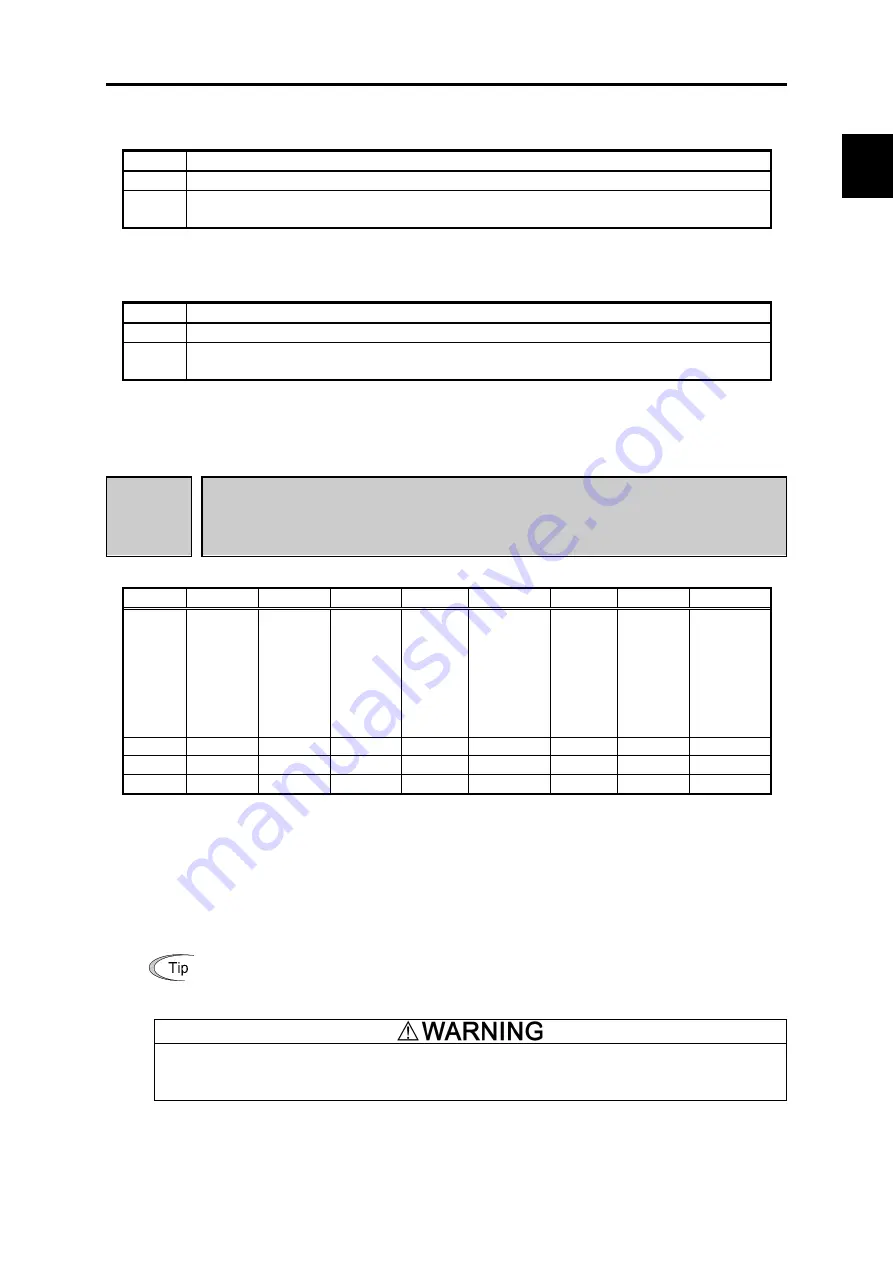
2.3 Overview of Function Code
C
hap.
2
FUN
CT
IO
N
C
O
D
E
S
ENOFF signal output mode (Bit 3)
ENOFF
output function behavior is selected by Bit 3. Behavior is descrived in below table.
Bit
Definition
0
ENOFF
signal means that EN1 and/or EN2 terminals are OFF (not active).
1
ENOFF
signal means that EN1 and/or EN2 terminals are OFF (not active) and RUN
command is ON.
Calculate ASR with only speed command during ULC (Bit 4)
ASR calculation method during ULC is defined by Bit 4. Behavior is descrived in below table.
Bit
Definition
0
Detected speed is used for ASR calculation during unbalanced load compensation.
1
Detected speed is assumed as 0 during unbalanced load compensation.
ASR works by using only reference speed from APR.
FAN ON/OFF during battery operation (Bit 6)
Normally is not necessary to change this bit.
L99
Control switch
P06 motor unload current
L56 torque bias (torque reference finish timer)
L57 torque bias (limit)
L80 brake control operation selection
By setting L99, operations of inverter can be enabled/disabled.
Bit
Bit 7
Bit 6
Bit 5
Bit 4
Bit 3
Bit 2
Bit 1
Bit 0
Function
Not
assigned
DOPEN
function
change
S1 bit
selection
for DCP
Rise
direction
definition
Short floor
operation
using
s-curve
control
driving
Initial
torque
bias and
reference
torque
decreasin
g
Magnetic
pole
position
offset
Current
confirmation
for
synchronous
motor
Data=0
-
Disable
SW52-2
FWD
Disable
Disable Disable
Disable
Data=1
-
Enable
SW52-3
REV
Enable
Enable
Enable
Enable
Default
0
0
0
0
0
0
1
0
■
Current confirmation for synchronous motor (Bit 0)
In case of controlling synchronous motor, the output current is proportional to the output torque.
Therefore, theoretically, the output current is 0 before releasing the brake. In this case, even if the
output phase is lost, it is impossible to detect it. This function can be used to ensure an output higher
than the setting in P06. Please use this function when lift controller uses ID or ID2 as brake release
condition in case that the inveter is controlling a synchronous motor.
By using the function, it is possible to confirm the connection between inverter and
synchronous motor at stop condition.
If this function is used, the recommended value of P06 is less than 5% of the motor rated current.
Otherwise injuries could occur.
■
Magnetic pole position offset (Bit 1)
The tuning result by
PPT
is saved (written) or read.
Refer to the explanation of
PPT
for details.
2-175
Содержание Frenic lift
Страница 1: ...LM2A series Reference Manual INR SI47 1909a E...
Страница 7: ......
Страница 13: ......
Страница 51: ...2 38...
Страница 221: ......
Страница 242: ...3 4 Programming Mode Chap 3 OPERATION USING TP A1 LM2 Figure 3 14 Screen transition for Op Monitor display example 3 21...
Страница 252: ......
Страница 254: ...URL http www fujielectric com...