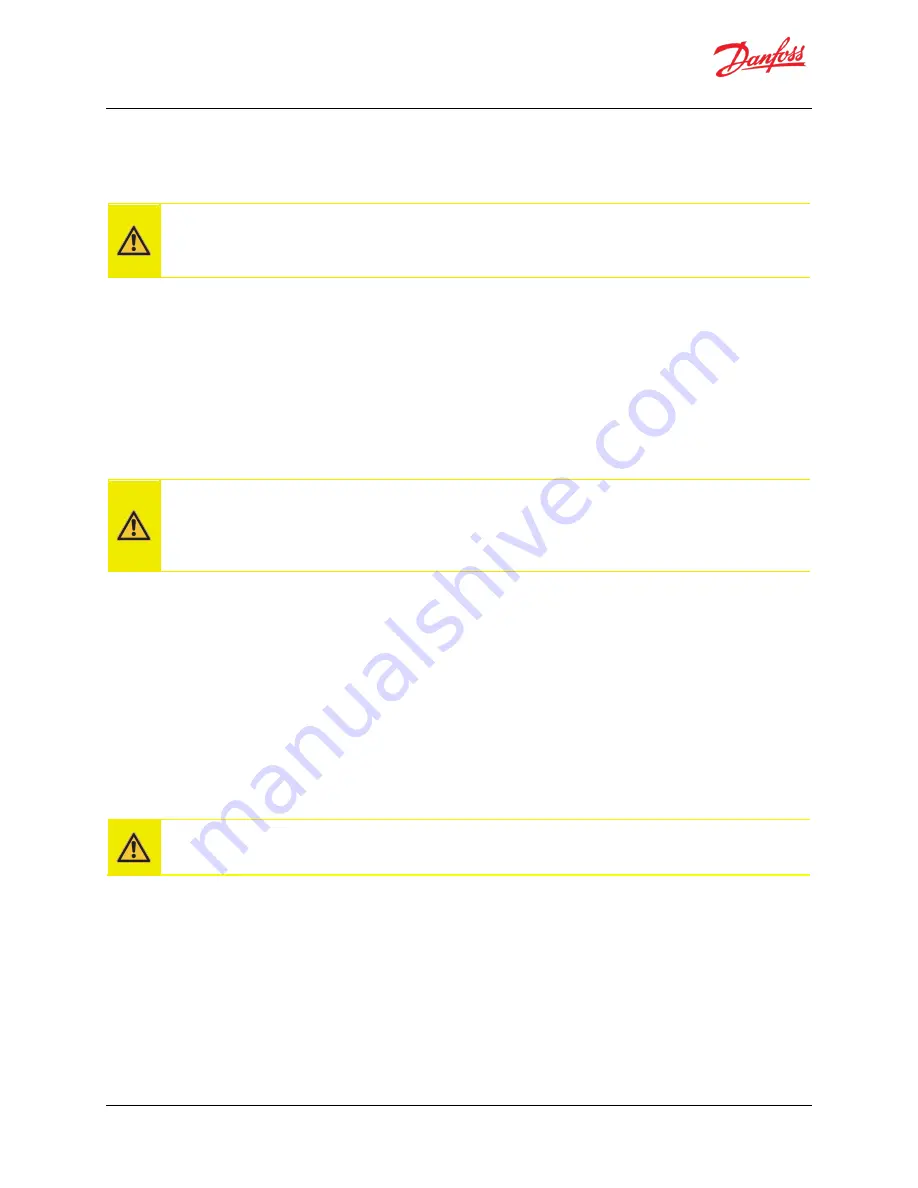
Installation and Operation Guide
ED-DT318B
Drive Train Systems with Traction Control, Inverter/Controller, and Motor with 2 Speed Transmission
BC353060341319en-000101
Revision D
© Danfoss | November 2020 | 15
Classified as Business
2.2.2
Vibration Considerations
The controller is to be mounted to the vehicle frame that is supported by the suspension system of the vehicle.
CAUTION
Vibration isolators at the mounting points of the controller are required when the
vehicle vibration levels at the controller mounting location are in excess of typical
automotive or commercial vehicle levels.
Danfoss Power Solutions has qualified the controller to the vibration levels stated in Appendix A
. It is the responsibility of the integrator or vehicle manufacturer to determine the vibration levels in the
application and when necessary, specify, install and maintain the vibration isolators.
2.2.3
Cable Routing
Route the cables in a way that avoids unnecessary binding and premature wear. Do not locate connections in
close proximity to any surface or connector that could short the motor leads.
CAUTION
The customer must route and secure the Phase Cables, DC Cable, Signal Cable, and
TCU to MCU Interface Cable and Drivetrain Control Cables in such a manner as to
ensure that connector housings and sealing interfaces are not stressed during
installation or operation.
2.2.4
Preparing the Coolant Loop for MCU and Motor
Danfoss Power Solutions requires that the controller be the first component in the coolant loop. The controller
coolant ports function as either inlet or outlet. The performance of the system is not impacted by which
controller coolant port is used for inlet or outlet. The temperature of the coolant going to the controller must not
exceed 60
°
C to achieve full performance (reference the flow rates in ICD).
The coolant fittings on the controller are intended for a 20mm hose. The coolant must have a minimum flow of
10 LPM.
If the customer elects to use the Eaton 5586750 heat exchanger (oil to water) to cool the transmission lubrication
fluid, the coolant supply to the cooler must
Not
be in line with the inverter or the motor.
CAUTION
Never allow the controller to operate unless the coolant is flowing at a minimum flow
rate of 10 LPM.
There is no restriction on the maximum coolant flow. However, the system is designed for a maximum operating
pressure of 30 PSI.
2.2.5
Routing the Signal Cable
The Signal Cable (cable E in
) contains information about the position of the rotor, and the
temperatures of the motor’s rotor and stator. The controller depends on that information to properly control the
motor. The data integrity of the Signal Cable is necessary for optimum operation and care must be taken to
ensure the reliability of these signals.
Содержание ED-DT318B
Страница 185: ......