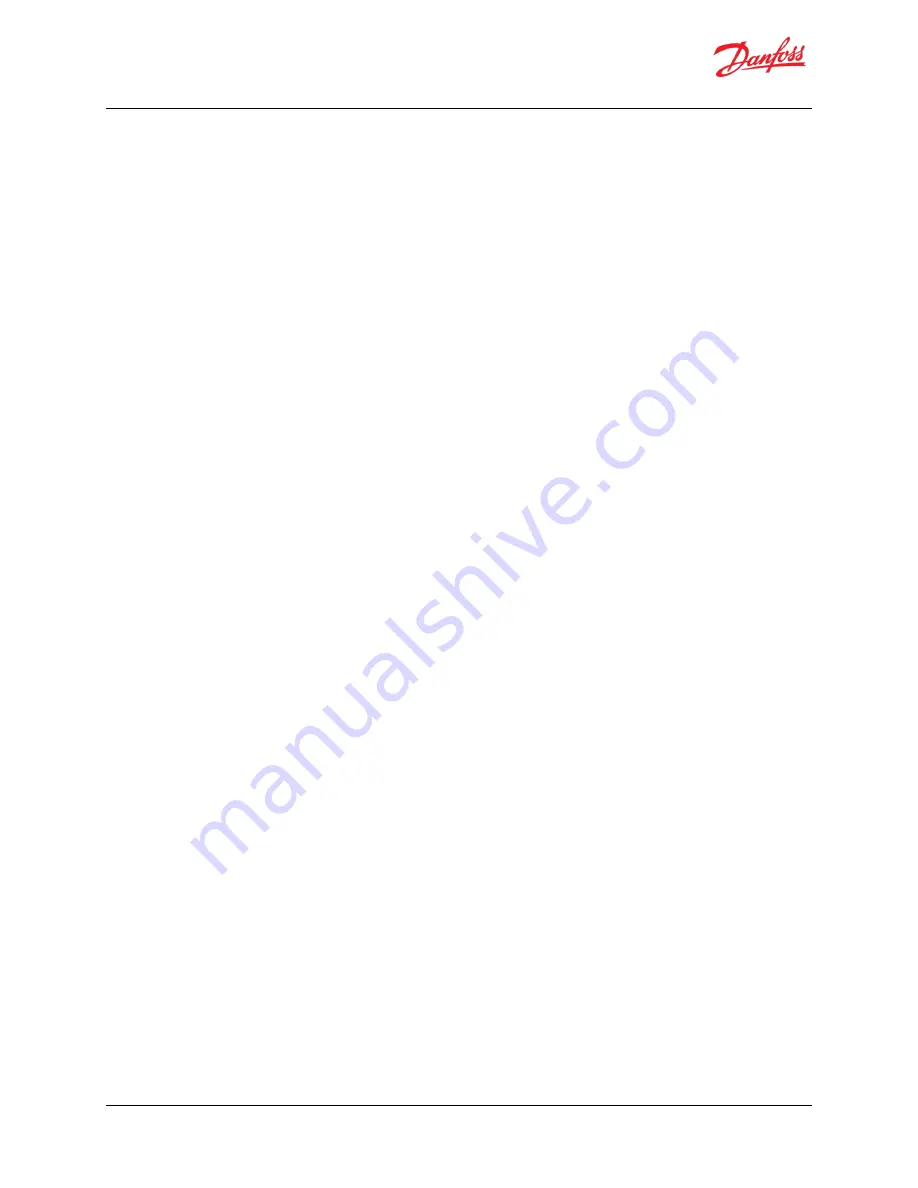
Installation and Operation Guide
ED-DT318B
Drive Train Systems with Traction Control, Inverter/Controller, and Motor with 2 Speed Transmission
BC353060341319en-000101
Revision D
© Danfoss | November 2020 | 52
Classified as Business
5.3.2
Forced Voltage Control
Forced voltage control ensures the bus voltage of the inverter does not exceed the limits of the inverter’s
components. This condition may occur if the high voltage path is suddenly removed, for example, if a battery
contactor opens.
If the motor is regenerating when the high voltage path is suddenly removed, then the bus voltage experienced
by the inverter can rise very rapidly, endangering inverter components. This is detected as a
Disconnected
Battery Event
. It will occur if, over a 2 millisecond period, the bus current is very small but the voltage change
indicates that significant currents are flowing into the inverter’s capacitors.
If the motor is motoring when the high voltage path is suddenly removed, the bus voltage experienced by the
inverter can fall very rapidly, threatening a power device shutdown. This is detected as a
Low Forced Voltage
Event
. It will occur if all of the following are happening: bus current is small, the bus voltage is less than the
minimum allowed battery value and dropping fast, and the inverter is seeing large motor currents OR the speed
is above base speed.
Danfoss Power Solutions inverters monitor for these conditions and enter the control mode “Forced Voltage
Control” in order to control the bus voltage by motoring or regenerating rapidly. While in control, Forced
Voltage Control maintains the voltage 10 V below the maximum battery voltage defined in the System
Configuration. Note that if the regen switch is open then it will control the voltage to a higher value. This control
mode is only allowed to use 10% of the motoring and regeneration capabilities of the Danfoss Power Solutions
motor. The mode releases control within 128 milliseconds if conditions indicate that the battery is still
connected. This condition is reported through the Diagnostic Software described in
Section 8
of this manual,
and also through the MCU Limp Home Mode signal (
Section 7.3.3.5
5.3.3
Stall
If the motor’s rotor does not move when high torque is commanded, the result is a stalled condition in the
motor. A rotor locked in this way can cause the current through the inverter to exceed safe limits. If unchecked,
these high currents will cause the failure of an IGBT power device in the inverter. To protect against a prolonged
stall condition (locked rotor); Danfoss Power Solutions controllers contain a complex algorithm to deliver the
requested torque for as long as possible without damaging the power devices. The amount of time is variable
and contingent on the amount of torque requested. It can range from many seconds down to 600 milliseconds.
Once this time has elapsed, the Stall Limit will report a stall condition and limit the torque to 10% for 30 seconds.
This condition is reported through the Diagnostic Software described in
Section 8
of this manual, and also
through the MCU Stall Condition Active signal (
Section 7.3.2.36
5.3.4
Forced Open Loop
In normal operation, the controller uses measured values from the motor to tune and improve control. In the
case of detected measurement failure, control is managed with open loop values. The conditions that cause this
include Invalid Sensor voltage, Error with leg current sensors, Current sensors appear disconnected, and bad
controller calibration. Each significantly limits torque output, but the motor is allowed to operate in a “limp-
home” mode. This condition is reported through the Diagnostic Software described in
Section 8
of this manual,
and also through the MCU Forced Open Loop signal (
Section 7.3.2.37
5.3.5
Software Watchdog Timer
In addition to all limit protections discussed above, a software watchdog timer is also enabled. If the watchdog
timer is not maintained properly by the inverter’s firmware, the system will be reset automatically.
Содержание ED-DT318B
Страница 185: ......