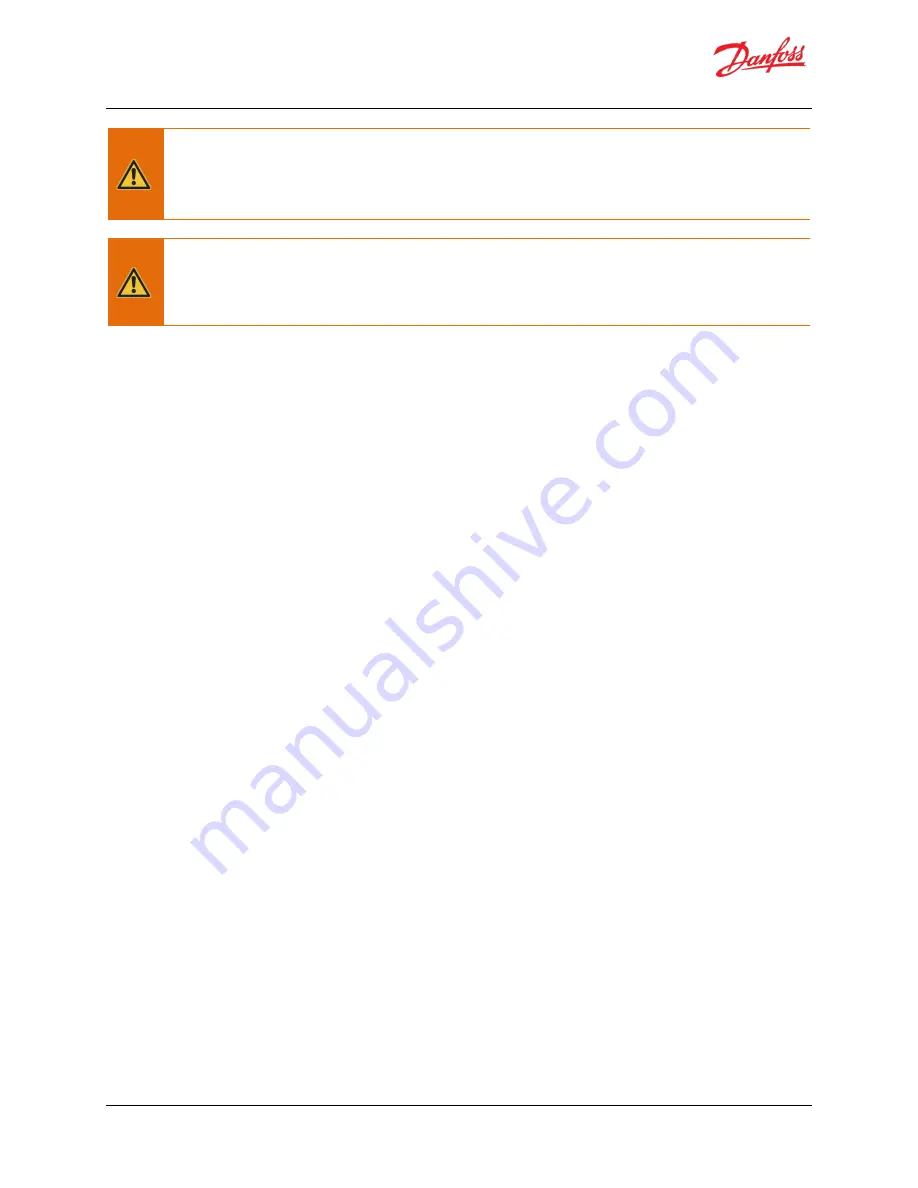
Installation and Operation Guide
ED-DT318B
Drive Train Systems with Traction Control, Inverter/Controller, and Motor with 2 Speed Transmission
BC353060341319en-000101
Revision D
© Danfoss | November 2020 | 49
Classified as Business
WARNING
DO NOT FLAT TOW the vehicle. While towing the vehicle, the drive wheels MUST
NOT ROTATE,
or
damage will result when the motor system is not operational. If
needed, the drive shaft should be disconnected from the transmission output
flange.
WARNING
DO NOT RE-ENABLE BATTERY VOLTAGE TO A MOVING VEHICLE.
It is strongly
recommended that if a condition occurs which requires power cycling the system, the
vehicle should be at a full stop before battery power is enabled. Applying battery voltage
while the motor is moving may result in serious damage to the system.
5.2
Valid Control Modes via CAN
The only Control Mode in the Danfoss Power Solutions PowerPhase
®
DT2 System is CANbus Control. Control
commands are issued by the VCU to the TCU via the CANbus. The TCU only recognizes one mode of operation:
torque production with a speed limit.
5.2.1
Special Features
The MCU has a number of special features which can simplify vehicle control, improve system efficiency, and
help with electric vehicle ride comfort. In the following section acceleration limiting will be discussed.
5.2.2
Acceleration Control
While fast acceleration is desirable, too much acceleration can cause poor riding comfort and excessive
mechanical stress. All vehicles have a natural maximum acceleration limit due to the mechanical systems
themselves and their environment. In addition, some applications have mandated limits to the acceleration
experienced by vehicle riders.
Danfoss Power Solutions’ Acceleration Limit feature attempts to control the acceleration of the electric motor to
a user-defined level, allowing simplification of the vehicle control algorithms during terrain changes. With the
same command sequence, more torque can be used going uphill and less torque be used going downhill,
providing the vehicle occupants with identical experiences in both cases.
The Acceleration Limit is set dynamically through a CANbus command (see the
Section
for details).
Acceleration Limit causes the Danfoss Power Solutions controller to use less torque if motor acceleration
exceeds the user-defined level. Note that it can only
remove
torque. It does not try to maintain the acceleration
rate unless too much torque is requested. Thus, a controlled deceleration requires a negative torque (regen)
request, and a controlled acceleration requires a positive torque request.
For example, if an Acceleration Limit of 150 RPM/sec is set and a full torque request is issued to the Danfoss
Power Solutions controller while the motor is at rest, then the Danfoss Power Solutions controller could deliver
up to full torque to get the motor spinning. As the motor begins to spin, the controller will lessen the torque
delivered to maintain an acceleration of 150 RPM/sec. The controller maintains this acceleration
while the torque
request is greater than required to achieve an acceleration rate of 150rpms
.
If the torque request drops to zero, torque will immediately be removed. If a negative torque request is issued at
this point, the Danfoss Power Solutions controller will deliver the requested regeneration torque (or less) in
order to maintain a 150 rpms deceleration.
Содержание ED-DT318B
Страница 185: ......