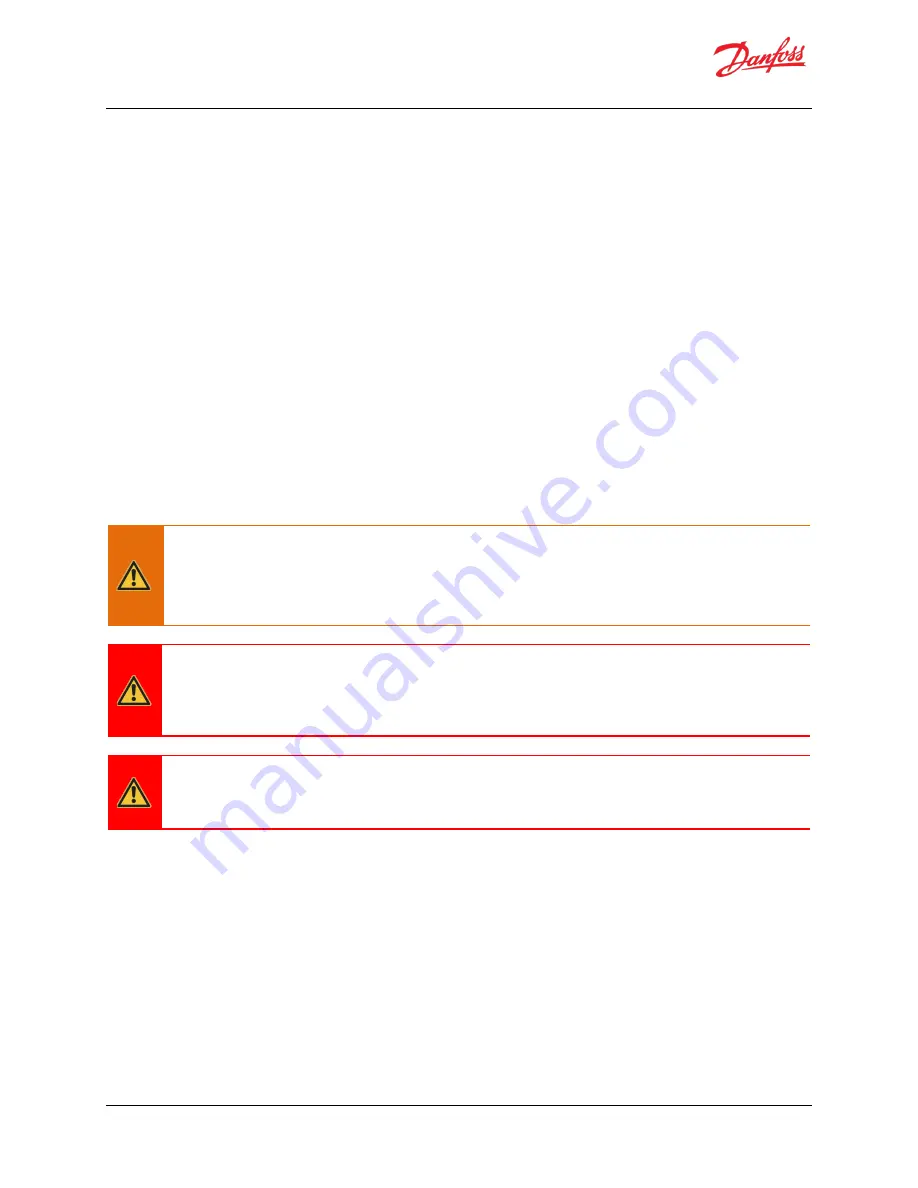
Installation and Operation Guide
ED-DT318B
Drive Train Systems with Traction Control, Inverter/Controller, and Motor with 2 Speed Transmission
BC353060341319en-000101
Revision D
© Danfoss | November 2020 | 38
Classified as Business
the TCU at the end of the daisy chain, the 120Ω terminating resistor should be connected to the unused signal
pins. If the user does not wish to place the MCU at the end of the daisy chain, both sets of signal pins should be
used. The user should not splice to one set of pins and leave the other open.
shows the allowed VCU
CAN bus configurations.
The User Interface Connector also provides the 24 V battery voltage used to power the TCU and the MCU.
The pin assignments and wire sizes for the User Interface Connector are defined in
Danfoss Power Solutions recommends that the 24 volt supply voltage be controlled by the VCU and that it be
fused using an automotive rated 10 amp fuse between on the low voltage lines to the controller/invertor. Treat
this low voltage 24V supply as you would the ignition source for a gasoline powered vehicle. The 24V line must
be at least 14 gauge wire to avoid a voltage drop in the wire supplying LV to the controller. Note that the kit
(Danfoss Power Solutions part # 98010-022) supplied with the PowerPhase
®
DT2 system provides terminals
(Danfoss Power Solutions part # 15010-083) and wire seals (Danfoss Power Solutions part # 15010-019)
appropriate for use with 14 G wire.
Danfoss Power Solutions recommends that the CAN and RS232 serial cables be 18 gauge, 2 conductor, shielded
stranded twisted pair wire equivalent to the Danfoss Power Solutions part number 14020-019 as specified in
Please note that all user interface control signals are isolated from the high voltage DC bus and should not be
referenced in any way to the high voltage DC bus supply.
WARNING
CYCLING THE
+
24V OR ENABLE SIGNAL WHILE THE MOTOR IS IN MOTION SHOULD
BE AVOIDED IF AT ALL POSSIBLE.
Cycling either of these signals will cause the inverter CPU to shut down and restart –
which may result in unpredictable current surges.
DANGER
Your system may be configured for rotation when input voltage is applied. Before
applying input voltage, ensure that the shaft and/or anything connected to the shaft
has sufficient area for rotation. Always disconnect input voltage before making or
removing any other connections.
DANGER
Do not connect either the positive or negative high voltage bus to the chassis, motor
cases, or controller. Catastrophic damage may occur. Provide sufficient insulation on
all power terminals for safety.
Содержание ED-DT318B
Страница 185: ......