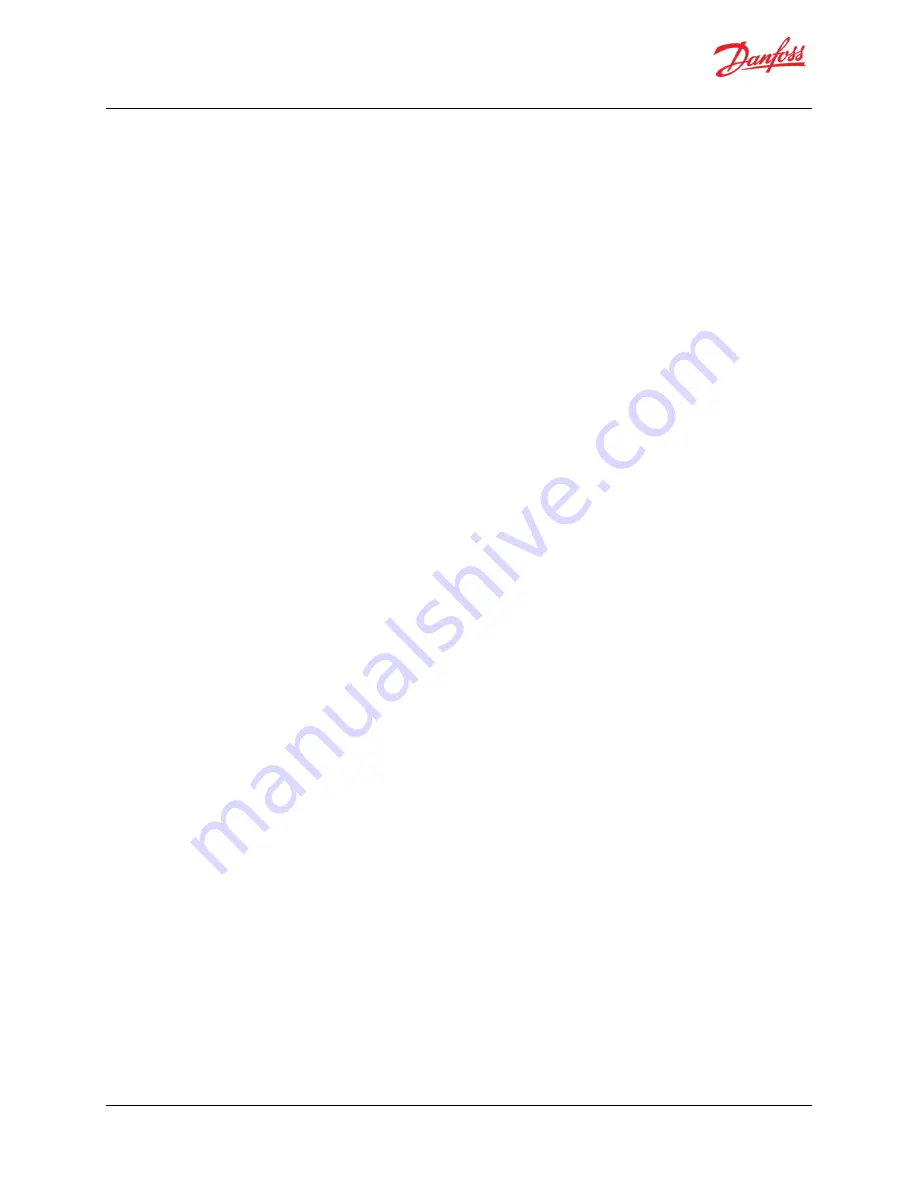
Installation and Operation Guide
ED-DT318B
Drive Train Systems with Traction Control, Inverter/Controller, and Motor with 2 Speed Transmission
BC353060341319en-000101
Revision D
© Danfoss | November 2020 | 54
Classified as Business
6
Communications
This section covers the CAN communications required for normal motor operations and RS232 communications
required by the diagnostic software.
6.1
VCU to TCU CAN Communications
The user is responsible for connecting the CAN communication from the VCU to the TCU and the Diagnostic
Connector (see
for the Drivetrain Interface Connector pinout and
for the Diagnostic
Connector pinout).
Please follow the typical CAN setup procedures according to J1939.
Note that the CAN bus connecting the VCU to the TCU has two sets of leads in the Drivetrain Interface
Connector: VCU CAN Leg A (pins 1, 2 & 3) and VCU CAN Leg B (pins 4, 5 & 6). Both should be used as they are
provided to preserve the integrity of the daisy chain for that bus. If the user elects to place the TCU at the end of
the daisy chain, the 120Ω terminating resistor should be connected to the unused signal pins (I.e.: if all of the
other devices on the CAN bus are connected to VCU CAN Leg A, the termination resistor should be connected
between VCU CAN Leg B + and VCU CAN Leg B -). If the user does not wish to place the MCU at the end of the
daisy chain, both sets of signal pins should be used. The user should not splice to one set of pins and leave the
other open.
shows the allowed CAN bus configurations.
The VCU to TCU CAN Bus can support the following configurations:
Baud Rate
•
250 kbps
•
500 kbps
Message Format
•
PDU1 (29 bit)
•
PDU2 (29 bit)
•
CANOpen (11 bit)
Bit Order
•
Little Endian
The default configuration is 250 kbps, PDU1, Little Endian. If another combination is needed, please contact your
Danfoss Power Solutions representative to obtain a customer specific TCU configuration and matching dbc file.
6.2
TCU to MCU CAN monitor
Danfoss Power Solutions also provides access to the TCU to MCU CAN bus via the Diagnostic Connector. This
access allows monitoring of communications between the TCU and MCU. It also used to update TCU and MCU
firmware and TCU configuration data. The MCU configuration is updated via the RS232 port documented below.
TCU to MCU CAN bus. Note that the wiring from the MCU to the TCU is provided by Danfoss Power Solutions via
the TCU to MCU Interface Cable (Cable C in
). The customer is responsible for the wiring from the
Drivetrain Interface Connector to the Diagnostic Connector.
The CAN configuration for the TCU to MCU CAN bus is 500 kbps, PDU1, Little Endian.
Содержание ED-DT318B
Страница 185: ......