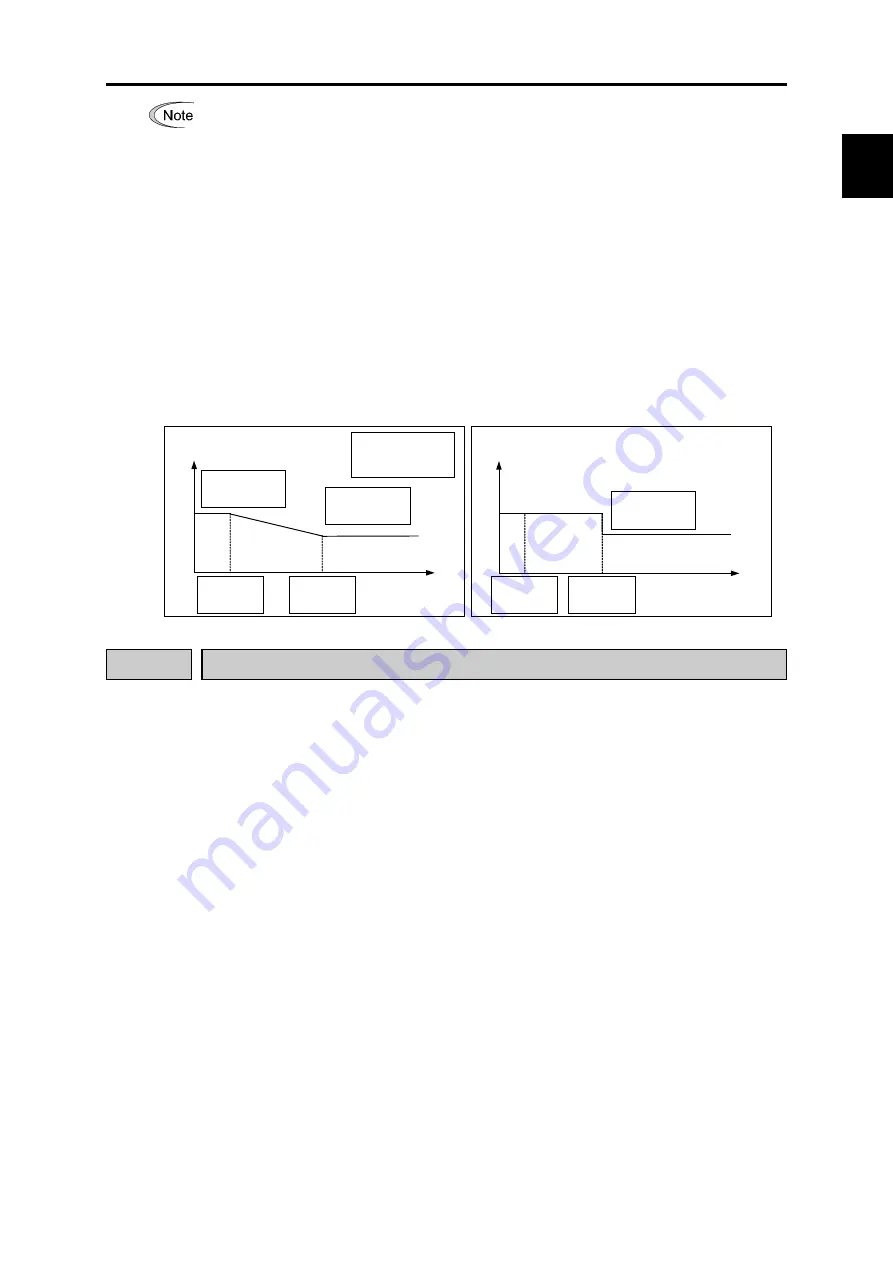
2.3 Overview of Function Code
C
hap.
2
FUN
CT
IO
N
C
O
D
E
S
An integral action refers to a delay component. The integral constant is the gain of the
delay component. Making the integral action highly responsive increases the delay
component, unstabilizing the control system including the motor and machinery. It takes
the form of overshooting or vibration.
One solution for the resonance of machinery generating abnormal mechanical noise from
the motor or gears is to increase the integral constant. If there is a requirement to not
delay response from machinery or equipment, examine the machinery causing the
resonance and take any necessary measures at the machinery side.
■
ASR switching speeds (L40 and L41)
L40 and L41 specify the speed at which the P and I constants to be applied are switched between the
ones for high speed (L36 and L37) and the ones for low speed (L38 and L39). The switching pattern
samples are shown below.
Note that if L41
≤
L40, the P and I constants are switched to the ones for high speed when the
switching speed specified by L40 is lower than the reference speed (final).
- Data setting range: 0.00 to 6000 (r/min)
ASR
P
constant and I constant
L38:
P
constant
L39: I constant
at low speed
L36:
P
constant
L37: I constant
at high speed
Reference speed
(final)
I constants (L37,
L39) are calculated
by 1/I formula
L41:
Switching
speed 2
L40:
Switching
speed 1
L40:
Switching
speed 1
L41:
Switching
speed 2
Reference speed
(final)
L36:
P
constant
L37: I constant
at high speed
ASR
P
constant and I constant
L42
ASR (Feed forward gain)
The FRENIC-Lift (LM2A) series of inverters supports the feed forward control that directly adds to
reference torque a torque value determined by derivation of the reference speed (final).
- Data setting range: 0.000 to 10.000 (s)
The PI control of the ASR is a feedback control. It monitors the result (detected speed) of the target
operation and deals with any deviation from the desired operation (reference speed (pre-ramp)) for
correction (for following the reference speed (pre-ramp)). The merit of this control is that it can
make corrections even for factors not directly measurable such as not measurable disturbance and
uncertainty of the control target. The demerit is that the control makes follow-up corrections after
detecting any deviation (reference speed (final) - detected speed) even for foreknown changes.
Since the operation quantity (reference torque) for foreknown factors can be obtained beforehand,
adding the quantity to the reference torque directly, the feed forward control can provide a highly
responsive control.
When the load inertia is foreknown, the feed forward control is effective. As shown on the next page,
the follow-up speed from the detected speed to the reference one is definitely different depending
upon whether the feed forward control is disabled or enabled. To get the maximal effect, it is
necessary to well balance the feed forward gain (L42) with the P and I constants (L36 to L39) of the
ASR.
2-153
Содержание Frenic lift
Страница 1: ...LM2A series Reference Manual INR SI47 1909a E...
Страница 7: ......
Страница 13: ......
Страница 51: ...2 38...
Страница 221: ......
Страница 242: ...3 4 Programming Mode Chap 3 OPERATION USING TP A1 LM2 Figure 3 14 Screen transition for Op Monitor display example 3 21...
Страница 252: ......
Страница 254: ...URL http www fujielectric com...