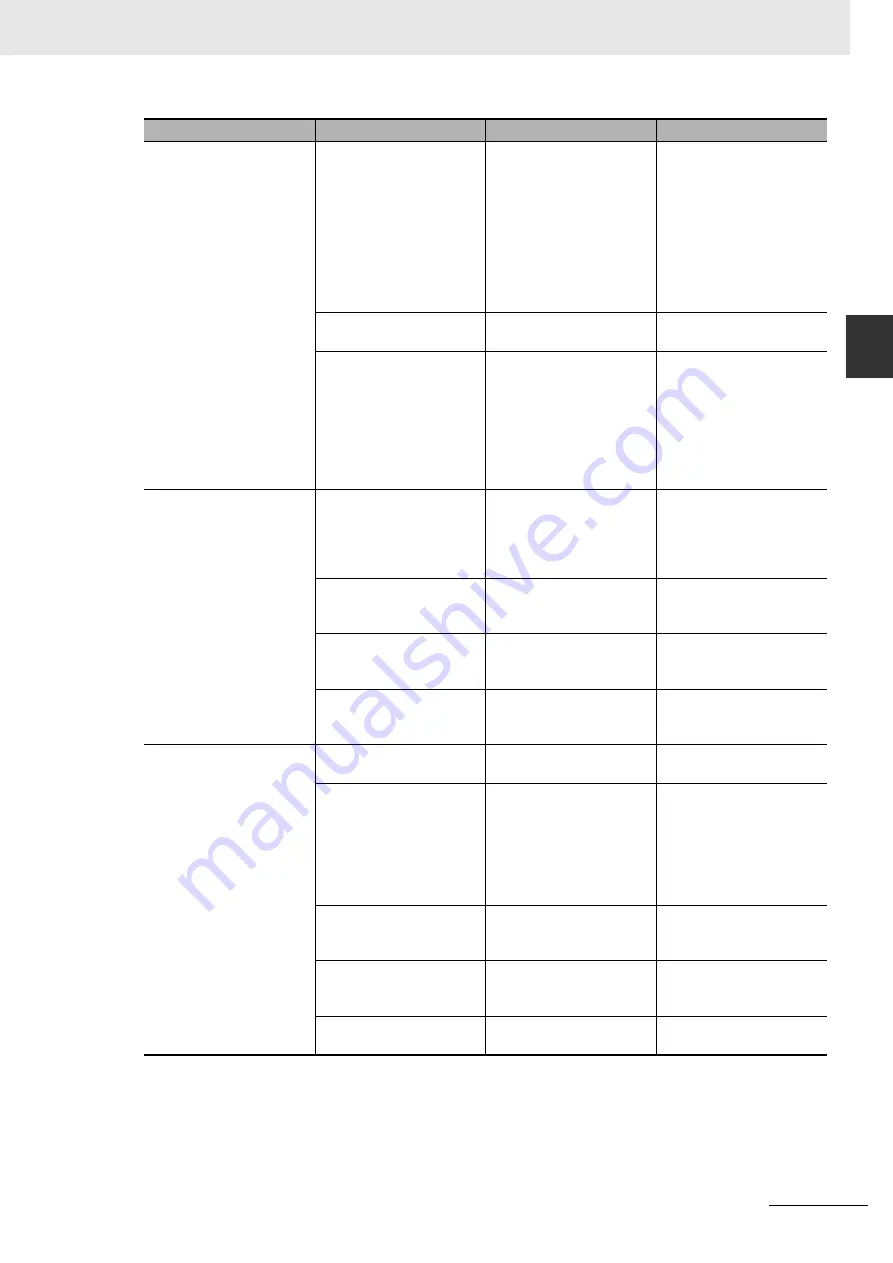
11-57
11 Troubleshooting
NJ-series CPU Unit Motion Control User’s Manual (W507)
11-2 T
ro
u
b
lesh
oo
tin
g
11
11-2
-3 Error Ca
uses and R
emedies
Operation cannot be
started, positioning is not
completed, or positioning
takes too much time to
complete.
The in-position range of
the Servo Drive is too nar-
row, and thus the current
position does not enter the
in-position range. (The
current operation does not
complete until the current
position enters the in-posi-
tion range, so you cannot
start the next motion.)
---
Increase the in-position
range.
Servo Drive gain is low.
---
Adjust the Servo Drive
gain.
The axis does not remain
in the in-position range
due to an external force.
Check the axis input infor-
mation for the Axis Vari-
ables to see if the
difference between the
command current position
and the actual current
position is within the in-
position range.
If you stop the axis so that
a position inside the in-
position range is not
achieved, such as holding
control, you can use the
following error reset output
to forcibly achieve the in-
position range.
Abnormal noise
Mechanical vibration
Check the moving parts of
the machine for intrusion
of foreign matter, dam-
age, deformation, and
loosening.
Correct the problem.
Insufficient adjustment of
the Servo Drive gain (high
gain)
---
Perform auto-tuning. Man-
ually lower the gain.
Incorrect Servomotor
selection (adjustment not
possible).
Select another motor
(check the torque and
inertia ratio).
Change to an optimal
motor.
Misalignment of the cou-
pling that connects the
motor shaft and machine
---
Adjust the motor and
machine installation.
Motor shaft shakes.
Insufficient adjustment of
the gain (low gain)
---
Perform auto-tuning. Man-
ually increase the gain.
Gain cannot be adjusted
due to low machine rigid-
ity.
In particular, this condi-
tion occurs on vertical
axes, SCARA robots, pal-
letizers, and other sys-
tems whose axes are
subject to bending or ten-
sional loads.
Increase the machine
rigidity. Readjust the gain.
Mechanical configuration
prone to stick slip (highly
sticky static friction)
---
Perform auto-tuning. Man-
ually adjust the gain.
Incorrect Servomotor
selection (adjustment not
possible)
Select an appropriate
motor (check the torque
and inertia ratio).
Change to an optimal
motor.
Failure
---
Replace the Servo Drive.
Replace the Servomotor.
Problem
Cause
Item to check
Countermeasure
Содержание NJ501-1300
Страница 12: ...Sections in this Manual 10 NJ series CPU Unit Motion Control User s Manual W507...
Страница 18: ...16 NJ series CPU Unit Motion Control User s Manual W507 CONTENTS...
Страница 22: ...Read and Understand this Manual 20 NJ series CPU Unit Motion Control User s Manual W507...
Страница 34: ...Revision History 32 NJ series CPU Unit Motion Control User s Manual W507...
Страница 44: ...1 Introduction to the Motion Control Function Module 1 10 NJ series CPU Unit Motion Control User s Manual W507...
Страница 58: ...2 Motion Control Configuration and Principles 2 14 NJ series CPU Unit Motion Control User s Manual W507...
Страница 86: ...3 Configuring Axes and Axes Groups 3 28 NJ series CPU Unit Motion Control User s Manual W507...
Страница 98: ...4 Checking Wiring from the Sysmac Studio 4 12 NJ series CPU Unit Motion Control User s Manual W507...
Страница 122: ...5 Motion Control Parameters 5 24 NJ series CPU Unit Motion Control User s Manual W507...
Страница 158: ...6 Motion Control Programming 6 36 NJ series CPU Unit Motion Control User s Manual W507...
Страница 166: ...7 Manual Operation 7 8 NJ series CPU Unit Motion Control User s Manual W507...
Страница 182: ...8 Homing 8 16 NJ series CPU Unit Motion Control User s Manual W507...
Страница 346: ...10 Sample Programming 10 92 NJ series CPU Unit Motion Control User s Manual W507...
Страница 422: ...Appendices A 18 NJ series CPU Unit Motion Control User s Manual W507...
Страница 423: ...Index 1 NJ series CPU Unit Motion Control User s Manual W507 I Index...
Страница 430: ...Index 8 NJ series CPU Unit Motion Control User s Manual W507 Index...