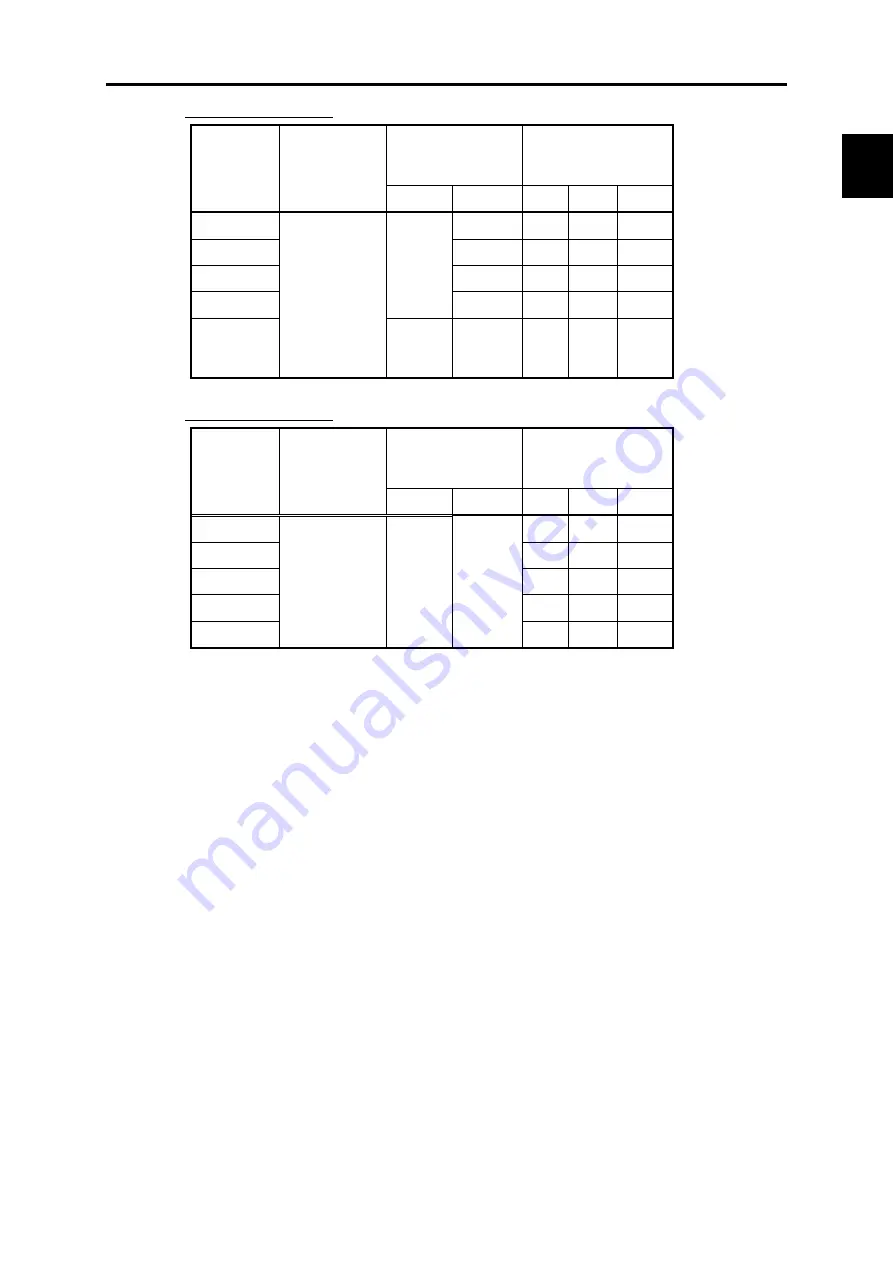
2.3 Overview of Function Code
C
hap.
2
FUN
CT
IO
N
C
O
D
E
S
Characteristics in F10=1
Applicable
motor rating
(kW)
Thermal time
constant
(Factory default)
Switching frequency
for motor
characteristic factor
Characteristic factor
(%)
f
2
f
3
α
1
α
2
α
3
2.2 to 4.0 kW
2 min
5 Hz
7 Hz
85
85
100
5.5 to 11 kW
6 Hz
90
95
100
15 kW
7 Hz
85
85
100
18.5, 22 kW
5 Hz
92
100
100
30 to 45 kW
Base
frequency
×
33%
Base
frequency
×
83%
54
85
95
Characteristics in F10=3
Applicable
motor rating
(kW)
Thermal time
constant
(Factory default)
Switching frequency
for motor
characteristic factor
Characteristic factor
(%)
f
2
f
3
α
1
α
2
α
3
2.2 to 4.0 kW
2 min
Base
frequency
×
33%
Base
frequency
×
83%
85
85
100
5.5 to 11 kW
90
95
100
15 kW
85
85
100
18.5, 22 kW
92
100
100
30 to 45 kW
54
85
95
■
Overload detection level (F11)
F11 specifies the level at which the electronic thermal overload protection becomes activated.
- Data setting range: 0.00 (Disable)
1 to 200% of the rated current (allowable continuous drive current) of the
inverter.
In general, set F11 to the allowable continuous drive current of the motor when driven at the rated
speed (i.e. 1.0 to 1.1 multiple of the rated current of the motor). To disable the electronic thermal
overload protection, set F11 to "0.00."
■
Thermal time constant (F12)
F12 specifies the thermal time constant of the motor. The time constant refers to the time required
for the electronic thermal overload protection to detect a motor overload when the current of 150%
of the overload detection level specified by F11 has flown continuously.
- Data setting range: 0.5 to 75.0 (min)
(Example) When F12 is set at "5.0" (5 minutes)
As shown below, the electronic thermal overload protection is activated to detect an alarm condition
(Alarm
OL1
) when an output current of 150% of the overload detection level (specified by F11)
flows for 5 minutes.
The actual activation time required for issuing a motor overload alarm tends to be shorter than the
one specified by F12 since it takes into account the time period from when the output current
exceeds the rated current (100%) until it reaches 150% of the overload detection level.
Example of Operating Characteristics
2-37
Содержание Frenic lift
Страница 1: ...LM2A series Reference Manual INR SI47 1909a E...
Страница 7: ......
Страница 13: ......
Страница 51: ...2 38...
Страница 221: ......
Страница 242: ...3 4 Programming Mode Chap 3 OPERATION USING TP A1 LM2 Figure 3 14 Screen transition for Op Monitor display example 3 21...
Страница 252: ......
Страница 254: ...URL http www fujielectric com...