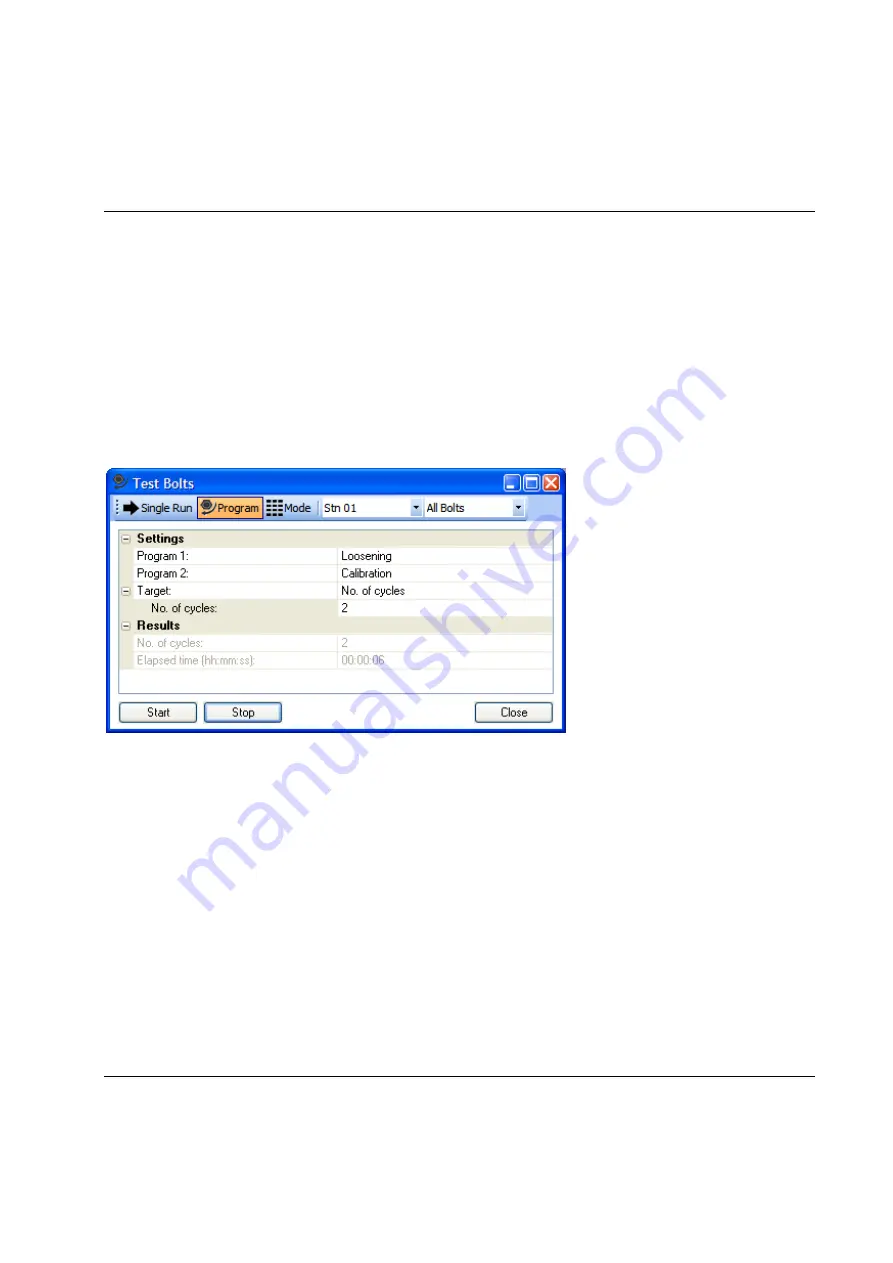
Set Up and Maintenance
192
9836 3521 01
Program
You can either use an existing program or you can create a special tightening program called
“Calibration”. The tightening program shall have the following structure:
Step 1:
“Diagnostic” step with spindle functional test enabled and
Spindle Only
selected as zero
offset compensation.
Step 2: Tightening step, e.g. torque xx Nm; speed yy rpm
Step 3: CE
It is practical to also create a loosening program to be used to loosen the tightened joint.
In the picture below is it defined one tightening and one loosening program.
With number of cycles set to the value 2, a loosening will first be done followed by a tightening.
Mode
Using the Mode option is similar to the Program one. The difference is that in the Mode option it is
possible to run different tightening programs for different spindles. As we normally recommend that you
shall only run one spindle at a time when you make a calibration is the mode alternative probably not a
real option.
4.17.3.2 Torque
All Atlas Copco torque transducers are factory calibrated to a sensitivity /-0.3% of the nominal
torque. Due to component tolerances in the TC electronics a fine tune of the torque sensor is
recommended. Exchange of a torque transducer to an identical unit does not require a new calibration, but
for quality control reasons it is anyway normally done.
An inline slip-ring torque transducer and a peak hold monitoring amplifier shall be used for the torque
measurement, e.g. Atlas Copco IRTT transducer with ACTA.
Summary of Contents for PowerMACS 4000
Page 2: ......
Page 46: ...System Architecture 46 9836 3521 01...
Page 267: ...Tightening 9836 3521 01 267...
Page 400: ...Tightening 400 9836 3521 01...
Page 486: ...Peripheral Devices 486 9836 3521 01...
Page 622: ...Peripheral Devices 622 9836 3521 01...
Page 664: ...References 664 9836 3521 01...
Page 668: ...9836 3521 01 2010 11 Edition 10 3 0 www atlascopco com...