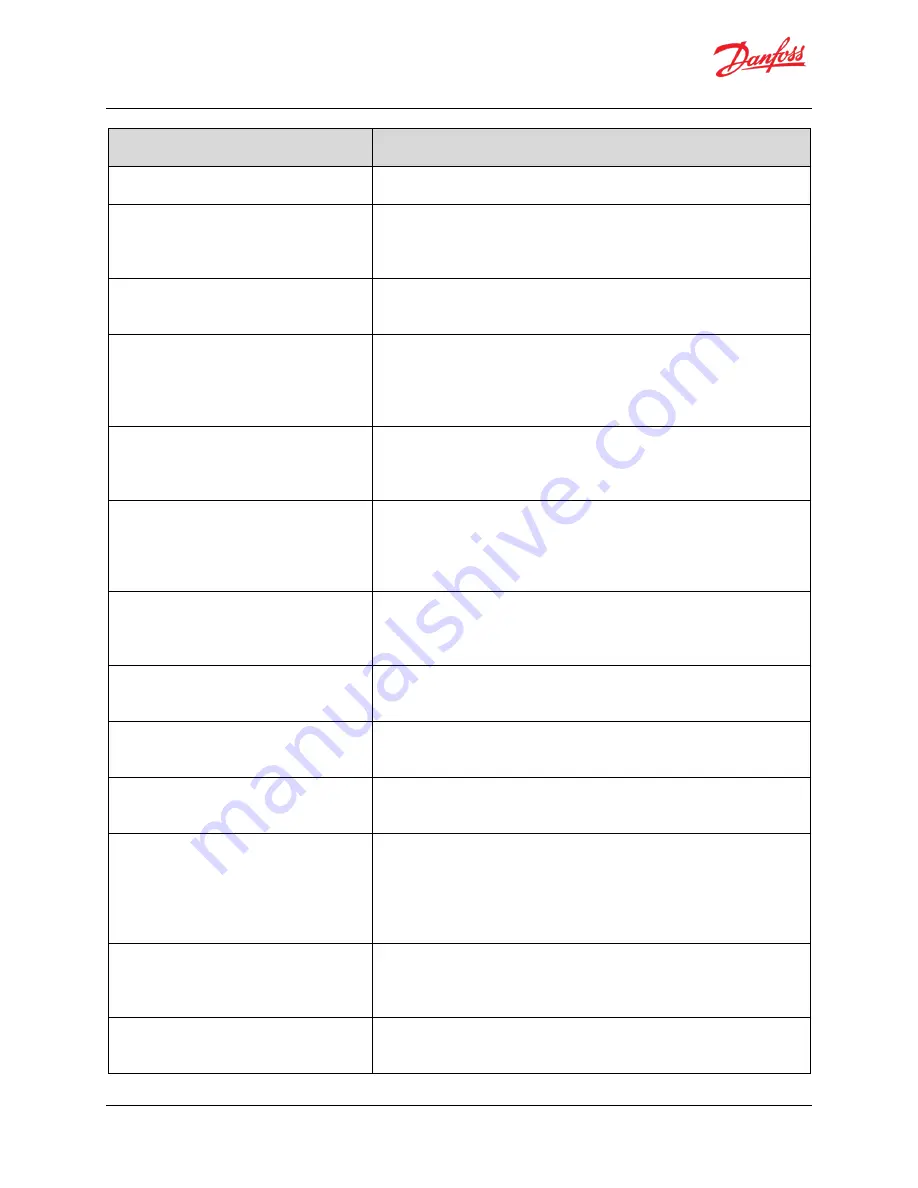
Installation and Operation Guide
ED-DT318B
Drive Train Systems with Traction Control, Inverter/Controller, and Motor with 2 Speed Transmission
BC353060341319en-000101
Revision D
© Danfoss | November 2020 | 150
Classified as Business
Entries
Description
Bad rotor temperature occurred
The rotor temperature sensor is suspect.
Inverter Temp Shutdown
Rotor Temp Shutdown
Stator Temp Shutdown
These events mark when temperatures exceeded limits, causing
the power switches of the inverter to shut down.
Over Positive Phase Advance ONCE
Under Negative Phase Advance ONCE
These events mark when the controller has encountered the phase
limits of the motor.
Position signal is bad
Position signal has come good
Position error is too large
Apparent rotor movement occurred
These events mark a problem or the resolution of a problem with
the position sensor signals. Either a cable was removed or the
position offset is suspect.
Mechanical revolution count occurred
The user configurable number of motor revolutions has occurred.
This entry will be made each time that counter counts this number
of revolutions.
CANbus watchdog occurred
CANbus commands ceased. This is sometimes seen benignly
because the vehicle controller is powered off and is no longer
communicating, but the motor controller has not yet been
powered off.
Torque matching problem
The controller found that it was unable to control the motor to the
desired torque. If this occurs regularly, this could be because the
motor has partially demagnetized.
Back EMF saturated high
Back EMF saturated low
The dynamic motor tuning control could not find the motor’s Back
EMF. Indicates that the wrong motor is connected.
Low Forced Voltage Control Occurred
The controller went into forced voltage control because of
dangerous low voltage conditions.
Disconnected Battery Event Occurred
The controller detected conditions that indicated no power supply
connection. This condition often results in forced voltage control.
Noisy position < 1 Hz
Noisy position < 150 Hz
Noisy position < 250 Hz
Noisy position < 350 Hz
Noisy position > 350 Hz
Electrical noise occurred on the position signals. This is a
potentially dangerous condition because it could cause motor
miscommutation if this rate is greater than 150 Hz.
Regen Switch closed
Regen Switch open
Indicates the state of the 7th power switch in the inverter, called
the Regen Switch. It isolates the inverter when high voltage or high
regeneration current occurs.
Stalled OFF
Stalled ON
These events mark when the controller severely limited torque
while the motor could not spin.
Содержание ED-DT318B
Страница 185: ......