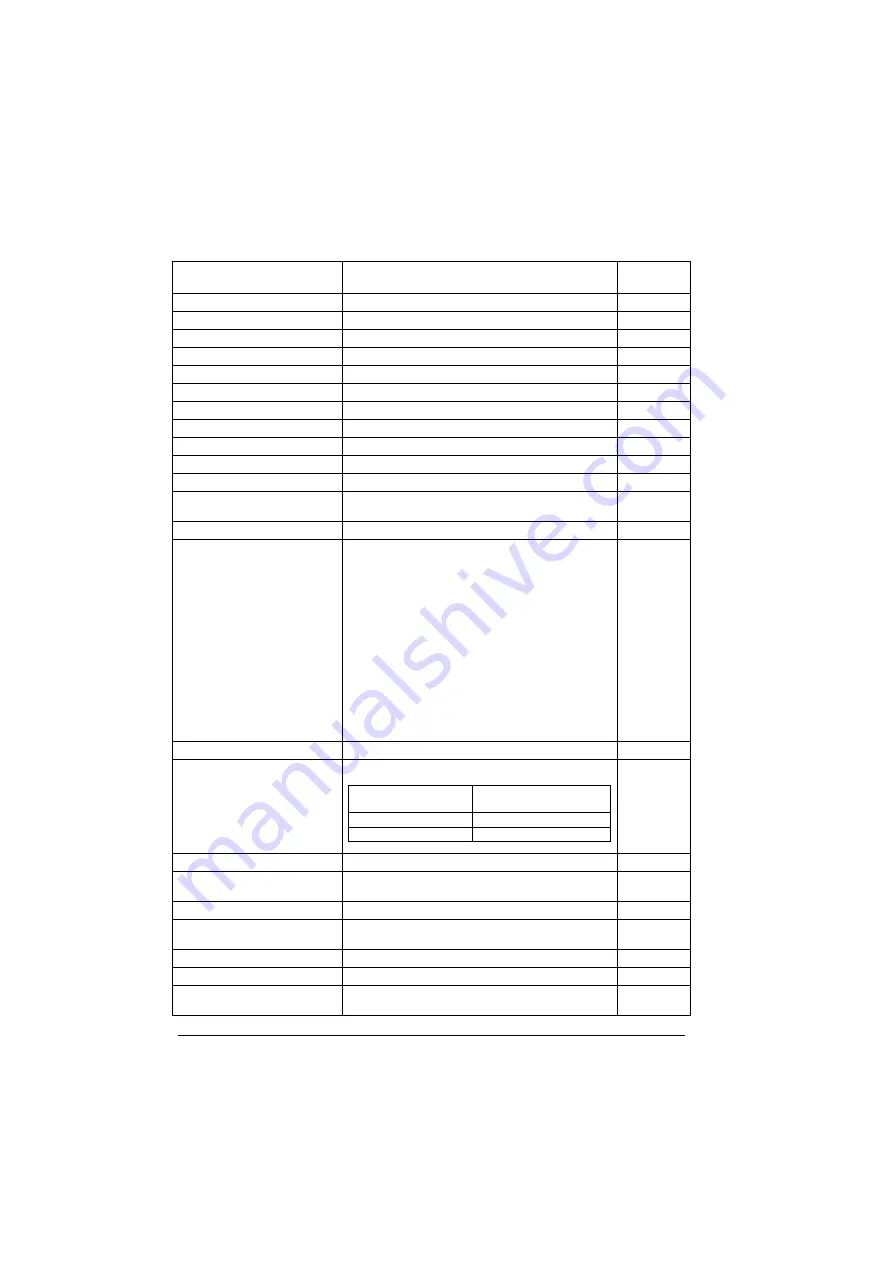
226 Parameters
In1+In2
Sum of sources 1 and 2.
1
In1-In2
Source 2 subtracted from source 1.
2
In1*In2
Source 1 multiplied by source 2.
3
In1/In2
Source 1 divided by source 2.
4
MIN(In1,In2)
Smaller of the two sources.
5
MAX(In1,In2)
Greater of the two sources.
6
AVE(In1,In2)
Average of the two sources.
7
sqrt(In1)
Square root of source 1.
8
sqrt(In1-In2)
Square root of (source 1 - source 2).
9
sqrt(In1+In2)
Square root of (source 1 + source 2).
10
sqrt(In1)+sqrt(In2)
Square root of source 1 + square root of source 2.
11
Defines the filter time constant for process feedback. 0.000 s
0.000…30.000 s
Feedback filter time.
1 = 1 s
Defines, together with parameter
, a general scaling factor for the process PID
control chain.
The scaling can be utilized when, for example, the
process setpoint is input in Hz, and the output of the
PID controller is used as an rpm value in speed
control. In this case, this parameter might be set to
to the nominal motor speed
at 50 Hz.
In effect, the output of the PID controller = [
]
when
deviation (setpoint - feedback) = [
] and [
] =
1.
Note:
The scaling is based on the ratio between
and
. For example, the values 50 and 1500 would
produce the same scaling as 1 and 30.
0.00
-20000.00…200000.00 Process setpoint base.
1 = 1
See parameter
.
1500.00;
1800.00
(
b0)
-20000.00…200000.00 Process PID controller output base.
1 = 1
Selects the primary source of process PID setpoint.
See the control chain diagram on page
not used
None.
0
Internal setpoint
Internal setpoint. See parameter
2
AI1 scaled
3
AI2 scaled
4
Motor potentiometer
(output of the
motor potentiometer).
8
No.
Name/Value
Description
Default
FbEq 16
Operation mode
Scaling
Speed control
Frequency control
Summary of Contents for ACS280
Page 1: ... ABB MACHINERY DRIVES ACS280 coldplate drives Firmware manual ...
Page 4: ......
Page 10: ...10 ...
Page 16: ...16 Control panel ...
Page 20: ...20 Start up ID run and use ...
Page 24: ...24 Default control connection ...
Page 88: ...88 Program features ...
Page 298: ...298 Parameters ...