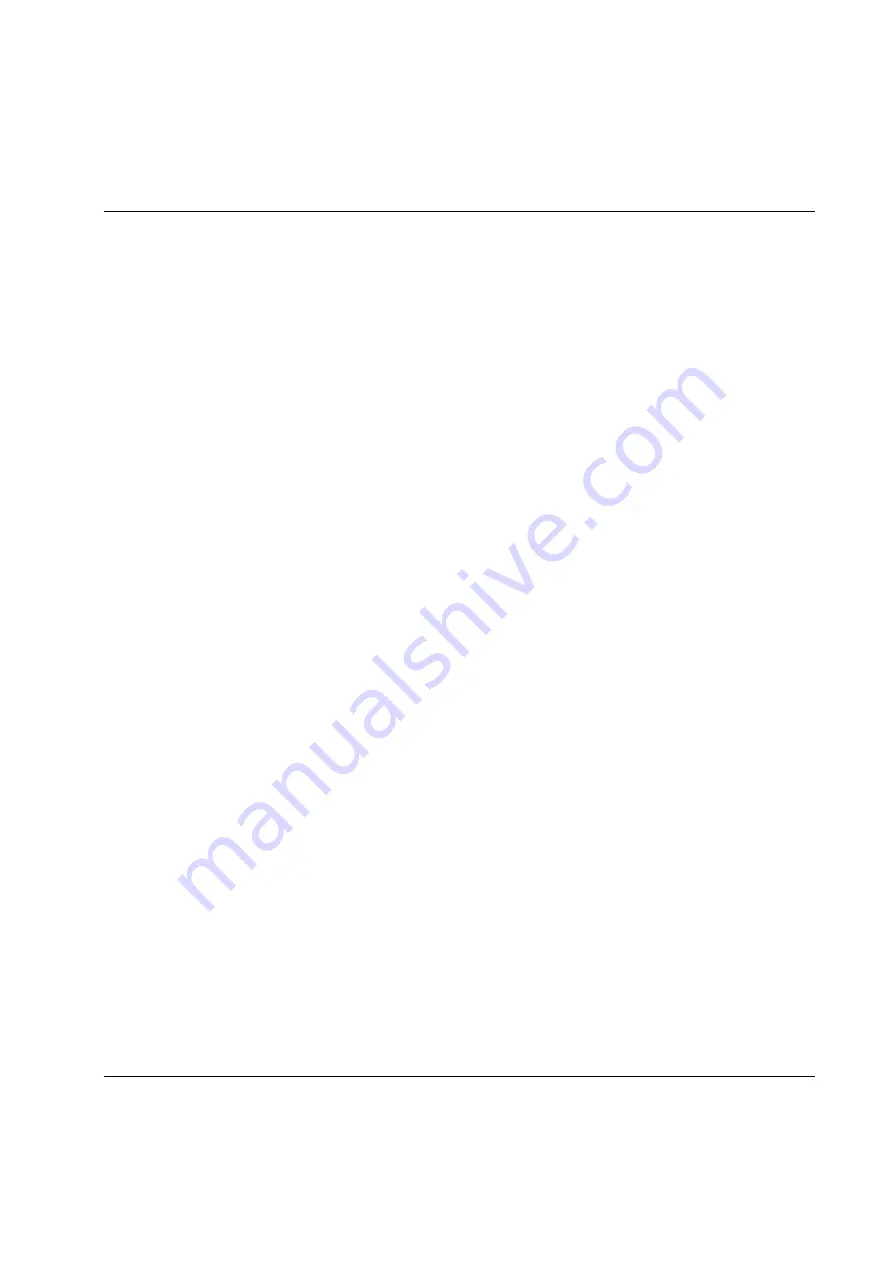
Tightening
9836 3521 01
271
Include 2
nd
Angle:
Check this to include the second angle channel in the trace if equipped
(takes more memory).
Monitoring Settings
Stop monitoring when NOK:
Check this checkbox to have the monitoring function stop
recording data whenever a step is found NOK when evaluated. This, together with the step
control parameter
Start/restart monitoring
(see chapter: Step
– Control), is used to select
which parts of the cycle that is evaluated by he monitoring checks set up using the Cycle End
step(s). See also chapter: Bolt Monitoring.
Use 2
nd
monitoring buffer:
Check this checkbox to enable the second monitoring buffer. The
buffer will use the same settings as the monitoring buffer. Only Final torque and Threshold
angle checks are run and reported for the second buffer. See also chapter: Bolt Monitoring.
Monitoring Start and Monitoring End:
Are used to specify the condition when monitoring
function should be started and stopped.
Auto scale Mon Buffer:
If Auto scale is checked then the buffer is automatically rescaled if the
traveled angle exceeds the maximum angle of the buffer. When started every element covers 1
encoder increment and whenever the buffer limit is reached this value is doubled causing a
lower resolution. Already recorded data is kept (compressed) when the buffer is rescaled. If
you leave Auto scale unchecked you must manually enter the resolution of the buffer in the edit
field to the right of it. In this case the oldest recorded data will be overwritten when buffer limit
is reached resulting in that the last part of the cycle is kept in the buffer. When using a fix buffer
the checkbox
Allow monitoring buffer overrun
controls whether or not a buffer overrun
should be regarded as an error or not. If checked then an overrun will generate an event and
cause the cycle to end NOK. If not checked then only a warning is generated.
Limits
Report threshold torque limit:
Each bolt for which the highest measured torque does not
exceeds the
Report threshold torque limit
will have the "Warnings" bit REPLIMIT (REPort
LIMIT) set.
The highest measured torque is defined as the highest value of the two result variables “Bolt
Max T” and “Bolt Min T”. If “Bolt Min T” is negative the absolute value of “Bolt Min T” is used
instead, that is,. the warning bit is set if
Report threshold torque limit > MAX (ABS (Max T),
ABS (Min T))
.
If none of the bolts executed for a cycle (disconnected bolts excluded) exceeded the value of
the
Report threshold torque limit
parameter then the corresponding cycle data will be
automatically dropped.
Normally this parameter is used to avoid reporting tightening made "in the air". Leave the
parameter empty to disable the function.
Remove fastener torque limit:
This is a "program global" restriction, that is, a restriction that
is checked over all steps executed in the cycle. When the measured torque exceeds the
entered value the current step is immediately stopped.
Summary of Contents for PowerMACS 4000
Page 2: ......
Page 46: ...System Architecture 46 9836 3521 01...
Page 267: ...Tightening 9836 3521 01 267...
Page 400: ...Tightening 400 9836 3521 01...
Page 486: ...Peripheral Devices 486 9836 3521 01...
Page 622: ...Peripheral Devices 622 9836 3521 01...
Page 664: ...References 664 9836 3521 01...
Page 668: ...9836 3521 01 2010 11 Edition 10 3 0 www atlascopco com...