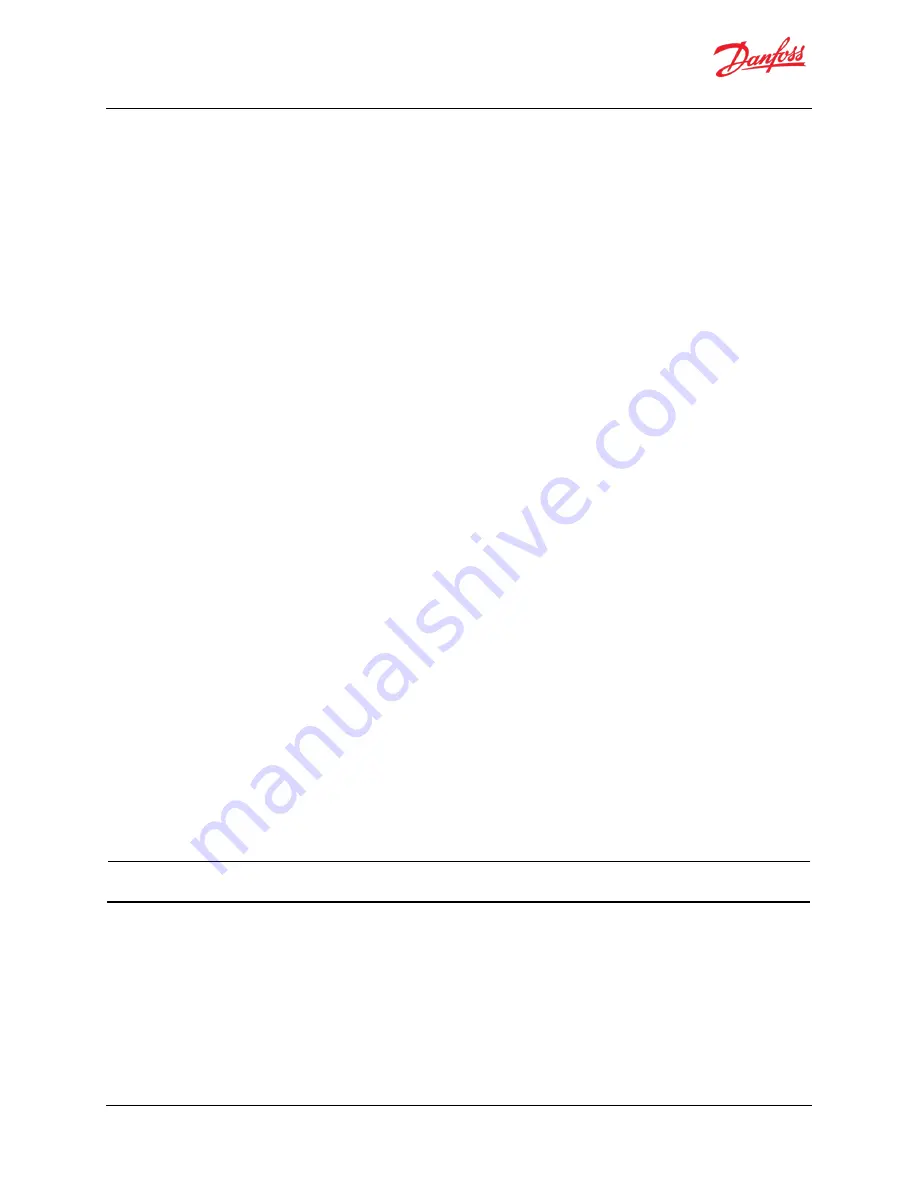
Installation and Operation Guide
ED-DT318B
Drive Train Systems with Traction Control, Inverter/Controller, and Motor with 2 Speed Transmission
BC353060341319en-000101
Revision D
© Danfoss | November 2020 | 32
Classified as Business
Install the phase cable housing (the metal block holding the phase cables together) to the controller housing
and secure it using the included M6x1x16 socket head cap screws (SHCS) and tighten to the torque indicated in
the ICD drawing.
The phase cable housing is keyed to the controller housing so it can only be installed in the correct orientation.
After installation, the holes in the ring lugs at the end of the phase cables should line up with the threaded holes
at the terminals of the controller.
Install three of the included M8-1.25 x20 flanged head bolts through the ring lug holes (
), and thread
them into the holes in the controller terminals. Tighten to the indicated torque in the ICD drawing.
3.1.2
DC Cables
The DC Cables (
cable F) supplies DC voltage from the high voltage power source to the inverter.
DC cables must have a dedicated set of contactors and fuses with appropriate ratings between the motor
controller and the DC High voltage battery.
Install the DC cable housing (the metal block holding the DC cables together) to the controller housing and
secure it using the included M6x1x16 socket head cap screws (SHCS) and tighten to the torque indicated in the
ICD drawing.
The DC cable housing is keyed to the controller housing so it can only be installed in the correct orientation.
After installation, the holes in the ring lugs at the end of the DC cables should line up with the threaded holes at
the terminals of the controller.
Install two of the included M8-1.25 x20 flanged head bolts through the ring lug holes (
), and thread
them into the holes in the controller terminals. Tighten to the indicated torque in the ICD drawing.
At rated peak power of the ED-DT318B system at the nominal voltage (both stated in the specific product
specification sheet available through Danfoss Power Solutions sales); the Danfoss Power Solutions controller can
draw over 650 Amps from the traction battery. Internal impedances inside the customer’s battery can drop the
voltage supplied to the Danfoss Power Solutions controller.
The ripple voltage on the high voltage power supply should be less than 10 V peak-to-peak at all current levels.
Before applying input high voltage, ensure that the shaft, and anything connected to the shaft, has sufficient
area for rotation. Also make sure that the motor is secured to something that can handle the reactionary torque
from the motor. As the rotor accelerates, the motor case attempts to torque in the opposite direction. Always
disconnect input high voltage before making or removing any connections.
Due to the high inrush current of charging the controller’s internal capacitors, the customer
must
ensure that the
high voltage system has proper fusing and contactor configuration to ensure proper system start-up. Danfoss
Power Solutions recommends some type of “soft start” circuit, which is the responsibility of the user and/or high
voltage battery pack manufacturer.
NOTICE
A soft start circuit is recommended for input voltages above 100 V High Voltage DC.
3.1.3
High Voltage Interlock Connection
The High Voltage Inter-Lock (HVIL) connections must be made for the system to operate safely.
The HVIL circuit is a continuity path “daisy chain” that starts at the User Interface connector, on the controller.
The HVIL continues internally through the controller to the controller termination cover switch (closed when
cover is on) then thru the position cable to the motor termination cover switch (closed when cover is on). From
the switch in the motor back to the User Interface connector, see block diagram of the circuit (
Содержание ED-DT318B
Страница 185: ......