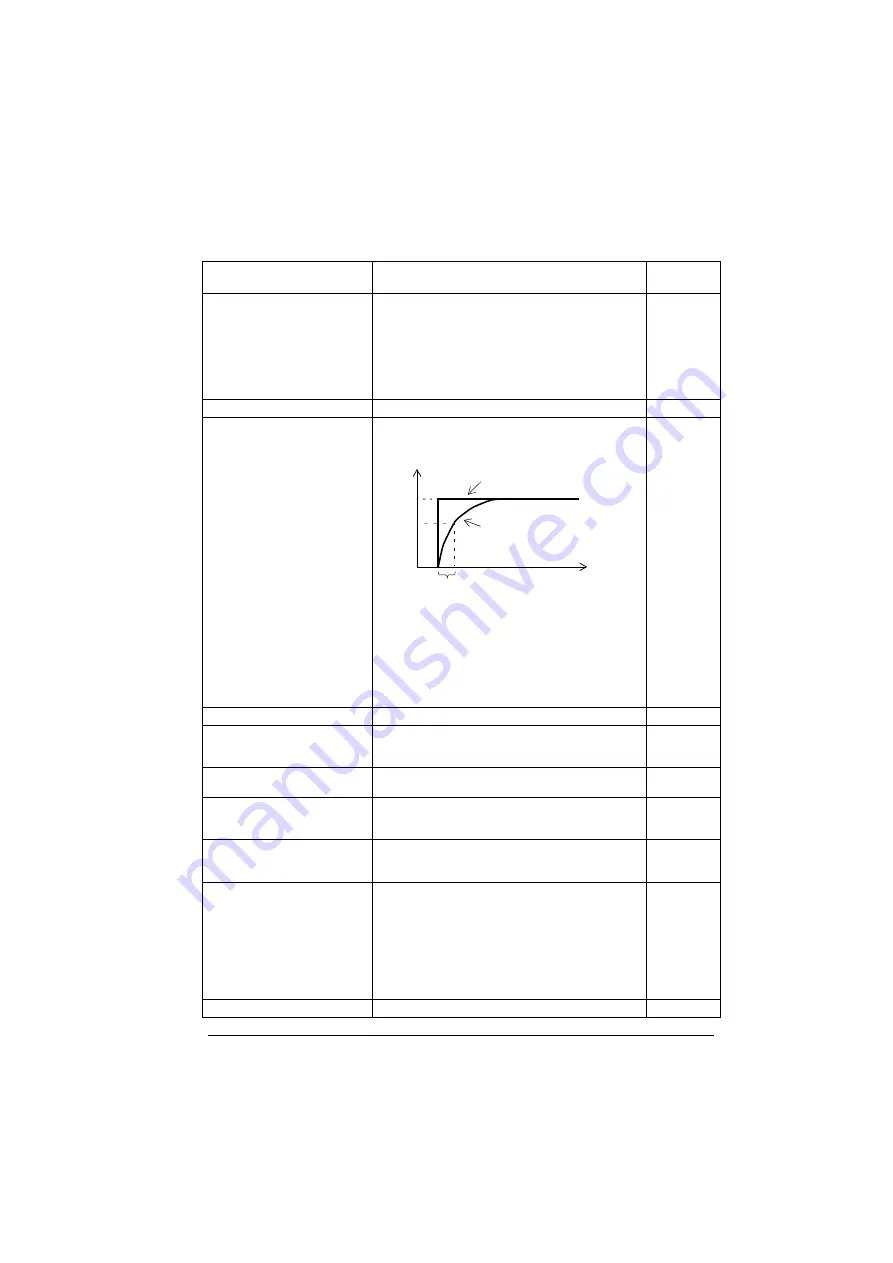
Parameters 231
Defines the derivation time of the process PID
controller. The derivative component at the controller
output is calculated on basis of two consecutive error
values (E
K-1
and E
K
) according to the following
formula:
PID DERIV TIME × (E
K
- E
K-1
)/
T
S
, in which
T
S
= 2 ms sample time
E = Error = Process reference - process feedback.
0.000 s
0.000…10.000 s
Derivation time.
1000 = 1 s
Defines the time constant of the 1-pole filter used to
smooth the derivative component of the process PID
controller.
0.0 s
0.0…10.0 s
Filter time constant.
10 = 1 s
Defines the minimum limit for the process PID
controller output. Using the minimum and maximum
limits, it is possible to restrict the operation range.
0.00
-200000.00…
200000.00
Minimum limit for process PID controller output.
1 = 1
Defines the maximum limit for the process PID
controller output. See parameter
.
100.00
-200000.00…
200000.00
Maximum limit for process PID controller output.
1 = 1
Freezes (or defines a source that can be used to
freeze) the output of the process PID controller,
keeping the output at the value it was before freeze
was enabled. This feature can be used when, for
example, a sensor providing process feedback must
to be serviced without stopping the process.
1 = Process PID controller output frozen
See also parameter
.
not used
Not used
Process PID controller output not frozen.
0
No.
Name/Value
Description
Default
FbEq 16
63
%
100
T
t
O = I × (1 - e
-t/T
)
I = filter input (step)
O = filter output
t
= time
T = filter time constant
Unfiltered signal
Filtered signal
Summary of Contents for ACS280
Page 1: ... ABB MACHINERY DRIVES ACS280 coldplate drives Firmware manual ...
Page 4: ......
Page 10: ...10 ...
Page 16: ...16 Control panel ...
Page 20: ...20 Start up ID run and use ...
Page 24: ...24 Default control connection ...
Page 88: ...88 Program features ...
Page 298: ...298 Parameters ...